
Machining aerospace components demands an advanced skill set and extensive knowledge to navigate the ever-evolving challenges of today’s aerospace industry.
Aerospace shops are tasked with meeting increasingly stringent tolerances and mastering growing complexity in component features, while grappling with continuous advancements in materials that are exceedingly difficult to machine. Shops are also expected to prove out new components quickly, with little room for error, as a scrapped component could cost upward of hundreds of thousands of dollars.
Compounding these challenges is the widening skills gap caused by an aging workforce and fewer people from younger generations pursuing manufacturing careers. But as the challenges evolve, so do the innovations. New tools, techniques, and technologies have emerged, offering aerospace manufacturers more opportunities to enhance precision and productivity.
In this shifting environment, keeping machining knowledge up to date and upskilling teams is the key to maintaining a competitive edge. That may be easier said than done when a shop is occupied with the day-to-day demands of production. Fortunately, expert resources and industry partners can help teams advance. It’s just a matter of knowing where to focus training efforts to get the greatest return. Here are some essential strategies to elevate capabilities and drive more productive aerospace manufacturing.
1. Embrace technological change
Aerospace shops can really limit themselves by staying in their comfort zone – relying on the same equipment, technology, and techniques that have been moderately successful for them the past 20 or 30 years. This common mistake can put a drag on cost, efficiency, and productivity in any workshop.
For example, some shops may be more comfortable using older mills and lathes to machine a new component instead of working with a multitask machine to do more complex operations. Although it may seem like the simplest way to get production moving, it requires multiple steps and tool setups, resulting in more downtime compared to making the part with a single multitask setup.
Shops must take a holistic view of production and cost to understand how new technologies such as multitask machines, optimized tooling, and advanced digital solutions can benefit their overall operation. But investing in new technology is just the start. New tools, techniques, and CAM software are constantly emerging, helping maximize those technology investments, which means regular training can help support investments and ensure teams are using these technologies to their fullest potential.
2. Master multi-axis machining with the latest strategies
Advancements in multi-axis machining reduce downtime with fewer part setups, boost precision, and significantly reduce machining time with faster cutting action. Learning the latest multi-axis solutions and strategies can greatly improve a shop’s productivity but also requires dedicated training. Partnering with an expert tool or equipment provider who works with these innovations daily is the surest way to bring a team up to speed.
One advancement greatly benefiting aerospace shops is Y-axis turning – a new range of tools and cutting strategies leveraging the Y-axis on a multi-axis machine, rather than the X- or Z-axis used on a traditional lathe. The Y-axis is more rigid than other axes and can handle the most counteracting forces on a component when turning. This allows turning operations to cut much faster than traditional methods, while also enabling simultaneous index-turning methods for turning complex shapes much more efficiently.

Shops should also train their teams on the latest tool path strategies and verification tools for multi-axis machines. For example, when turn-milling complex engine cases or cylindrical and conical-shaped aerospace components, Sandvik Coromant offers a solution combining CAM programming tool path strategies with specialized calculators to predict and optimize the placement of the tool for each pass. This negates the need for point milling with a ball nose and allows the use of a large indexable cutter. The result is a much faster and more economical setup that can still hold extremely tight tolerances in a multitask operation.
3. Go deeper with digital machining
Many aerospace shops are evolving into highly digital environments. Using data from machine tools, shops today can take advantage of software platforms for machine monitoring and data analytics to gain insights into machine utilization, stop causes, alarms, and faults. Or they can use digital tool selection software to quickly find the optimal tool for their operation based on cutting data or other machining parameters.
It’s critical aerospace shops know how to properly use these digital tools and understand how to analyze the insights from the gathered data. Training helps ensure they can confidently use those insights in actionable ways that make a difference on the shop floor, from performing predictive maintenance to improving tool performance.
Many training programs include digital technology in their classes. Sandvik Coromant includes its smartphone applications and cloud-based software as part of its standard training. During hands-on practice on the shop floor, participants download an app and use it to calculate all the parameters to run a part. Incorporating digital tools transfers key skills and also makes classes more interactive and engaging.
Customized training can help shops with specific goals, such as learning new CAM programming or verification tools, and can help aerospace shops address unique challenges to improve their operations to meet business goals.
4. Optimize tool selection for advanced materials
Material science is constantly advancing, resulting in new, improved materials with higher heat resistance and better weight-to-strength ratios. While these advancements make aircraft more lightweight and fuel efficient, they also create challenges for machinists.

Whether a shop is working with titanium or nickel alloys, understanding the breadth of tools available and how they can impact the precision, productivity, and reliability of an operation is critical. Heat-resistant materials put intense heat back into the tool, which can dramatically reduce tool life and process security without the optimal cutting parameters. Training a team in the latest tool selection strategies can make all the difference between a profitable operation and costly mistakes.
As component materials continue to advance, so do the cutting tools, grades, geometries, and tool substrates. Exposing teams to the latest tooling solutions such as ceramic end mills, polycrystalline diamond (PCD) and cubic boron nitride (CBN) coated tools or optimized turning tools for titanium and nickel alloys can help shops unlock more advanced techniques and transform productivity.
To illustrate just how much of a difference tooling can make in aerospace operations, consider a recent case study with Sandvik Coromant and a company turning large turbine discs. Sandvik Coromant helped implement a new ceramic turning solution, a first for the company. Along with the new tooling solution, Sandvik Coromant also provided several remote training sessions and an on-site expert to support them with programming, cutting data, and tool path strategy. Once they were trained on the new tooling solution, they could machine their component 60% faster.
5. Train with a tool provider that has wide-ranging capabilities and expertise
Aerospace shops ready to invest in training have a wide range of options available. But there are certain criteria to look for in a training partner if shops want to get the greatest benefit to their business.
Find a partner who has long-standing expertise in the aerospace industry and wide-ranging capabilities in all aspects of the machining process. Training from experts with a holistic view of manufacturing can help teams connect the dots between engineering, planning, tool selection, programming, material sciences, and more. They’ll also have deeper industry partnerships, creating more opportunities for joint training sessions with partners in other disciplines.
A tool provider like Sandvik Coromant offers much more than basic training on a cutting tool or insert, they offer training services and engineering support for the entire machining value chain. Whether a team needs training assistance on finite element analysis (FEA), an online webinar on CAD/CAM programming and simulation, on-site training on tool monitoring, or hands-on training with the latest tools and techniques at a dedicated training facility, Sandvik Coromant can provide a range of training options to help teams achieve their goals.
When making critical components for aircraft, production needs to be precise, efficient, and on the cutting edge. Working with an expert partner who can train teams in theory as well as practical applications with firsthand learning will go a long way in making shops successful, now and in the future.
Sandvik Coromant
https://www.sandvik.coromant.com
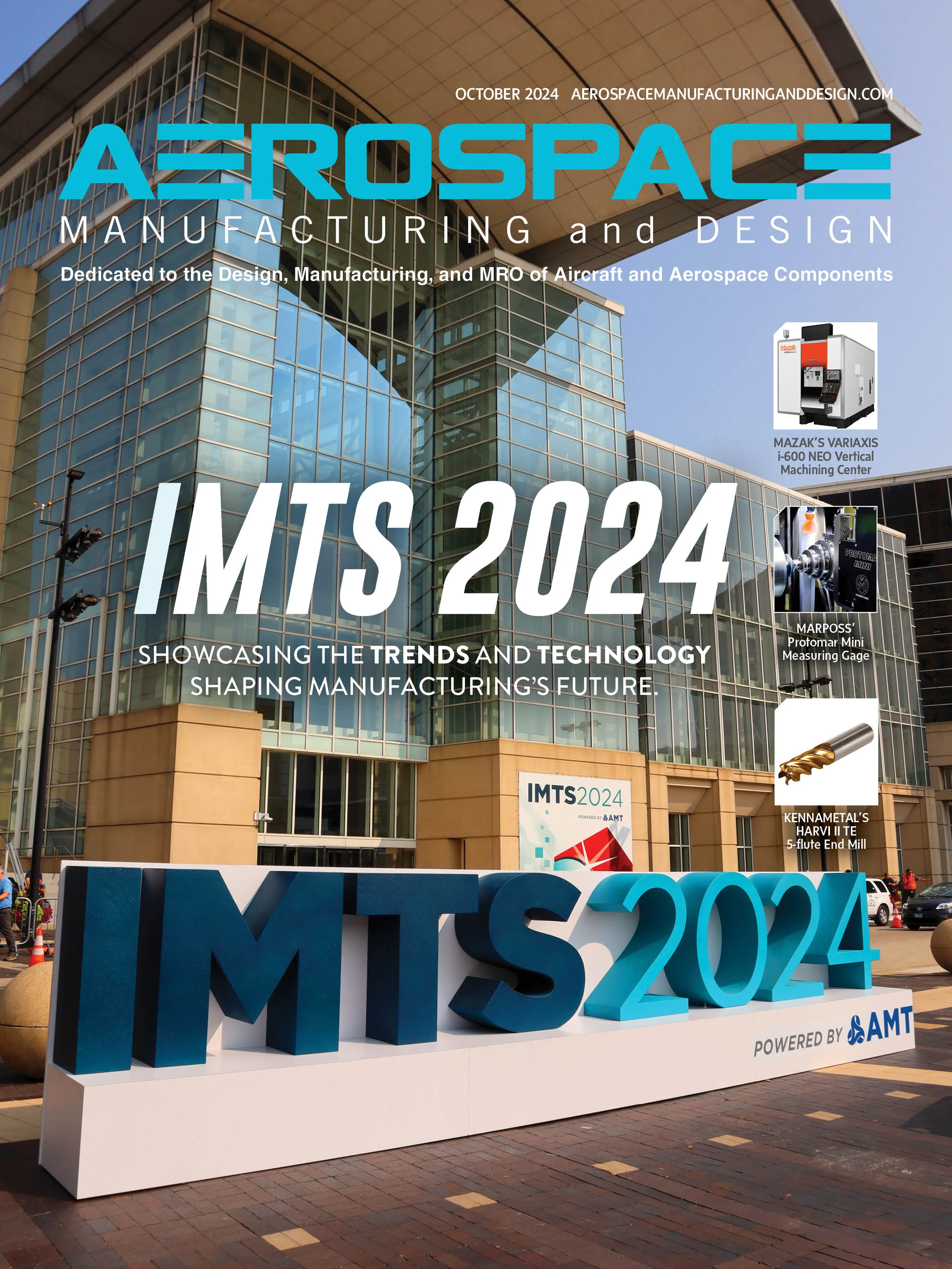
Explore the October 2024 Issue
Check out more from this issue and find your next story to read.
Latest from Aerospace Manufacturing and Design
- America Makes announces QTIME project call
- Innovation meets precision for 40% faster machining
- Upcoming webinar: Pro tips from a supply chain strategist
- Heart Aerospace relocates to Los Angeles
- Fixtureworks introduces Stablelock Clamps
- Piasecki acquires Kaman's KARGO UAV program
- PI Americas’ long-travel XY piezo nanopositioners-scanners
- AAMI project call submission deadline extended to May 12