
ShopFloorConnect OEE, production tracking, and data collection software allows users to quickly leverage data from their machines. The on-premises software solution provides timely, accurate, and unbiased data directly from the shopfloor for making informed management decisions.
The software is scalable and well-suited for manufacturers in metalforming and metal fabrication, machining, injection molding, and more. The software provides valuable overall equipment effectiveness (OEE) calculations that accurately report OEE for complex manufacturing environments, and unlike cloud data solutions, customers fully own their data.
ShopFloorConnect is available in three customizable purchase packages, depending on customer requirements for features, capabilities, and number of users.
Wintriss Controls Group
https://www.wintriss.com/sfc
TEMPUS technology reduces AM build times up to 50%

Patented TEMPUS technology enables users of RenAM 500 series metal additive manufacturing (AM) systems to reduce build times up to 50%. The technology uses advanced scanning algorithms that sequence the layer data to maximize productivity while maintaining part quality. The optimization suits some part geometries more than others, but all geometries will have some productivity benefits. Parts with thin, vertical features are likely to experience proportionally higher productivity savings.
TEMPUS technology is standard with the RenAM 500 Ultra system, along with advanced process monitoring software. Existing RenAM 500 series customers can access TEMPUS technology as a paid-for upgrade.
While traditional powder bed systems require the powder recoater to fully distribute powder before the layer can be consolidated, TEMPUS technology fires the lasers as the recoater is moving, saving up to nine seconds of build time from every layer with no reduction in part quality.
Renishaw
https://www.renishaw.com
Grade for machining Inconel 718, stainless steels

Grade HB-710 is for extended cutting edge wear in machining high temperature, nickel-based alloy and stainless-steel materials. Developed to increase performance in milling and drilling difficult-to-machine applications, the new grade balances toughness and hardness to achieve high degrees of edge line security and resistance to corner and micro chipping, two common modes of tool failure in these applications.
The submicron grain size and medium-low cobalt content of HB-710 are well suited for grinding to produce the desired cutting-edge geometries.
The company manufactures tungsten carbide custom, standard, and altered blanks and preforms in a comprehensive selection of grades. Vertically integrated, it manages the entire process from powder production through the delivery of high-performance, reliable near-net shaped blanks that address specialized customer application challenges across diverse industries.
H.B. Carbide
https://hbcarbide.com
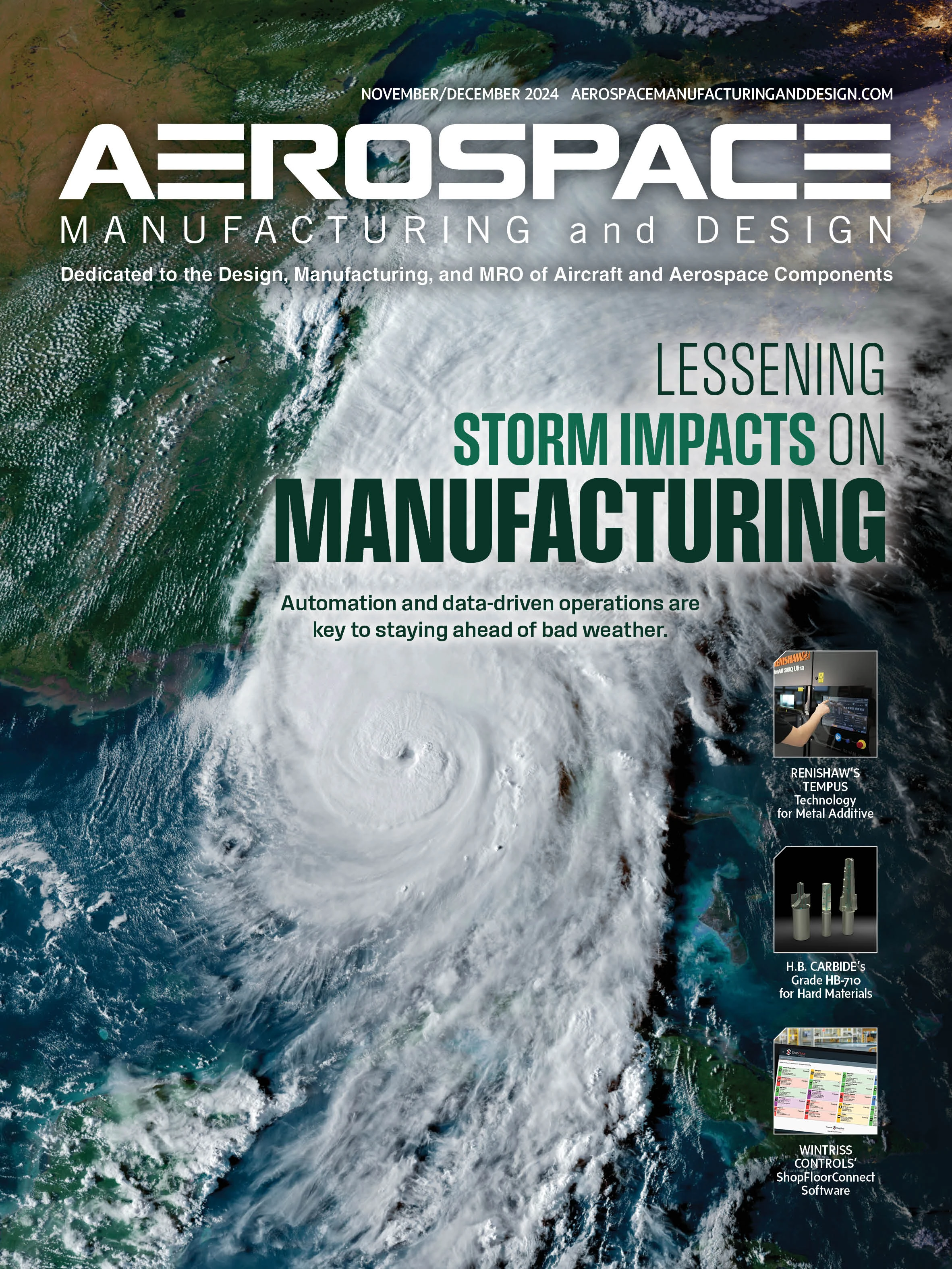
Explore the November/December 2024 Issue
Check out more from this issue and find your next story to read.
Latest from Aerospace Manufacturing and Design
- America Makes announces QTIME project call
- Innovation meets precision for 40% faster machining
- Upcoming webinar: Pro tips from a supply chain strategist
- Heart Aerospace relocates to Los Angeles
- Fixtureworks introduces Stablelock Clamps
- Piasecki acquires Kaman's KARGO UAV program
- PI Americas’ long-travel XY piezo nanopositioners-scanners
- AAMI project call submission deadline extended to May 12