
According to a recent State of Smart Manufacturing Report of more than 1,500 manufacturers, supply chain disruption was cited as one of the top five biggest external obstacles to manufacturers’ growth in 2024. Extreme weather events are having increasingly harmful impacts on manufacturers, causing more disruptions as these events become more frequent and severe. In fact, the National Centers for Environmental Information reported 19 weather events with losses exceeding more than $1 billion each in the first 7 months of 2024. Manufacturing networks also face heightened risks as they grow more interconnected. Hurricanes, power outages, and floods can impact the availability of raw materials or cause damage to facilities. Meanwhile, severe storms in any season can heighten these risks, throwing a curveball for supply chains by delaying deliveries and disrupting production schedules.
Weather patterns
Understanding El Niño and La Niña weather conditions is essential for manufacturers as these patterns significantly influence global weather, which in turn affects operations. El Niño is characterized by the warming of sea surface temperatures in the central and eastern Pacific Ocean, leading to wetter conditions in some regions while causing drought in others. La Niña brings cooler sea surface temperatures and often results in the opposite weather effects, such as increased hurricane activity in the Atlantic. According to the National Weather Service, El Niño conditions existed through summer 2024, while La Niña conditions were expected to start afterward and are likely to persist through the first quarter of 2025. Both climate patterns have profound implications for manufacturing, especially in areas prone to extreme weather, making it critical for manufacturers to anticipate and prepare for the potential impacts during these cycles.
Building resilience
While forecasting the weather is still possible, the intensifying nature and frequency of extreme storms makes planning for them more difficult. Experts can easily plan for cold weather in the winter, but anticipating specific incidents resulting from that weather can be tough. For example, the February 2021 ice storm in Texas crippled the state’s power grid, leading to widespread blackouts and production halts. This triggered a global plastics shortage, doubling the prices of raw materials as demand increased. The Texas storm had a domino effect, disrupting local and global supply chains.
Manufacturers need to adopt a comprehensive, data-driven strategy to build resilience against a variety of weather-related risks. For regions vulnerable to extreme heat and wildfires, implementing temperature-controlled environments and fire-suppression systems is vital. In areas prone to floods, ice, or snowstorms, manufacturers should focus on ensuring proper drainage, reinforcing structural integrity, and monitoring weather conditions in real time to adjust production schedules as necessary. For regions prone to tornadoes and hurricanes, manufacturers should reinforce facilities, secure supply chains by diversifying suppliers, and stockpile critical materials. Manufacturers can also prepare for power outages by installing generators and implementing automated systems that allow for real-time adjustments to production and logistics.
Be prepared
Protecting factories and logistics requires tailored strategies. Preparing the operations site or factory involves conducting regular risk assessments, updating contingency plans, automating critical processes to ensure operational continuity, and enhancing communication channels to keep all stakeholders informed and ready to respond to any delays or challenges.
For logistics, it’s essential to leverage real-time data and analytics to reroute shipments around affected areas. Maintaining strong relationships with multiple suppliers ensures alternatives are available during disruptions. Implementing cloud-based logistics management systems can provide enhanced visibility and flexibility, safeguarding the supply chain against weather-related interruptions.

Have a weather action plan
A comprehensive weather action plan is crucial for safeguarding manufacturing operations and employee safety during extreme weather events. This type of plan should include adjusting work schedules based on real-time weather data and forecasts.
Employee safety should be a top priority, with clear protocols such as evacuation plans and, where possible, options for remote work.
Maintaining optimal stock levels through predictive analytics ensures production can continue even when supply chains are disrupted.
Additionally, protecting critical data is vital. Ensuring all important information is backed up offsite or in the cloud helps safeguard against data loss during power outages or other disruptions.

Leveraging forecasts, big data analytics
Long-range weather forecasts are valuable tools for manufacturers, providing crucial insights for planning and preparedness. Traditional sources such as the Farmers’ Almanac offer broad predictions, valuable for their historical perspective. In contrast, commercial forecasting services deliver detailed, localized data essential for more precise planning.
The most effective strategy combines these forecasts with real-time data analytics, allowing manufacturers to quickly adjust their plans and make informed decisions as conditions evolve. This approach ensures short-term responsiveness and long-term strategic planning, helping manufacturers stay ahead of potential disruptions and maintain operational resilience.
Manufacturers must leverage big data analytics as a crucial digital building block in business processes. Historically, manufacturing operations and data management consisted of spreadsheets, planner experience, and a lot of guesswork. Decisions were made based on dated, error-prone information and human analysis using spreadsheets or old disparate software and systems. This reality forced companies to be reactive – data compiled and analyzed after events left manufacturers responding to weather that already occurred.
Achieving real-time visibility is critical to monitor safety stock and actual lead times to ensure material availability for production schedules to stay on track. Data is the key to helping manufacturers navigate unpredictable changes, make informed decisions, respond to issues, and adjust accordingly in real time. Failure to prioritize this can trigger a domino effect, disrupting production schedules and ultimately impacting the bottom line.

Real-time weather data is essential for making immediate operational adjustments, while supply chain analytics provide insights into potential disruptions, allowing for proactive management. Predictive maintenance data is critical for preventing equipment failures during adverse conditions, ensuring production continues smoothly. Additionally, historical weather data can inform long-term planning and risk assessments, helping manufacturers anticipate and prepare for recurring patterns and trends. By integrating these data sources into operations, manufacturers can enhance their ability to respond to expected and unexpected weather events.
Manufacturers can take the following key steps to embrace data in their operations and decision making:
- Assess digital maturity: As digital leaders progress on the maturity path, digital laggards will be forced to adapt or drop out. Manufacturers must evaluate current data infrastructure, analytics capabilities, and integration with critical systems to identify areas for improvement.
- Shift to a data-driven cultural mindset: Data-driven manufacturing and decision making means adopting a collaborative approach to decision making guided by data insights, ensuring operational visibility and agility.
- Leverage automation and integration: Use process automation and smart manufacturing systems to optimize operations, improve decision making, and enable real-time insights across the organization.
How automation can help
Siloed, error-prone, and outdated manual and paper-based processes can no longer keep pace with the complex and unpredictable landscape of modern manufacturing. By leveraging automation and smart manufacturing software, companies can optimize operations, improve decision making, and enhance overall performance. Automating production adjustments based on real-time weather data can minimize disruptions and maintain continuity. Smart manufacturing systems integrate data across the organization, enabling a comprehensive view of operations. Predictive analytics further support proactive measures, such as adjusting schedules or rerouting shipments before a storm hits. Embracing these technologies equips manufacturers with the agility and resilience needed to navigate unpredictable conditions.
Plex by Rockwell Automation
https://www.plex.com
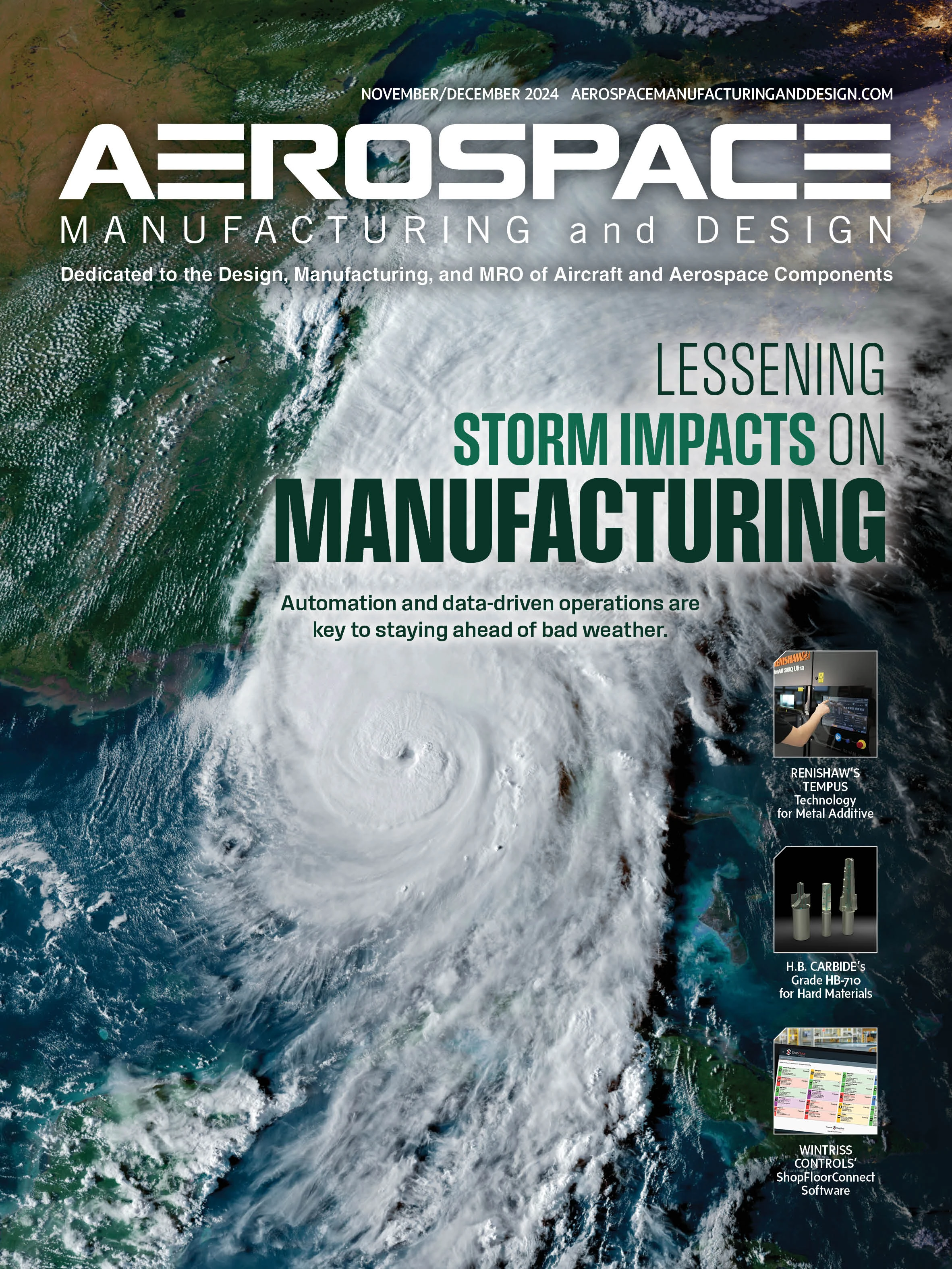
Explore the November/December 2024 Issue
Check out more from this issue and find your next story to read.
Latest from Aerospace Manufacturing and Design
- NASA selects instruments for Artemis lunar terrain vehicle
- Twin-cutter boring head
- Bell awarded funding for X-plane build phase of SPRINT program
- Shaft coupling clamps
- #46 Lunch + Learn Podcast with SMW Autoblok
- Gleason Corp. acquires the Intra Group of Companies
- Thread milling cutter reduces cutting pressure, vibration
- Malaysia Aviation Group orders 20 more Airbus A330neo widebodies