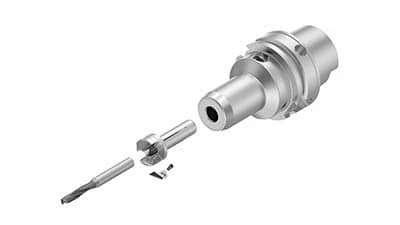
Kennametal has introduced the HiPACS drilling and countersinking system for aerospace fastener holes. Designed to drill and chamfer holes in one operation, the high-precision tool meets the aerospace industry's stringent accuracy requirements, while delivering increased tool life in machining composite, titanium, and aluminum aircraft skins.
“Most fastener hole tools used today are complex made-to-order tools with long lead-times,” says Kennametal Product Manager Georg Roth. “HiPACS uses standard, off-the-shelf components for quick delivery and low cost per hole, by allowing the drill and chamfer insert to be indexed independently from one another. What’s more, it’s the only indexable drilling and countersinking system on the market that can hold the aerospace industry’s required fastener hole chamfer tolerances in just one operation.”
Three simple components eliminate the need for custom tooling:
-A reducer sleeve with a built-in high-precision pocket seat. In conjunction with a standard hydraulic chuck, this component provides ultra-secure clamping and a runout of no more than 3µm, significantly increasing tool life and hole quality.
-A PCD countersinking insert. This eliminates the need for expensive custom solution step drills, reducing manufacturing costs while meeting the industry’s accuracy requirements.
-The two series of solid carbide drills – both diamond-coated and PCD-tipped – covering all material combinations found in a typical aerospace assembly. In addition, the straight shanked tools allow for length adjustments in increments of 10mm.
The HiPACS drilling and countersinking system can be used on all machines typically used for aerospace applications. In less stable conditions such as robot end effectors, the diamond coated carbide drills offer excellent tool life and hole quality. PCD-tipped drills excel in stable conditions such as gantry machines.