
In this post-COVID world where airports are jammed with travelers flying for business or pleasure, demand for more commercial aircraft is testing the capacity of manufacturers and the supply chain.
A McKinsey report, “Planning for Uncertainty in Commercial Aerospace,” reveals aircraft manufacturers have a backlog of 9,400 passenger jets through 2027, spurring them to increase production to 55 to 100 aircraft a month for the next five years.
This is straining an already stressed supply chain still recovering from production delays and interruptions from the pandemic.
Additionally, inflation rates are keeping prices for aircraft and replacement parts sky high.
Supplementing the MRO supply chain
When a plane is grounded due to faulty parts, the headaches for operators become even more acute as they’re faced with the costly trifecta of maintenance, repair, and overhaul (MRO).
Not every operator has an MRO supply chain to cover every part of an aircraft. That’s where 3D printing (3DP) is filling the gap and providing a cost-effective, timely, and efficient solution to getting planes back in the air and making money.
While there are several examples of 3D-printed flight-critical parts, the technology’s greatest potential may be in replacing, even re-designing, parts not critical to flight. This is especially true for low- or no-criticality parts, such as cabin components, for which operators don’t generally maintain large inventories.
Ordering, paying for, and storing big backlogs of such parts makes little sense. But with 3DP, low volumes of spare parts can be delivered with much shorter lead times than those of conventional manufacturing methods.
The only other storage involved is for the digital files for those parts, which can then be retrieved when additional units need to be produced.

Expanding access to 3DP through partnerships
Just as the MRO industry is a three-headed entity, effectively serving its needs through 3DP requires alignment between manufacturing, design, and distribution.
Materialise recently formed a partnership with Proponent, the largest independent aerospace distributor, and Stirling Dynamics, an EASA 21.J-certified Aerospace Design Organization, which is part of Expleo.
Through this unique trifecta, each partner plays a role suited to its expertise.
- Stirling Dynamics develops improved, certified designs for 3D-printed interior cabin parts and provides complete aircraft documentation and installation instructions.
- Materialise 3D prints flight-ready parts in its EASA Part 21G-certified production facility.
- The parts are distributed by Proponent to airlines, MROs, and original equipment manufacturers (OEMs) globally.
Creative solutions made possible with 3DP
Here’s an example of how the combination of creative and thoughtful design and 3DP resolved a specific issue and created an opportunity for boosted revenue.
The problem revolved around a dado panel, or decompression panel, on a Boeing B737. In normal conditions, this grill mounted at the bottom of the cabin wall below the window stays partially open to allow air entering the cabin from the ceiling to exit through the side wall. If there’s a sudden change in pressure, such as decompression, the dado panel fully opens to speed up the pressure equalization between the cabin and the area affected by the decompression.
In the MRO process, a problem was identified in the number of latches and pins that allow the different parts to move. Those latches and pins tend to break easily, and when they do, the plane must be grounded until repairs can be made or a replacement panel can be produced and installed.
Replacement panels are expensive, and repairing the latches and pins would only amount to a stopgap until they break again.
Understanding the fundamental design flaw in the panel, Expleo worked with Materialise to redesign it with a more robust latching mechanism.

This resulted in cost savings for the airline by enabling it to replace entire dado panels with a redesigned panel lasting longer, reducing the amount of time a plane would need to be grounded if the panels required maintenance or replacement.
One more example of 3DP’s speed and flexibility involves a cover for a door handle that an airline didn’t like. With a unique design from Stirling Dynamics, the airline was able to incorporate its logo and use a glued attachment, rather than fasteners, eliminating the need to drill mounting holes in the internal side of the aircraft fuselage.
Creating efficiencies in original aerospace parts
If you’re playing defense all the time repairing or replacing parts, that’s not a sustainable game plan for reducing costs, delays, or time on the ground.
The design flexibility enabled by 3DP creates opportunities to produce better parts for OEMs as well. To avoid problems upfront, parts can be tested and endorsed by OEMs and then marketed to others once approved for flight to create an additional revenue stream.
While we’re confident in the advantages and attributes of 3D-printed aviation components, there is still an element of resistance in some quarters due to a lack of trust that parts will be as strong or functional as conventionally built parts.
That’s probably a product of two conditions – a lack of familiarity with 3DP’s capabilities and resistance to change.
However, those reasons for delaying adoption of 3D-printed parts simply don’t hold up. While 3D-printed parts may not be appropriate for every aviation application, in many instances they can do the job as well or better than conventionally manufactured parts. Production is reliable and repeatable. Hundreds of thousands of 3D-printed parts are in flight today, with historical performance data and complete process documentation available to ensure compliance with all necessary standards and guidelines.
Wider adoption of 3DP means saving money and time while improving productivity and performance. The aerospace industry has an opportunity to take advantage of the unique capabilities of digital manufacturing to improve its MRO and manufacturing processes, leading to aircraft spending less time on the ground and more in the air, where they belong.
Materialise
https://www.materialise.com
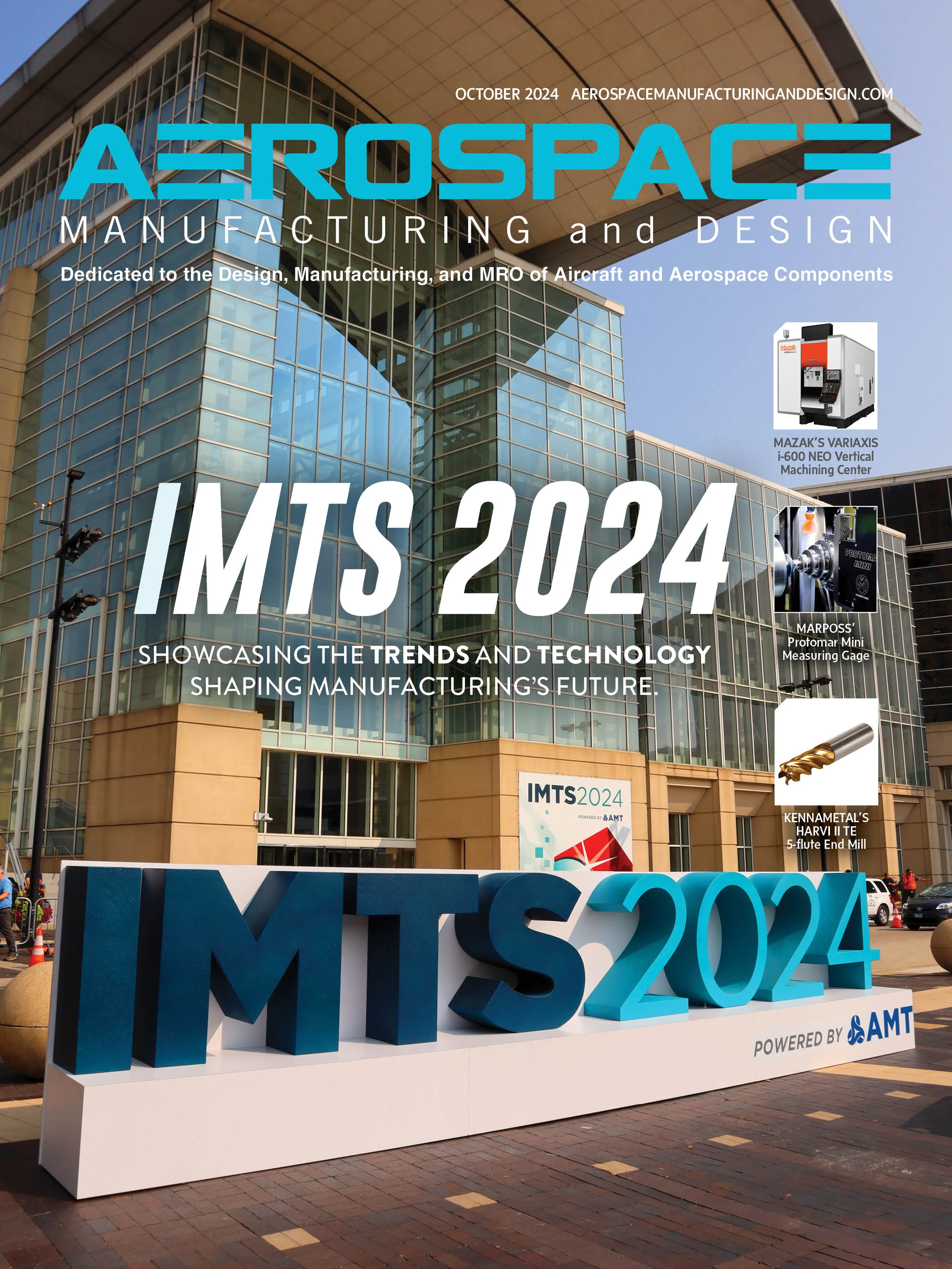
Explore the October 2024 Issue
Check out more from this issue and find your next story to read.
Latest from Aerospace Manufacturing and Design
- Talking machine tools with the professionals who build them
- Tools and strategies for improving your machining processes
- America Makes announces QTIME project call
- Innovation meets precision for 40% faster machining
- Upcoming webinar: Pro tips from a supply chain strategist
- Heart Aerospace relocates to Los Angeles
- Fixtureworks introduces Stablelock Clamps
- Piasecki acquires Kaman's KARGO UAV program