

Is sticking a superabrasive grinding wheel still necessary given the advancements in modern CNC grinding technology?
Let’s begin by defining sticking. Dressing sticks, also called abrasive stones, are typically made from silicon carbide (green) or aluminum oxide (white). The sticks are usually about 6" long. One purpose of sticking (applying a dressing stick) is to remove debris from a grinding wheel’s cutting surface. When a grinding wheel becomes loaded, its ability to remove material from the workpiece decreases. Instead of cutting, it gradually begins to push the workpiece away.
A secondary purpose of sticking is to break down the grinding wheel’s bond, allowing the worn crystals to fall out to reveal fresh, sharp ones.
Traditionally, wheel sticking in CNC grinding has been a manual process performed at predetermined intervals or triggered when the workpiece dimensions begin to fall outside tolerance. A decline in surface finish can also prompt sticking. Occasionally, the workpiece (particularly steel) may start to discolor, signaling the wheel has glazed over and requires sticking.
The operator stops the machine and manually applies a dressing stick to the wheel at reduced revolutions per minute. This carries a safety risk, as the operator’s hands need to reach into a machine with a rotating spindle. However, some safety protocols prevent the spindle from operating while the machine doors are open.
To mitigate safety concerns associated with manual wheel sticking, most machine manufacturers have incorporated automatic sticking devices. The grinding wheel automatically moves to a stick in a holder and makes several passes over the tip of the stick. Operators can track data on how much the dressing stick wears and whether the grinding wheel loses diameter. These parameters are then integrated into the programming, ensuring a reliable and repeatable process. Longer periods of unattended production become possible.
Another approach is using a rotary onboard dresser. Similar to sticking, rotary dressing restores the grinding wheel’s cutting ability.
An automatic onboard dresser generally performs the renewal process more effectively than a fixed stick. By using the entire circumference of the dressing wheel, the process becomes more predictable and consistent. Like dressing sticks, dressing wheels are also made from silicon carbide or aluminum oxide.
To improve the process, an acoustic gap control system is often used, allowing the grinding wheel to automatically approach the dressing wheel and accurately determine the current diameters of the grinding and dressing wheels.
The selection of sticks, dressing wheels, and operational parameters is provided by the wheel manufacturers and should be followed as closely as possible.
The answer to whether wheel sticking is still necessary with today’s technology is yes, although it’s required less frequently than in the past. I highly recommend this process be included in your continuous improvement program.
MyGrinding Inc.
https://www.mygrinding.com
Get curated news on YOUR industry.
Enter your email to receive our newsletters.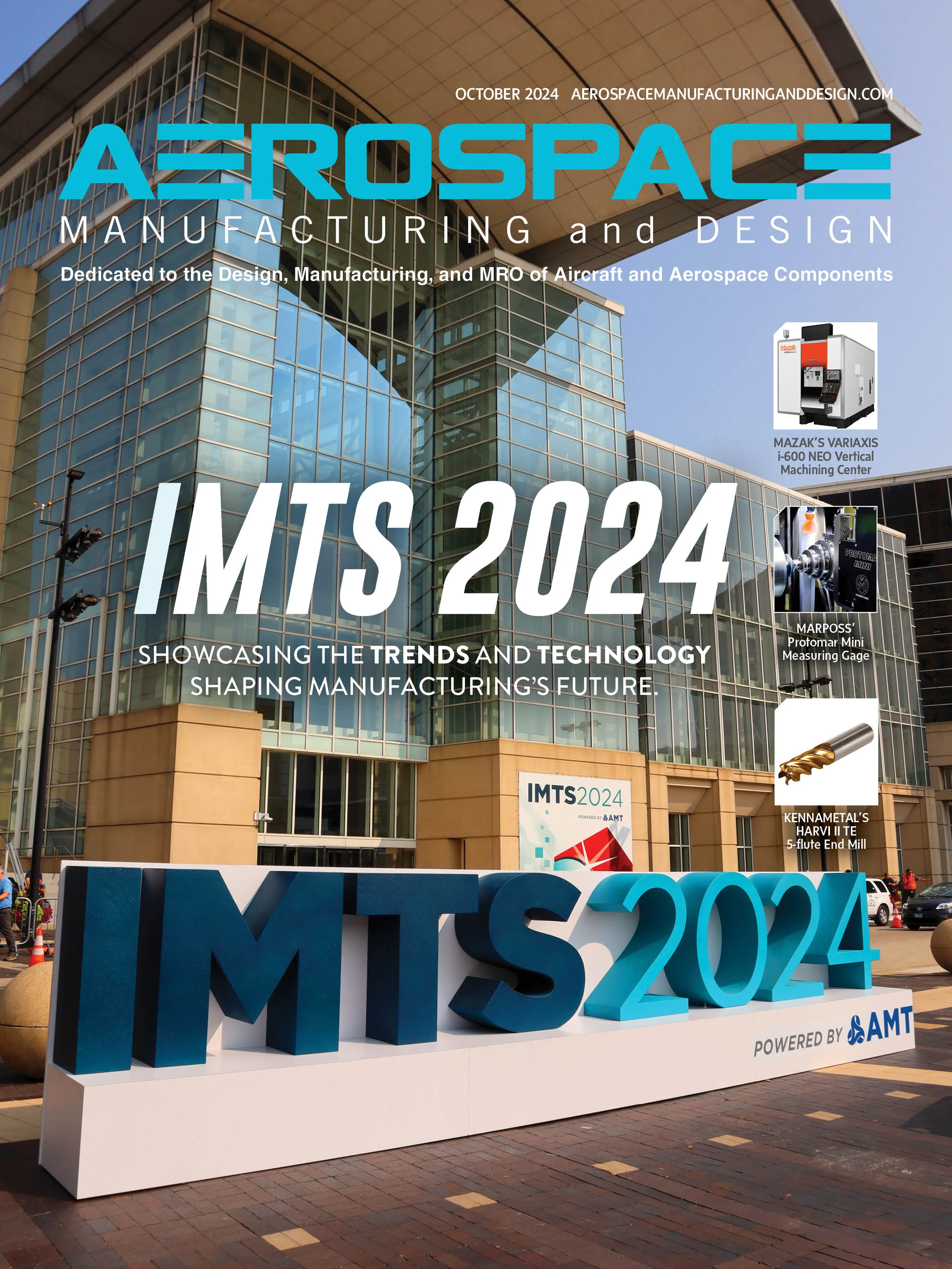
Explore the October 2024 Issue
Check out more from this issue and find your next story to read.
Latest from Aerospace Manufacturing and Design
- NASA offers free high school engineering program this summer
- Pemamak's PEMA Vision 3D software
- Aerospace Industry Outlook - Spring 2025, presented by Richard Aboulafia
- Panama’s National Air and Naval Service selects Embraer Super Tucano
- Model 5770 Linear Abraser
- #42 Lunch + Learn Podcast - Quell Corp
- RECARO Aircraft Seating showcases advanced comfort solutions at AIX 2025
- Mitutoyo America’s MiSTAR 575 Shop Floor CNC CMM