
JuggerBot 3D LLC, an industrial 3D printer original equipment manufacturer (OEM), announced the selection of key technical partners for a hybrid additive manufacturing (AM) project through the Air Force Research Laboratory (AFRL). Mississippi State University’s (MSU) Advanced Composites Institute (ACI) and Oak Ridge National Laboratory (ORNL) have been chosen as technical partners for their expertise in Fused Granulate Fabrication (FGF) and Direct Ink Writing (DIW) composite manufacturing.
The organizations will develop reliable process parameters for consistent material deposition, demonstrating the steps needed to produce production tooling for composite manufacturing.
This $4 million congressional award, funded by the Office of the Under Secretary of Defense for Research and Engineering Manufacturing Technology [OSD(R&E)], aims to advance large-scale hybrid AM to produce faster, less expensive tooling critical to the defense and aerospace industry. The project involves the development of a system integrating two-part resin and pellet-fed material extrusion technologies, processing performance-grade thermoplastic polymers and advanced thermoset resin inks, including epoxies and vinyl esters. The system is designed to reach build volumes of 360ft³. Phases of technology development will occur throughout the project, set to be completed in December 2025, from system development to comprehensive modeling and advanced tool path development.
ORNL, known for advancing innovative AM technologies, including FGF (pellet-fed 3D printing), has been selected to support advanced tool path generation software. This selection builds on previous Collaborative Research and Development Agreements (CRADAs) focused on sophisticated AM processing, such as JuggerBot 3D’s Bead Characterization System (BCS) and other competencies found in the JuggerBot 3D Material Card. ORNL and JuggerBot 3D will enhance slicing software and printer hardware to process thermosets independently and simultaneously with thermoplastics. JuggerBot 3D will also develop and integrate thermoset Material Cards.
MSU’s ACI will lead system-level validation. This process, which includes rigorous material testing and assessment (MT&A), ensures the effectiveness of the established process parameters for thermoset and thermoplastic materials.
Air Force Research Laboratory (AFRL)
JuggerBot 3D
Mississippi State University’s Advanced Composites Institute (ACI)
Oak Ridge National Laboratory (ORNL)
Build processor for investment casting

The Neo Build Processor for Investment Casting is designed to accelerate production of high-quality investment casting master patterns.
The build processor, developed for Stratasys Neo450 and Neo800 stereolithography (SLA) 3D printers, offers up to 50% faster file processing and enhanced print speeds, streamlining the 3D printing (3DP) workflow for manufacturers and service bureaus in the aerospace and other demanding industries.
3DP master patterns can reduce investment casting production time from weeks to days, resulting in up to 75% time savings compared to traditional methods of manufacturing, including wax mold and CNC machining. Rapidly producing intricate designs previously unachievable with conventional techniques opens new possibilities for innovation in part design and functionality, specifically with small-series production runs.
Combining Somos WaterShed AF resin, Neo SLA technology, and advanced Materialise software with the variable layer thickness feature produces highly accurate 3D-printed master patterns requiring minimal finishing. This streamlined process is designed to yield exceptional metal castings in record time.
MaterialiseStratasys
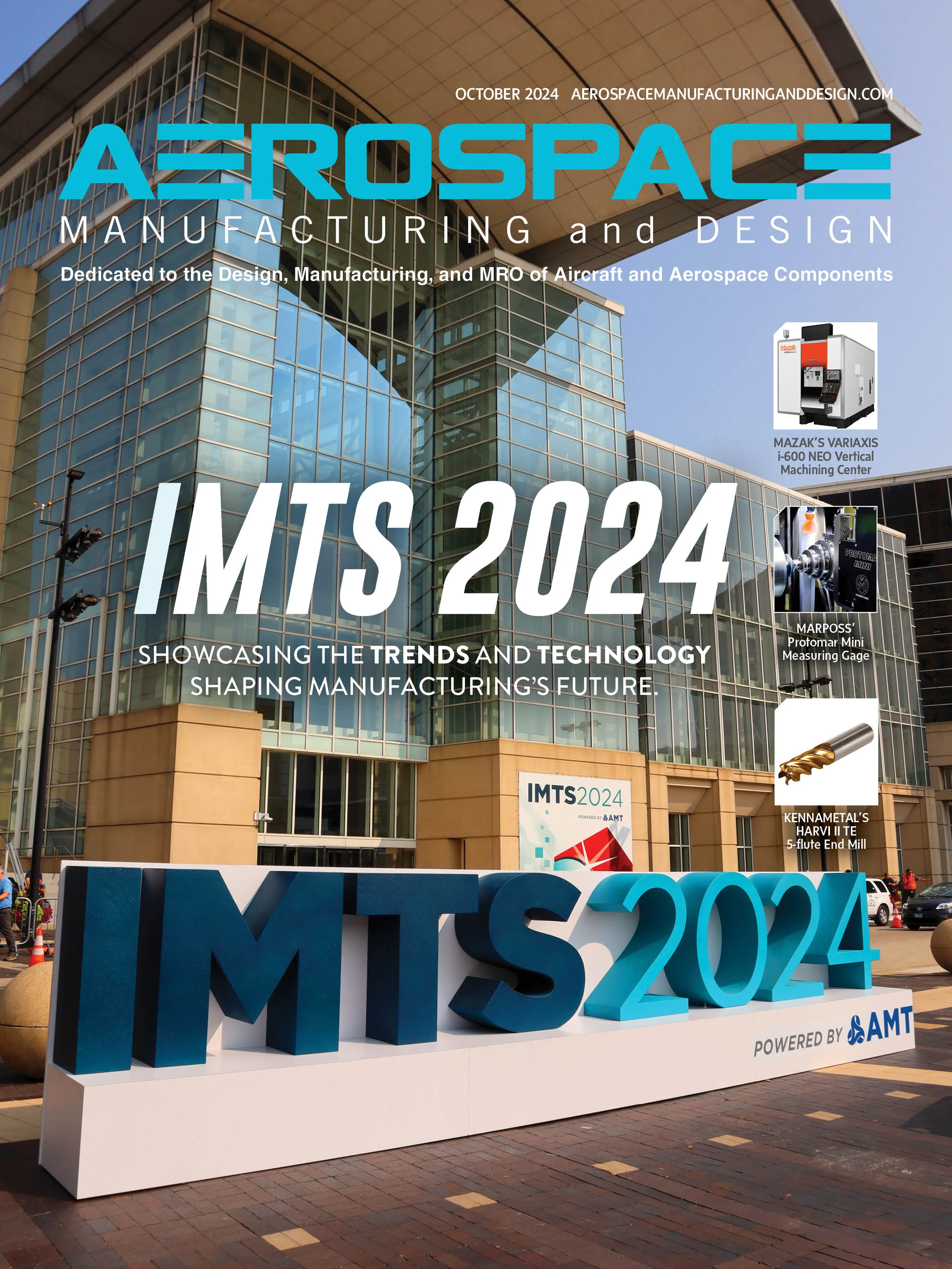
Explore the October 2024 Issue
Check out more from this issue and find your next story to read.
Latest from Aerospace Manufacturing and Design
- America Makes announces QTIME project call
- Innovation meets precision for 40% faster machining
- Upcoming webinar: Pro tips from a supply chain strategist
- Heart Aerospace relocates to Los Angeles
- Fixtureworks introduces Stablelock Clamps
- Piasecki acquires Kaman's KARGO UAV program
- PI Americas’ long-travel XY piezo nanopositioners-scanners
- AAMI project call submission deadline extended to May 12