
Stereolithography (SLA) 3D printer manufacturer Formlabs released the large-format Form 4L with a 353mm x 196mm x 350mm build volume, nearly 5x the size of its predecessor, the Form 4. The Form 4L can produce large-scale prints in less than six hours, as well as thousands of small parts per day, with speeds up to 80mm/hour. Built on Formlabs’ proprietary Low Force Display (LFD) print engine, the printer offers a 99% print success rate compared to other SLA 3D printers.
The Form 4L is compatible with more than 23 Formlabs resins with properties such as durability, rigidity, and flame retardancy. The printer can also be used in Open Material Mode, allowing users to choose their own materials. A new cartridge design reduces plastic waste by 63% and delivers faster resin dispensing. The new release is also available as a biocompatible version called the Form 4BL.
Formlabs
https://formlabs.com
Specialty materials for industrial additive manufacturing

Renishaw has launched five new materials for use with its RenAM 500 series of metal industrial 3D printers. The materials include commercially pure copper, H13 tool steel, Hastelloy X alloy, super-duplex stainless steel, and AlSi7Mg aluminum alloy. The company worked directly with customers to develop process parameters for new alloys for its laser powder bed fusion (LPBF) additive manufacturing (AM) systems.
The material release opens up several new applications. Pure copper has extremely high thermal and electrical conductivity, making it well-suited for consumer electronics and heat exchanger components. The strong, lightweight aluminum AlSi7Mg can be used in multiple aerospace and automotive applications, while H13’s thermal fatigue properties and high heat resistance make it suitable for a variety of high-temperature uses. Hastelloy X alloy and super-duplex stainless steel are both strong and corrosion resistant, making them highly applicable to the oil and gas and chemical process industries.
Renishaw
https://www.renishaw.com
Lightweight 3D-printed alloy

Researchers at Oak Ridge National Laboratory (ORNL) and the National Energy Technology Laboratory (NETL) developed and 3D printed the lightest crack-free alloy capable of operating without melting at temperatures above 2,400°F. The development has the potential to allow additively manufactured (AM) turbine blades to more effectively handle extreme temperatures, such as those generated in the gas turbine engines used in airplanes. While materials such as tungsten can handle these temperatures, they’re too heavy to use in airplanes. The ultra-light weight of the new alloy could reduce the carbon footprint of aircraft.
A few years ago, ORNL researchers developed a new class of extreme heat-resistant nickel- and cobalt-based superalloys for use in metal 3D printing applications. The latest material, however, composed of seven different elements combined in a niobium-rich, complex concentrated alloy, has a melting point at least 48% higher than those superalloys. The researchers 3D-printed test components with the new material by fine-tuning their electron beam melting process.
National Energy Technology Laboratory
https://netl.doe.gov
Oak Ridge National Laboratory
https://www.ornl.gov
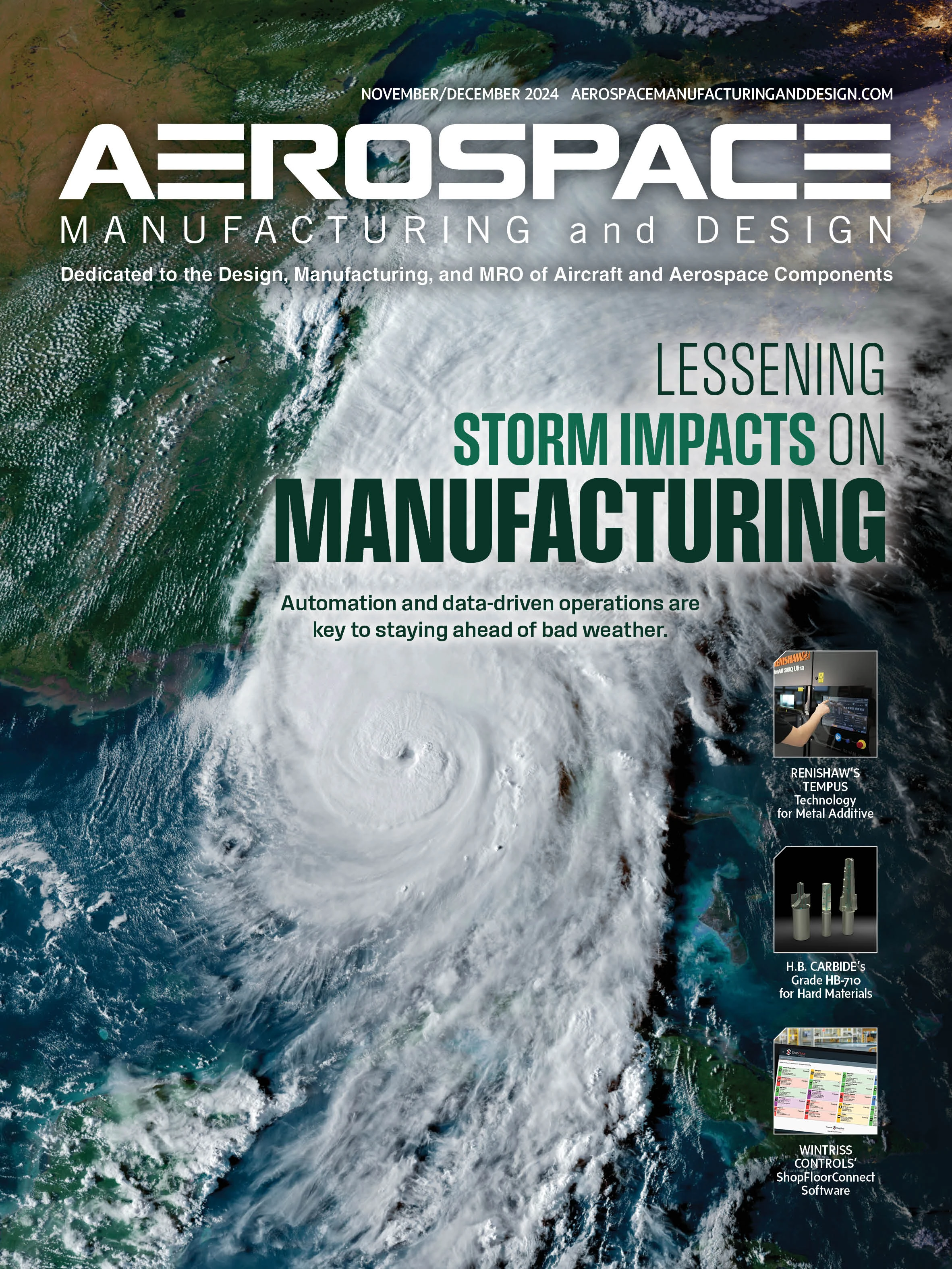
Explore the November/December 2024 Issue
Check out more from this issue and find your next story to read.
Latest from Aerospace Manufacturing and Design
- AAMI project call submission deadline extended to May 12
- Jergens launches cast iron tooling column additions
- Airbus to acquire assets relating to its aircraft production from Spirit AeroSystems
- FANUC America's Cobot and Go web tool
- Chicago Innovation Days 2025: Shaping the future of manufacturing
- High-density DC/DC converters for mission-critical applications
- #59 - Manufacturing Matters: Additive manufacturing trends, innovations
- ACE at 150: A legacy of innovation and industry leadership