

1. What type of furnace do I need?
Atmosphere or air furnaces work well for bar, sheet, or plate materials that will have stock removed afterward. Finished machined components and additive manufactured builds should be done in a vacuum furnace. When choosing a furnace, you must know if the furnace can hold the proper temperature tolerance throughout the run. If parts need to comply with industry and aerospace specifications, the furnace must demonstrate it can maintain ±10°F in the furnace work zone envelope.
2. Can I combine varied sizes and thicknesses in the same run?
There’s no need to run two loads if all can be done in one. AMS2759/3, Table 4 will give you an idea of thickness overlaps. A well-spaced load, not densely packed, will always achieve the best results. I’ve personally heard of bars being aged in their received bundles, which predictably causes a wide range of hardness variations. This is a clear sign of over and under-aging conditions, with the inside not getting hot enough and the outside exposed to heat for too long.
3. Everything went well with the aging cycle, but the hardness levels are nonconforming.
We operate at risk when we only complete the age harden of PH alloys. We must assume the upstream solution treatment (typically done at the mill) was performed accurately. This includes making sure the PH grade is cooled to below a specific temperature before the age harden.
I assume the furnace was loaded (not densely packed), calibrated, surveyed, and thermocoupled correctly. When diagnosing a problem like this, you must take a piece, solution treat, and age it. If the hardness falls within the specified requirement, improper solution treatment was the root cause.
4. My customer is asking for H900, which develops a 40-47 HRC. However, my customer wants 40-43 maximum HRC.
We’ve seen these types of requests for HRC ranges that have only one or two points. In many cases, you must explain what’s feasible. PH Stainless grades usually have wider hardness ranges because there’s variability in chemistry and/or the response to the age harden. Plus, many specifications don’t allow you to deviate on the initial age harden cycle. H900 requires 900 ±10°F for 1 hour +15 minutes -0 minutes. That’s it. That’s where you must start. From our experience, this cycle typically develops a 44-46 HRC, so now you’re anywhere from 1HRC to 2HRC over the maximum.
If hardness exceeds the maximum specified, you can re-age at the same temperature (recommended) or even go 10°F higher to reduce the hardness by a point or two. But re-aging may cause the hardness to fall below 40HRC, resulting in a re-solution anneal and starting all over again.
5. Will my finished parts distort? Is there any concern about size change or distortion in raw bar stock?
People use PH grades because they believe they don’t move dimensionally. Not true. They distort minimally when compared to other quench and tempered alloys. Major steel mills have literature with predictable size contraction based on the age harden or H COND. Distortion, however, is very unpredictable, especially for parts made from hardened bars. In these situations, AMS2759/11 also discusses stress relieving of PH alloys 100°F below the final age temperature. I’ve seen this minimize distortion and heard of less movement of the parts, especially in elevated temperature applications.

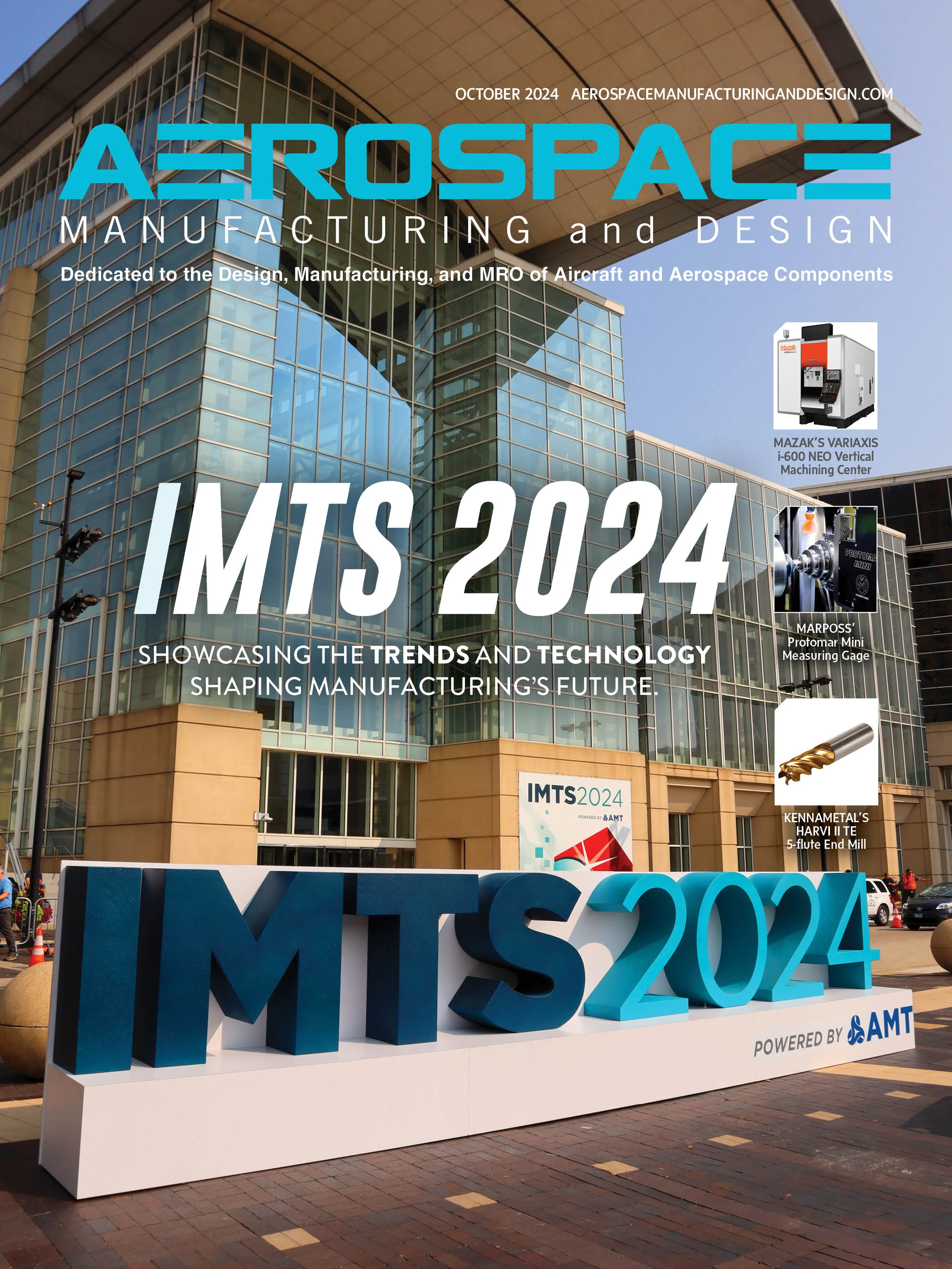
Explore the October 2024 Issue
Check out more from this issue and find your next story to read.
Latest from Aerospace Manufacturing and Design
- Taiwan’s China Airlines orders Boeing 777X passenger, freighter jets
- Reamer re-tipping extends life of legacy tooling
- Revitalizing the Defense Maritime Industrial Base with Blue Forge Alliance
- Safran Defense & Space opens US defense HQ
- Two miniature absolute encoders join US Digital’s lineup
- Lockheed Martin completes Orion for Artemis II
- Cylinder CMMs for complex symmetrical workpieces
- University of Oklahoma research fuels UAS development