
Uncrewed military systems represent a significant trend in modern warfare. From drones used for airstrikes and high-altitude surveillance to autonomous ground vehicles used for bomb disposal and reconnaissance, these uncrewed platforms offer mission flexibility and effectiveness while keeping forces personnel away from harm.
Demand for such platforms is growing rapidly worldwide. According to recent research from Prudent Markets, the uncrewed aerial vehicles sector is projected to reach $17 billion by 2028, with a compound annual growth rate of 5.7%. This upward trend is also repeated in the market for military uncrewed ground vehicles, with a study by Mondor Intelligence valuing it at $1.73 billion in 2024 and growing to $2.68 billion by 2029. In both cases, as with other uncrewed platforms such as autonomous underwater vehicles, this rapidly increasing demand is driven by multiple factors, including a desire to enhance military situational awareness and strike capabilities while reducing human casualties and costs.
A wide variety of energy sources
As the number of uncrewed platforms increases, so do the types of onboard energy sources. Larger drones, for example, are typically powered by combustion engines of different types, with some using indirect drive with generators producing electricity to drive electric motors. Combustion engines provide extended flight times and have good specific fuel consumption but are often heavier than other power sources and can be more complex to maintain.
Electrical systems are increasingly being favored for uncrewed military platforms, especially in short-range or light payload tasks, as they tend to be more reliable while emitting no greenhouse gasses at the point of use. Therefore, batteries are coming to the fore, with varying chemistries, including lead acid, nickel-cadmium, nickel metal hydride, alkaline, lithium polymer, and lithium-ion, to name a few.
In battery-powered military drones, the rechargeable batteries supply DC power directly to the motors. DC-DC converters play a vital role in regulating voltages levels across uncrewed military vehicles for systems such as the motor speed controller, flight/drive controls, and communication modules, as well as auxiliary systems onboard, including sensors and payloads. Converters are essential links in the chain of the performance of uncrewed aerial vehicles, with their performance directly influencing all areas of the vehicle’s operation.
Power management considerations
The specific requirements of each propulsion system for uncrewed military systems will affect the design and implementation of power conversion systems, comprising DC-DC for battery systems and AC/DC for generators driven by a diesel or jet engine. Because of the uncrewed characteristics, some common power challenges must be addressed across land, sea, air, and ground platforms. These challenges require engineers to be innovative and resourceful when designing power solutions.
First, uncrewed platforms tend to be smaller than their crewed counterparts, as lacking a human occupant eliminates the need for associated life-support systems. The smaller size also allows for increased stealth, mobility, and agility. However, this creates space limitations, compounded by the need for additional onboard systems, such as sensors and communication equipment. So power management solutions must be as small and light as possible, which requires careful consideration at the design stage.

Uncrewed platforms may require power for propulsion, communication systems, and sensor operation, and this requirement makes managing and distributing power efficiently while ensuring reliability and safety hard to achieve. They also often need higher levels of autonomy and redundancy in power systems to guarantee continued operation in remote or hostile environments, adding complexity to the power management architecture. Noise profile is also important – including electronic noise that can disturb radio, sensors, and more. And military platforms must be able to operate in harsh environments, with wildly varying temperatures, high vibration levels, dust, and electromagnetic interference often the norm. Ultimately, power management systems must be elegant yet rugged and resilient to meet these requirements while maintaining optimal performance.
The importance of global standards
Power management, including DC-DC and AC/DC power conversion, can be more demanding on uncrewed military platforms compared to conventional, crewed platforms. So, how are power management specialists meeting these challenges through more innovative design of critical systems and components?
In the 4W to 500W power range, DC-DC converters are crucial in efficient power management for systems, such as communication platforms; sensor networks; and avionics, flight, and environmental controls. Global standards provide guardrails for designing and manufacturing DC-DC converters for uncrewed military platforms, with multiple standards and stringent requirements in input voltage, electromagnetic interference, environmental conditions, and thermal management.

Many programs are covered by standards that overlap with crewed vehicles, such as MIL-STD (Military Standard). These MIL-STD standards have been created to ensure products used in military applications meet rigorous standards for reliability, performance, and interoperability. Examples include MIL-STD-810: environmental testing for harsh environments with temperature extremes, shock, vibration, and humidity; MIL-STD-461: providing requirements for electromagnetic compatibility; and MIL-STD-1275: requirements for input power.
Other standards specific to civilian aircraft and uncrewed aerial vehicles, meanwhile, include RTCA DO-160G, with section seven specifically focusing on operational shocks and crash safety; and SAE ARP4754A covering guidelines for airborne electronic hardware design including materials and environmental considerations.
Standards might be set by individual military branches or agencies, such as STANAGs (NATO Standardization Agreements) or specific program-level requirements. Ultimately, the component supplier must conduct case-by-case research for the particular standards and requirements for uncrewed platforms, with direct contact with the national program office or prime contractor responsible for detailed information about the exact requirements and stage-gating of the approval process.
Innovation in DC-DC and AC/DC converters
Fortunately, companies such as Gaia Converter have many years of experience in designing and building high-reliability DC-DC and AC/DC converters and power systems developed specifically to satisfy military and aerospace applications, considering factors such as size, power, temperature, weight, cost, compliance, scalability, and modularity. These products meet the diverse requirements of military applications for input buses, EMI/RFI compatibility, and severe environments with extended operating temperatures from -40°C to 105°C (-55°C optional). By extension, many of these rugged and reliable components will be suitable for uncrewed applications, depending on the program’s specific requirements. These products include:
- The MGDM-500 series features a range of 500W military grade isolated DC-DC converters with a wide input voltage range and a wide choice of output voltage from 12VDC to 48VDC – meeting demanding military applications where MIL-STD-461/704/1275 and DO-160 compliance is required. The MGDM-500 has one of the highest power densities in the market and has outstanding conducted noise performances based on double interleaved forward topology. It has protections such as soft start for inrush current limitation, overload and short circuit protection, and over-temperature shutdown.
- The LGDS-600 DC-DC input bus conditioner is designated as a range of 600W military-grade front ends that enable and ease the construction of power architectures. It provides highly effective transient suppression for sudden voltage spikes, with a powerful voltage limiter for long lasting surges up to 100VDC and 200VDC. The LGDS-600 series has control functions for power backup, a bi-phase switching frequency generator to synchronize downstream converters, and ultra-low series losses. Consequently, the LGDS-600 requires only input EMI filtering to fully comply with most international input bus standards, such as MIL-STD-704, MIL-STD-1275, and AECMA EN2282.
- Other products suitable for military applications include the MGDD21 - DC-DC and AC/DC Converter 20W power; LHUG150 - DC-DC Input Bus Conditioner 150 W power.
GAIA also has in-depth internal expertise that can provide system developers with how to design complex, high-power DC-DC converter architectures for military-grade power systems. A modular approach can significantly simplify the design process, enabling engineers to create complex power conversion systems using commercial off the shelf (COTS) and size, weight, and power (SWaP)-optimized building blocks. Engineers can meet multiple industry standards and power requirements while optimizing their power architectures according to new industry standards such as the Sensor Open System Architecture (SOSA). This expertise has led to developing a new fully integrated DC-DC front-end module that simplifies the design of military power converter architectures. The FLHG-60-ON modules comply with the most restrictive military and avionics standards, including MIL-STD 461/704/1275 and DO160, when used with GAIA DC-DC converters. The FLHG60 has no equivalent on the market and represents the company’s intense research and development effort to reach full compliance.

Finding the answers
As global interest in uncrewed military systems grows, the demand for reliable power solutions becomes increasingly critical. However, military environments demand DC-DC power modules to meet exacting requirements in a broad range of areas related to size, power, temperature, weight, cost, and compliance. GAIA Converter offers the know-how and the breadth of its product portfolio to design and build DC-DC converters for any application, helping platform leads to enhance scalability, modularity, and faster speed-to-market on the uncrewed platforms of the future.
GAIA Converter
https://www.gaia-converter.com
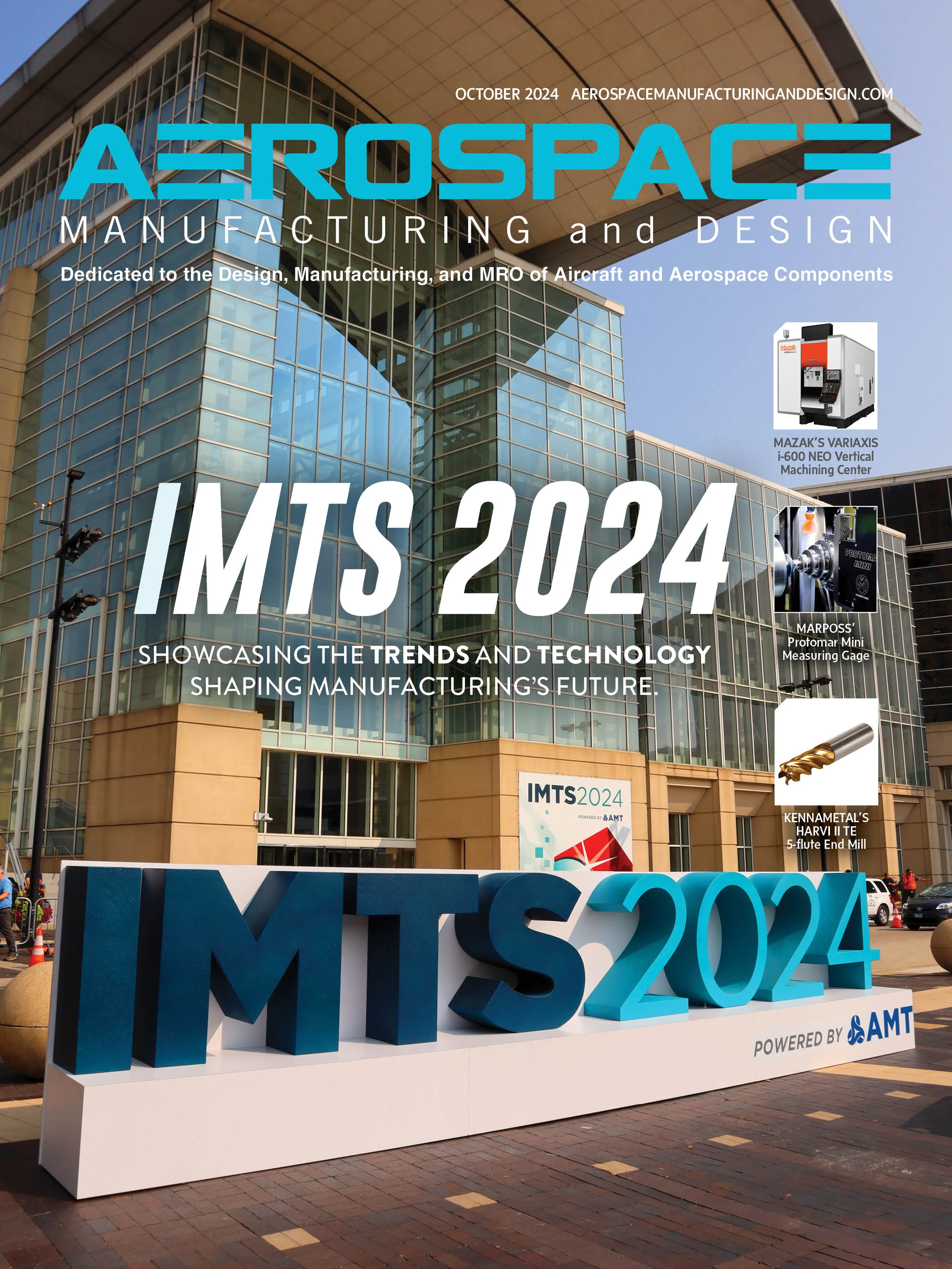
Explore the October 2024 Issue
Check out more from this issue and find your next story to read.
Latest from Aerospace Manufacturing and Design
- AAMI project call submission deadline extended to May 12
- Jergens launches cast iron tooling column additions
- Airbus to acquire assets relating to its aircraft production from Spirit AeroSystems
- FANUC America's Cobot and Go web tool
- Chicago Innovation Days 2025: Shaping the future of manufacturing
- High-density DC/DC converters for mission-critical applications
- #59 - Manufacturing Matters: Additive manufacturing trends, innovations
- ACE at 150: A legacy of innovation and industry leadership