
The full 5-axis VARIAXIS i-600 NEO machines multiple and complex curved surfaces on small and medium-sized workpieces in single setups for shorter production cycle times.
A 40-taper, 18,000rpm high-rigidity spindle provides versatility in cutting applications from heavy-duty machining to high-speed cutting of aluminum and other nonferrous materials.
Temperature-controlled cooling oil circulates around the spindle bearings, headstock, and ball screw cores to minimize spindle thermal change and allow high-speed operation.
Full gantry machine construction minimizes vibration during acceleration/deceleration for stability. High-rigidity and lower friction linear roller guides on the X-, Y- and Z-axis provide precise positioning and enable fast feedrates.
MAZATROL SmoothAi control technologies’ SMOOTH Ai Spindle automatically optimizes spindle speed based on sensor feedback, minimizing machining vibration for superior part surface finishes. Ai Thermal Shield adapts and learns from environmental changes to control the effects of heat on machining accuracy.
Mazak Corp.
https://www.mazak.com
5-flute solid end mills

The latest addition to a family of high-performance end mills, the HARVI II TE 5-flute end mill is designed for increased metal removal rates (MRR) and longer tool life while supporting high-speed and deep cuts. Its novel centerless end face design contributes to its increased flexibility across applications and material types. It delivers increased stability and stiffness in dynamic and traditional milling operations and on a much wider range of materials.
Kennametal Inc.
https://www.kennametal.com
In-process mini gage

The Protomar Mini measuring gage – capable of pre-, in-, and post-inspection – addresses the trend toward smaller, more flexible machine tools. Measuring 60.2mm x 258mm x 319mm, its compact design fits grinding machines with limited space.
Applications include use in multi-diameter machines, such as grinders for broaches or turbine blades. Setting it apart from conventional measurement systems is its ability to eliminate the setup and zeroing procedure on a master workpiece for diameters across its measuring range. It provides absolute measurements across its 100mm measuring range, eliminating the need for retooling when changing diameters. Operators can achieve 2.5μm measurement repeatability.
It integrates into the Marposs BLÚ advanced control network connecting all monitoring sensors within a machine using a single bus cable.
Marposs Corp.
https://www.marposs.com
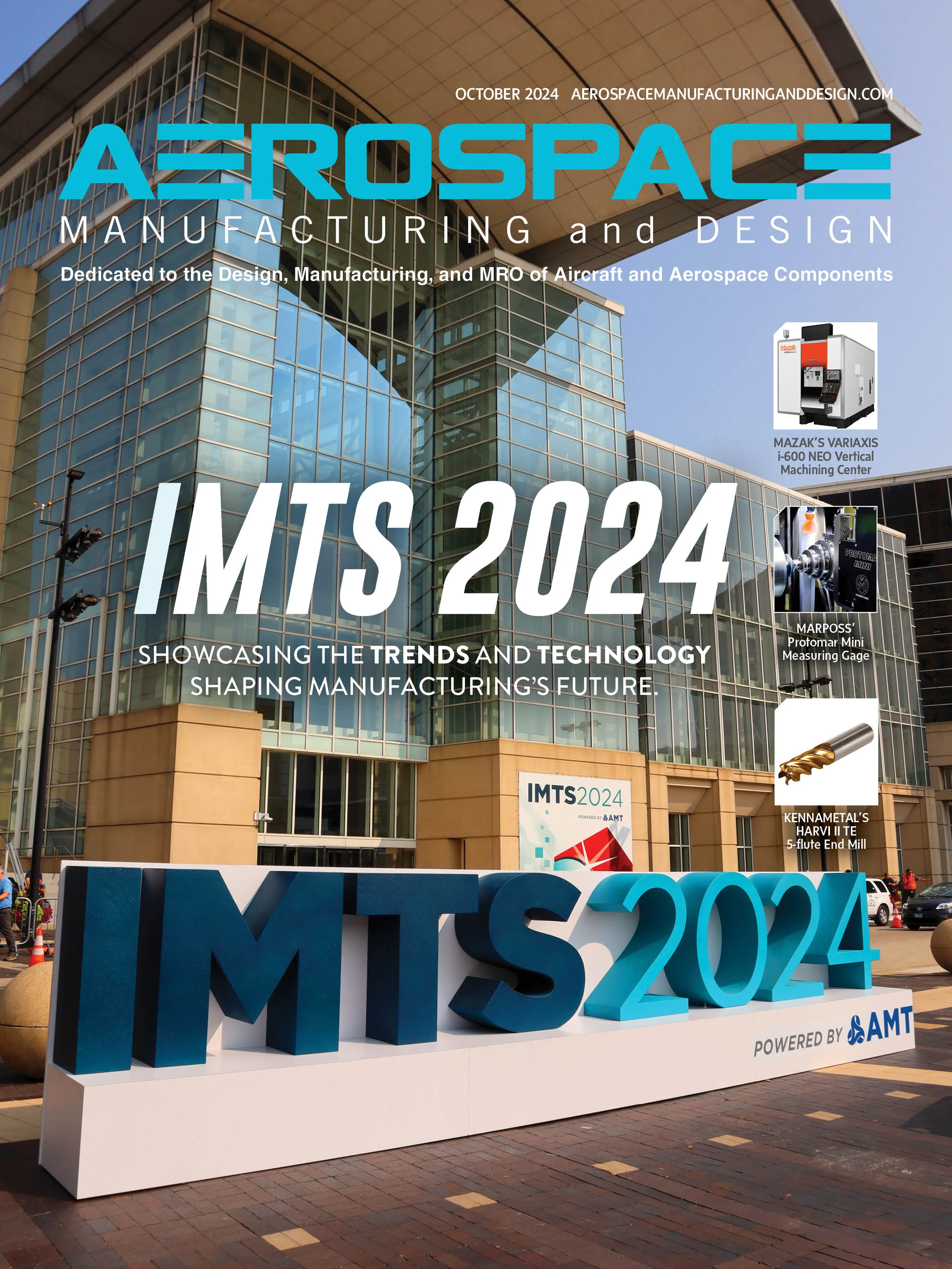
Explore the October 2024 Issue
Check out more from this issue and find your next story to read.
Latest from Aerospace Manufacturing and Design
- Talking machine tools with the professionals who build them
- Tools and strategies for improving your machining processes
- America Makes announces QTIME project call
- Innovation meets precision for 40% faster machining
- Upcoming webinar: Pro tips from a supply chain strategist
- Heart Aerospace relocates to Los Angeles
- Fixtureworks introduces Stablelock Clamps
- Piasecki acquires Kaman's KARGO UAV program