
1. Drilling challenging aerospace materials demands an application- specific solution.
Stainless, titanium, and nickel-based alloys are highly heat resistant so heat generated during the drilling process is pushed into the cutter. These materials also exhibit an extreme amount of elastic memory which means the workpiece will tend to compress around the drilling tool, resulting in additional wear on tool margins. This behavior will also increase the amount of contact with the material, resulting in work hardening being introduced to the drilled hole, potentially making a follow up process like tapping or thread milling significantly more difficult. Manufacturers now have an excellent solution in EMUGE InoxDrill featuring solid carbide construction, a custom ALCR-T89 coating and polishing process, and a single margin design that reduces material adhesion and provides excellent hole guidance, ideal for material that can compress down on a drill. The special coating provides a 15% increase in surface hardness, a 22% increase in maximum operating temperature compared to AlTiN-based coatings, and a 200% increase in tool life during testing.
2. A drill’s cutting edge plays an important role.
A concave main cutting edge combined with optimized cutting edge preparation enables best cutting behavior at very high feed rates, optimal chip forming, and increased tool life. When drilling a highly abrasive form of austenitic stainless steel, a manufacturer attempted to use a solid carbide drill which wasn’t optimally designed for heat resistant materials and didn’t include coolant-through capability. The result wasn’t good, so they implemented InoxDrill and increased total hole count ten-fold, ran a higher feed rate and overall drill penetration rate, resulting in more than 30% cost savings.
3. Coolant-through design provides effective heat management and improved chip evacuation for increased tool life, better hole quality.
Coolant-through drills can often be run at higher speeds and feeds as the cooling and chip evacuation capabilities allow for more aggressive cutting parameters. This can significantly reduce cycle times, especially when drilling deep or difficult holes. Look for drilling tools that are coolant-through.
4. The right toolholder and drilling tool are equally important.
With high penetration rate drilling in aerospace applications, EMUGE high precision/performance FPC mill/drill chucks provide unprecedented rigidity, vibration dampening, concentricity, machining speed, and tool life. Featuring the world’s only chuck with a 1:16 worm gear, the FPC chuck’s patented design delivers 3 tons of traction force. The unique design provides 100% holding power for maximum rigidity, and the collet-cone assembly absorbs virtually all vibration for maximum dampening, allowing the high-performance drill to reach full speed and tool life.
5. Don’t go it alone.
For application assistance, we recommend working closely with technical support from your tooling manufacturer/supplier. For example, since InoxDrill has an accurately controlled hone on the primary cutting edge for edge protection, it’s necessary to have a much higher feed rate than many conventional drilling tools to ensure you’re maintaining positive cutting under the material for efficient material removal. EMUGE’s comprehensive support team can provide the proper guidance. When the machine and drilling tools are in an optimal zone, the results speak for themselves.

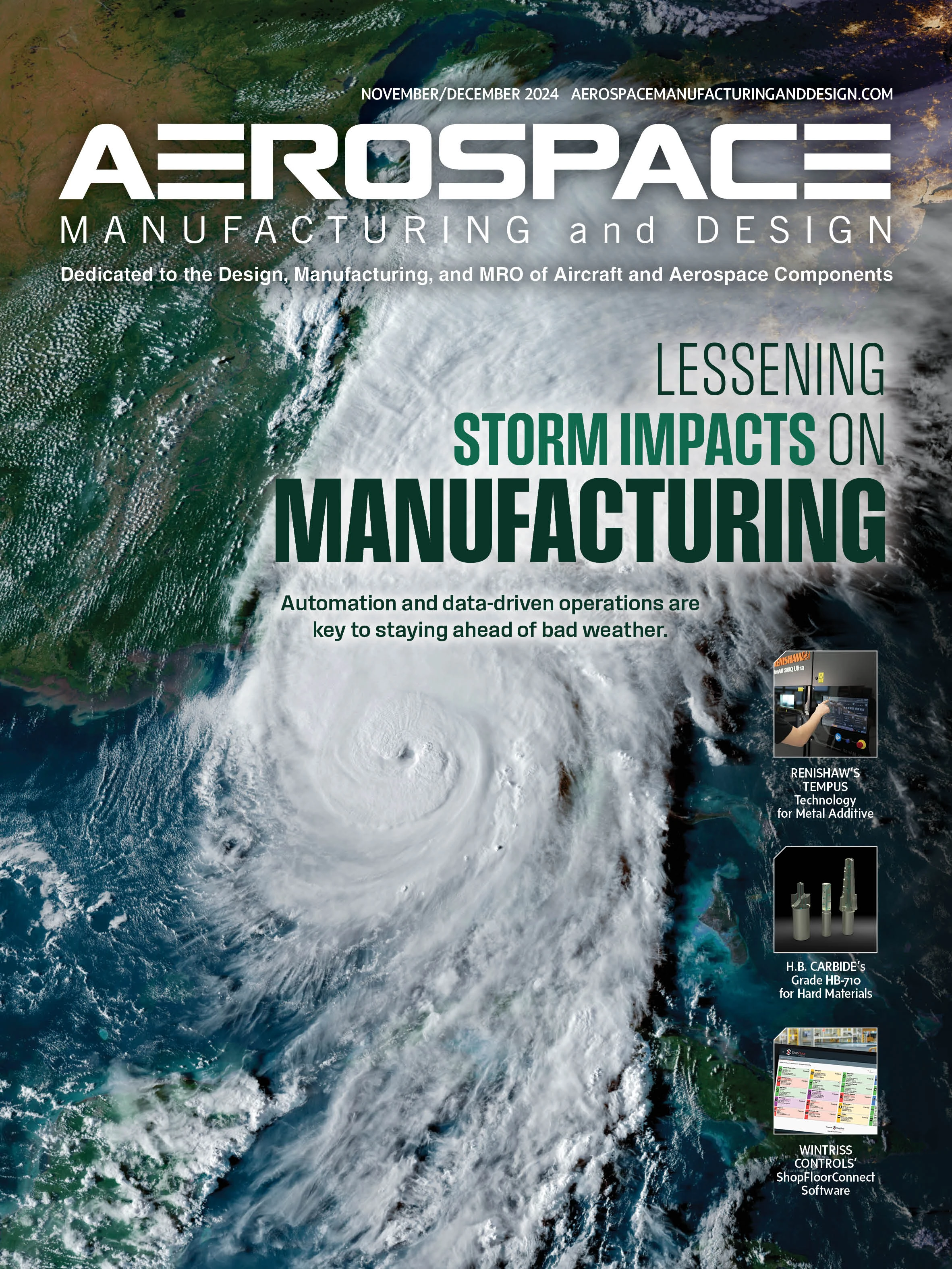
Explore the November/December 2024 Issue
Check out more from this issue and find your next story to read.
Latest from Aerospace Manufacturing and Design
- Talking machine tools with the professionals who build them
- Tools and strategies for improving your machining processes
- America Makes announces QTIME project call
- Innovation meets precision for 40% faster machining
- Upcoming webinar: Pro tips from a supply chain strategist
- Heart Aerospace relocates to Los Angeles
- Fixtureworks introduces Stablelock Clamps
- Piasecki acquires Kaman's KARGO UAV program