PHOTOS COURTESY OF BALLY RIBBON MILLS (BRM) UNLESS OTHERWISE NOTED.
NASA developed thermal protection system (TPS) technologies to protect spacecraft from the extreme heat conditions and entry environments space missions face. Working closely with the NASA Ames Research Center, Bally Ribbon Mills (BRM) developed a new generation of strong and robust materials produced using three-dimensional (3-D) weaving. In addition to use on existing missions, the new woven materials are expected to be used for future planetary missions.
Bally Ribbon Mills has been developing 3-D weaving since the company received a research contract from the United States Air Force Research Laboratory (AFRL) to develop the technology in the early 1990s. Alterations to existing looms led to a fully automated 3-D loom, which created orthogonal, isotropic, and quasi-isotropic composites, as well as near-net-shape and complex net shape preforms.
“3-D weaving is an emerging technology offering various benefits over two-dimensional (2-D) composite production and more traditional building materials, like steel and aluminum,” says Curt Wilkinson, BRM’s senior textile engineer. “Compared to traditional 2-D fabrics, 3-D weaving reduces weight, eliminates delamination often experienced with 2-D fabrics, reduces crack risks, and lowers production time. 3-D fabrics also offer direct and indirect manufacturing and operational cost reductions.”
New materials for compression pads
TPS materials protect a spacecraft from harsh heating and are typically thermally robust, low-density insulators that are somewhat fragile. For the human-rated Orion vehicle, some crucial parts of the TPS need to be extremely strong as they’re part of the vehicle structure. After Orion’s 2014 Exploration Flight Test-1 (EFT-1), engineers determined the existing materials used as the structural ablator wouldn’t work for future missions beyond low Earth orbit. The 2-D carbon phenolic material used for the EFT-1 compression pads has relatively low interlaminar strength and requires a metallic shear insert to handle structural loads.

There were few materials meeting demands of lunar return missions due to performance or part size limitations, so NASA began looking for TPS technology tailored to the specific needs of missions with human-rated spacecraft. NASA’s Orion/Artemis mission is preparing to send humans into deep space – with the goal of putting astronauts on Mars in the 2030s.
NASA began considering 3-D weaving technology for the Orion Multi-Purpose Crew Vehicle (MPCV), using compression pads serving as the interface between the crew and service modules. The multiple pad locations in the heat shield serve as a part of the mechanism for holding the crew and service modules together during most mission phases prior to separation, followed by the crew module’s Earth reentry. The compression pads must carry the structural loads generated during the two modules’ launch, space operations, and pyroshock separation, and serve as an ablative thermal protection system that can withstand the high heating of Earth reentry.
BRM began working on the 3-Dimensional Multifunctional Ablative Thermal Protection System (3D-MAT). The project combines 3-D weaving of quartz yarns with resin transfer molding to develop a multifunctional material architecture capable of meeting structural and thermal performance needs for lunar return and beyond. The material is made by 3-D weaving quartz yarns and infusing them with a cyanate ester resin. BRM’s 3-D orthogonal weave with high fiber volume showed a 900% increase in tensile strength in the Z direction, and the resin infusion fully densified the material so there are no pores, locking in strength and robustness.

NASA provided BRM with requirements on fiber volume and fiber percentages. BRM suggested a preform weave and design 4x larger than the largest preform ever woven at BRM. Development required significant equipment modification and procurement of a new loom harness design to individually control 5,000 yarns.
The project was the first achievement of continuous, automated 3-D orthogonal weaving at large scale (12ft x 3ft) and high fiber volume (60%), featuring a cross section 4x larger than the prior. The project also resulted in an innovation in resin infusion, with full resin densification of large 3-D preforms established for the first time (<1% porosity). This maximized the strength of the 3D-MAT composite, at a factor of 12x thicker than the prior state of the art for full densification.
The materials and architecture resulted in an extremely high-performance composite. Compared to the 2-D carbon phenolic used on Orion EFT-1, 3D-MAT is 9x stronger in tensile strength (Z); 3x stronger in shear strength; and 25% lower in thermal conductivity.

The heat shield compression parts must be light and strong to connect the two modules in a structural way while also managing heat.
Bally Ribbon Mills (BRM)
https://www.ballyribbon.com
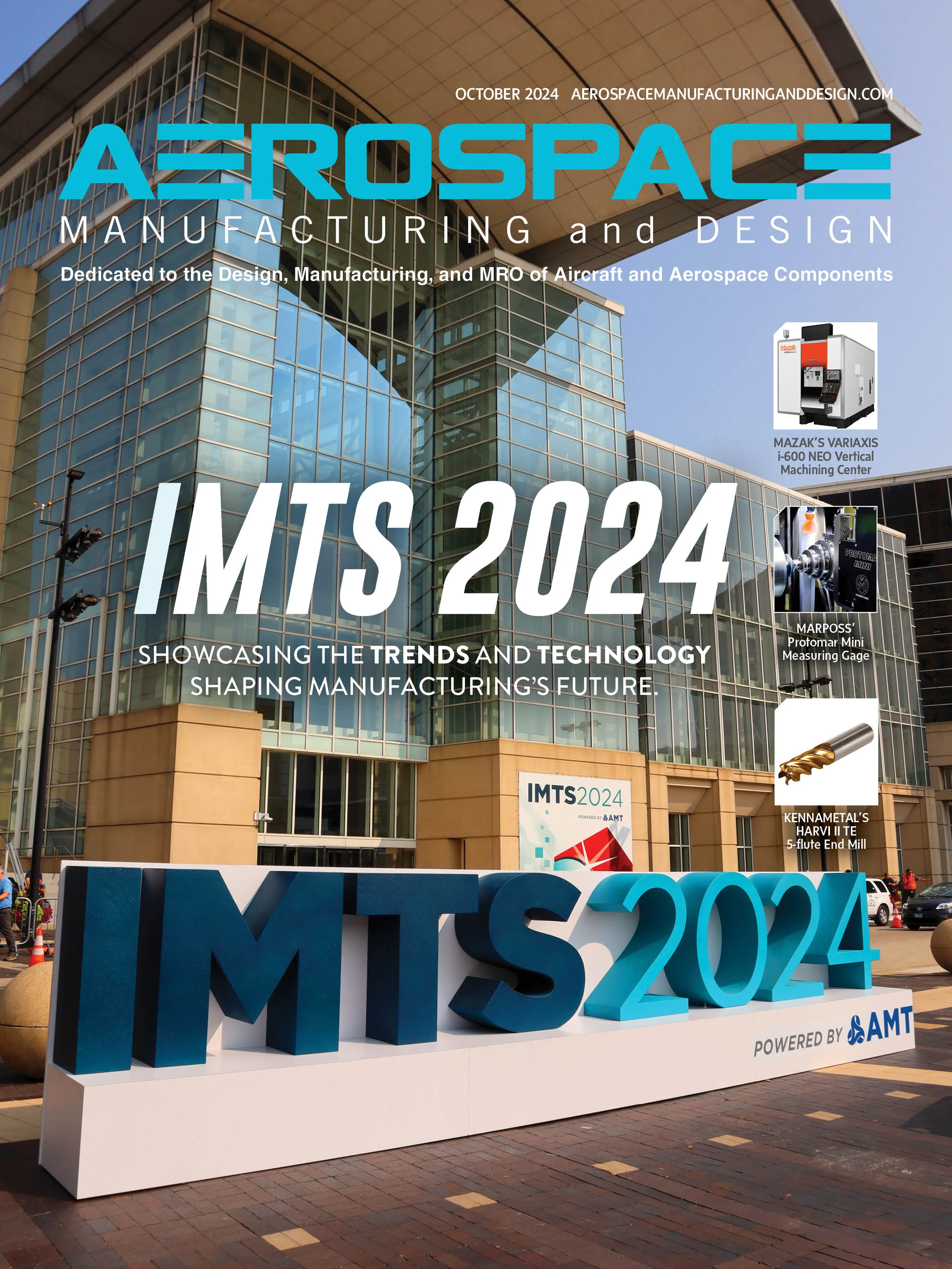
Explore the October 2024 Issue
Check out more from this issue and find your next story to read.
Latest from Aerospace Manufacturing and Design
- Talking machine tools with the professionals who build them
- Tools and strategies for improving your machining processes
- America Makes announces QTIME project call
- Innovation meets precision for 40% faster machining
- Upcoming webinar: Pro tips from a supply chain strategist
- Heart Aerospace relocates to Los Angeles
- Fixtureworks introduces Stablelock Clamps
- Piasecki acquires Kaman's KARGO UAV program