

In-process gaging on CNC cylindrical and peel grinders enables real-time monitoring and measurement of the workpiece’s outer diameter – essential for continuous, unattended production grinding. Detecting deviations caused by ambient environment thermal changes, oil temperature fluctuations, or grinding wheel wear minimizes the risk of producing out-of-tolerance parts. Additionally, it reduces the average cycle time by eliminating frequent stops to manually measure parts.
The measuring heads used in cylindrical and peel grinders gage the diameter of a workpiece using two feelers positioned on opposite sides, simulating the method of measuring with a micrometer. These gages often employ non-contact or minimal-contact technologies, such as laser, capacitive, or inductive sensors, to accurately measure the workpiece’s dimensions.
On a typical CNC cylindrical grinding machine, the gage remains in constant contact with the workpiece, providing real-time feedback and enabling continuous adjustments during the grinding process. On peel grinders, the gage only contacts the workpiece to take a reading once the machine stops, with the feedback being used to make corrections for the next part.
In-process gaging on CNC tool grinding machines involves monitoring several parameters, with one of the most critical being the outside diameter of the cutting tool, typically on endmills. This measurement can be performed using either a contact-based system, such as an electronic touch probe, or a more advanced non-contact laser measurement system. Touch probes have several drawbacks, including the risk of chipping the cutting edge (especially with carbide endmills), bending small tools during measurement, and inaccuracies when measuring variable helix endmills. A laser gage eliminates these risks by being contactless and capable of measuring the highest point of the cutting edge, even on complex 3- or 5-flute variable helix endmills.
Flute depth, while a non- critical dimension, requires attention because the fluting wheel removes most of the material from an endmill, making it prone to disproportionate wear and requiring regular adjustments. A touch probe can be used to measure flute depth. Another critical, yet often overlooked parameter is flute indexing. Eventually, wear on the fluting wheel can cause the indexing to shift, affecting the outer diameter and geometry of the front teeth.
To improve accuracy, run-out measurement and correction of the tool blank should be integrated into the production grinding process for various cutting tools, including endmills, drills, and reamers.
It’s essential to measure run-out at the front and back of the workpiece. The collet holding the workpiece can introduce lack of parallelism and off-center alignment. In a typical production environment, it’s usually sufficient to take these two measurements before beginning the grinding process. However, if extremely tight tolerances are required, the measurements should be repeated after flute grinding is completed. Due to the high grinding forces required for fluting, the blank may shift within the collet.
MyGrinding Inc.
https://www.mygrinding.com
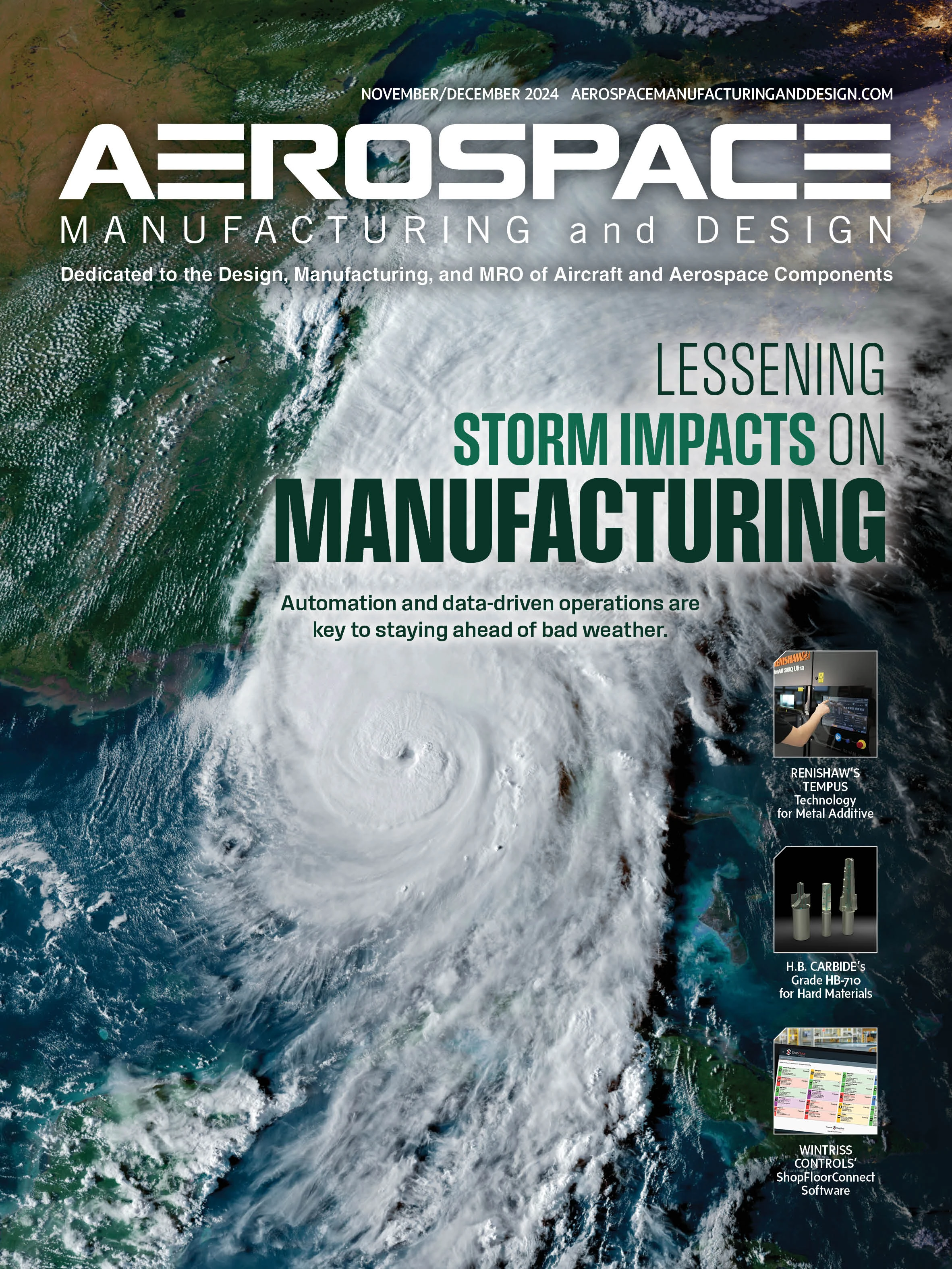
Explore the November/December 2024 Issue
Check out more from this issue and find your next story to read.
Latest from Aerospace Manufacturing and Design
- Mastering high-temp alloys with Kennametal Inc.
- Boeing to sell portions of digital aviation solutions
- SMW-Autoblok’s KNCS-matic 3-jaw power chuck
- 3 Questions with an Expert with Allied Machine & Engineering
- Electra raises $115M to pioneer Ultra Short aircraft
- Walter’s WT26 partial- and full-profile thread turning inserts
- April Manufacturing Lunch + Learn with Iscar
- April Manufacturing Lunch + Learn with Insaco