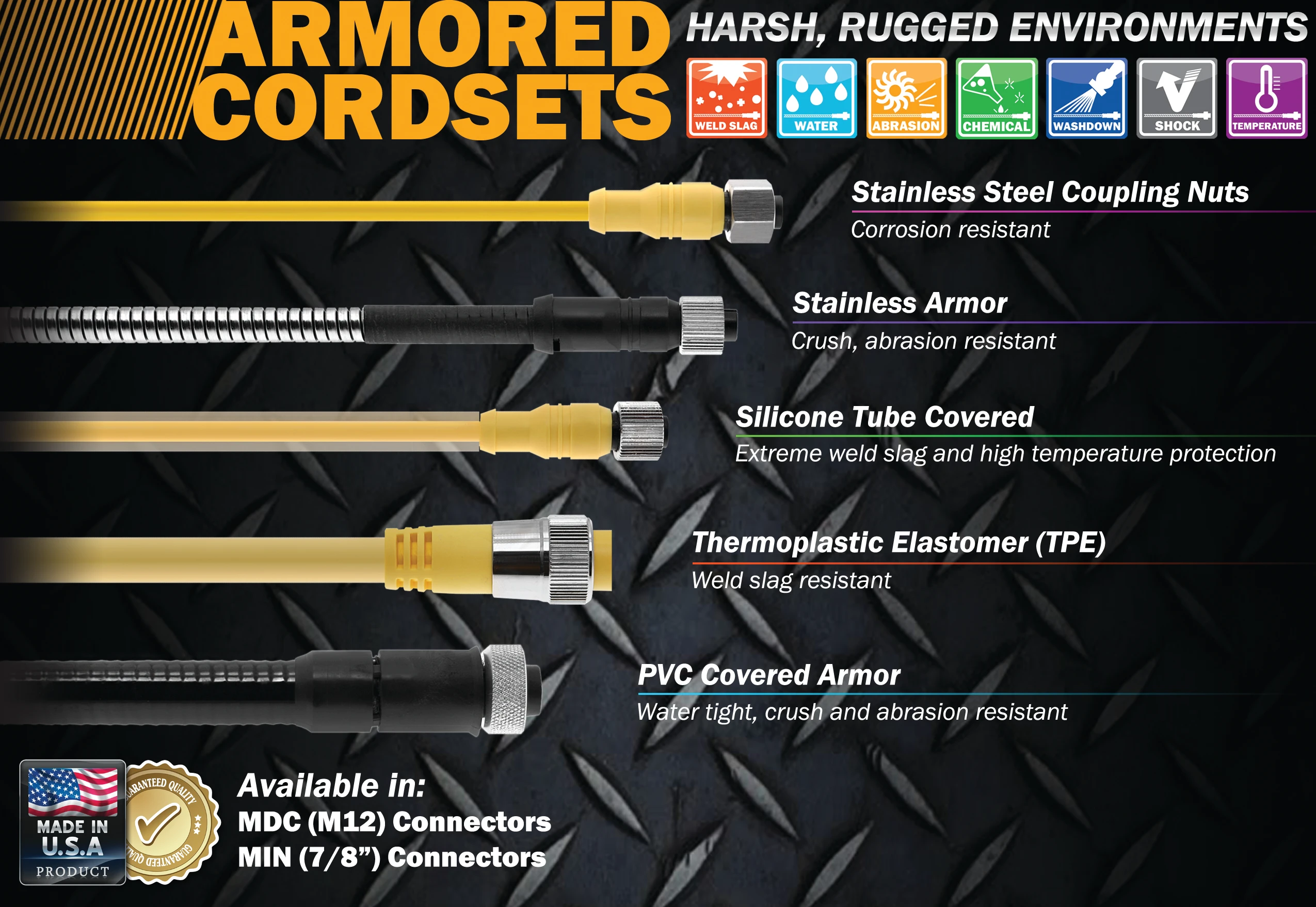
Mencom Corporation will introduce its new Armored Cables for use in harsh manufacturing environments at IMTS – The International Manufacturing Technology Show 2014 being held at Chicago’s McCormick Place September 8-13. Mencom Corporation can be found in Booth #E-4674 in the Industrial Automation North America Pavilion which is located in the Lakeside Center(East) Building.
One of the biggest challenges that every manufacturer struggle with is how to prevent downtime or outage caused by connection failure. Abusive manufacturing environments with extreme conditions are where these issues are most likely to take place. Sometimes it is difficult to diagnose and locate the exact problem of the failure because of its complex installation or location. Short and repetitive downtime with constant replacement is usually caused by cable failures and can be prevented by installing proper cables equipped with extra protection.
In most cases the downtime is usually caused by one of following conditions:
• Physical failure by repetitive impacts and abrasion with loaded components
• Damage by high pressure wash-down and cleaning chemical
• Damage by extreme temperature
• Weld Slag
The Mencom Armored Cables are designed to prevent failure from such common causes above. The cables feature a stainless steel coupling nut and stainless steel armor jacket which prevent water damage from high pressure washdown, cleaning chemicals and extreme temperature. A silicone tube-covered jacket prevents physical failure by repetitive impacts and abrasion with loaded components as well as protecting the cable from weld slag. A thermoplastic elastomer jacket protects the cable from cleaning chemical. They are available in MDC(M12) connectors and MIN(7/8 inch) connectors. Custom solutions including wiring and custom pin counts are also available.
Armored Cable Specs
SS nuts
• 316 SS = 0.08% carbon
• As opposed to 316L, which is 0.03% or less
• The higher the carbon content, the harder the steel
• Max temp - 1800ºF
• 316 is Austenitic (cannot be hardened by heat treatment), non-magnetic, highly stain resistant
• Resistant to most Alcohols, Sodium & Calcium brines, hypochlorite solutions (i.e., Sodium Hypochlorite-bleach, or Calcium hypochlorite, pool ‘chlorine’), phosphoric acid, sulfites and sulfurous acids. Due to presence of molybdenum, 316 is resistant to pitting caused by chlorides common in 304 alloys.
• Susceptible to Aluminum Fluoride, Bromine, etching chlorides, Phosphoric Acid (>40%), Silver Bromide, Sodium Fluoride, Sodium Hypochlorite (100%), Sodium Sulfide, Sulfur Chloride, Sulfuric Acid (>10%), and Tin Salts
316 SS is more resistant to both corrosion and oxidation than the 304 varieties of alloys. The HEX shape ensures that particles will not stick to the knurl during cleaning and make this coupling nut ideal for USDA inspectable facilities where potential caustic materials and high pressure wash downs are likely.
SS armor jacket
• MDC = 0.250” ID/ 0.345” OD
• Approx. 0.110 LBS/ft
• MIN = 0.500 ID / 0.600 OD
• Approx. 0.180 LBS/ft
• 304 SS – 0.08% carbon, often referred to as 18-8 due to the minimum requirement of 18% Chromium-8%
Nickel
• 304 is Austenitic (cannot be hardened by heat treatment), non-magnetic, highly stain resistant
• Max temp - 1800ºF
• Resistant to sterilizing solution, most organic chemicals, and a wide variety of inorganic chemicals
• Susceptible to pitting from chlorides, Susceptible to Aluminum Fluoride, Bromine, etching chlorides, Phosphoric Acid (>40%), Silver Bromide, Sodium Fluoride, Sodium Hypochlorite (100%), Sodium Sulfide, Sulfur Chloride, Sulfuric Acid (>10%), and Tin Salts
304 SS is the most common of the SS family. The chromium-nickel content and low carbon content create a highly durable alloy resistant to oxidation and corrosion. Found in almost every industry where ease of cleaning and the prevention of product contamination are paramount, the SS Armor Jacket also provides an abrasion resistance unattainable in the thermo-plastic materials.
PVC covered SS jacket
• Same specs for SS tubing
The PVC coated SS offers all the benefits of the SS jacketed cables with added ingress protection provided by a full PVC wrap.
Silicone tube jacket
• Consistent with FDA Regulations for Food Contact
• Does not support microbial growth
• Animal Fat and Chemical Resistant
• Resistant to organic solvents, strong acids, strong alkalis, UV, sea water, oxygen, and ozone
• Susceptible to oxidation at temperatures beyond the cable capacity (500ºC), and shows thermal stability (maintains properties over a wide range of operating temperatures, -100 ºC to 250 ºC)
• Susceptible to Acetone, hydrocarbons, asphalt, Benzene, many chlorine compounds, freons, gasoline, ethyls, lubricants, ketones, naphtha, propane, turpentine, xylene
TPE
• Thermoplastic elastomer (can be re-melted and re-formed) with physical properties and performance of a thermoset (cured, or vulcanized) rubber.
• Service range is typically -50ºC to 170ºC
• RoHS Compliant
• Resistance to Chlorines, Caustic Soda, Diesel Fuel, Glycerin, Glycol, Hydrogen Peroxide, Naphtha, Bleach, & Sea Water.
• Susceptible to Acetone, Benzene, Ether, Ethanol, Formic Acid, Freon, Isopropyl Alcohol, Nitric Acid, MEK, Phosphoric Acid, & Xylene.
Due to its chemical and abrasion resistance, TPE is an easy choice for potentially harsh environments requiring sanitation and wash-down procedures. TPE offers the flexibility of expensive thermoset materials making it suitable for a variety of applications from Automotive to Welding.