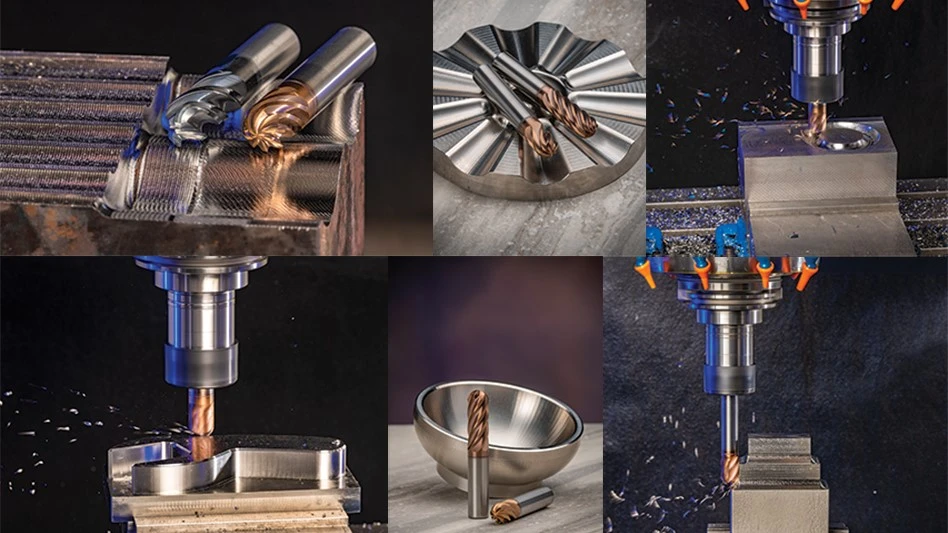
IMCO Carbide Tool launched the POW-R-ARC ball-end cutters, high-performance solid carbide cutting tools.
Designed for 3D contouring and chamfering at the fastest possible speed and feed rates, POW-R-ARC cuts and finishes in hardened metals up to 62 HRc, aluminum, stainless steel, low carbon steel, and super alloys such as high nickel alloys, cobalt chrome, and titanium.
“We focused on speed and high feed rates, and POW-R-ARC exceeded all expectations,” says Matt Osburn, IMCO vice president and technical director. “Available with 6 or 8 flutes, POW-R-ARC cutters feature advanced geometries, free-cutting design and a next-generation coating for faster feed rates, greater lubricity, and reliable chip clearance in most materials.
“Increasing the flutes from the traditional 4-flute tools to 6 or 8 flutes dramatically increases speed and feeds,” he says. “POW-R-ARC provides a great finish with a second pass. No stopping to change tools. No need to even stock dedicated finishing tools. And tests show POW-R-ARC lasts longer.”
Nearly 5x faster
In a recent test, a mold maker was cutting P20 steel and 4140 low alloy steel using a competitor’s tool running at 88ipm. After eight hours’ roughing with the competitor’s tool, they threw it away. After 16 hours’ semi-roughing and finishing with the competitor’s tool, they discarded that tool too.
Then they tried a POW-R-ARC cutter, running at 450ipm – nearly five times the speed – and completed roughing and finishing using the same tool. POW-R-ARC cut cycle time by half, from 24 hours (roughing to finishing) to 12 hours, and it more than doubled the tool life; it was still going strong after 32 hours.
“Just one POW-R-ARC tool did all the work and kept on going,” Osburn said.
The POW-R-ARC works well in machines with lower-max-speed spindles as well as high rpm machines. The unique geometry evacuates the chips, reducing the chances of loading up, even at a lower rpm. Long necks can be ordered for working in pockets and around mold guide pins.
POW-R-ARC also is ideal for 5-axis machines, with the added number of effective cutting flutes going from the OD all the way to the tip of the tool.
Cutting dissimilar materials
According to Steve Avers, IMCO’s technical support manager, even greater savings are seen when cutting across dissimilar materials, which typically requires handwork to eliminate digs where materials meet.
“Molds and dies, medical implants, turbine blades and glass molds often have abutting materials with different characteristics,” Avers says. “POW-R-ARC cuts through both materials smoothly, eliminating digs where edges meet. The time-consuming handwork required to remove these digs. POW-R-ARC cutters are serious time savers and game-changers.”
Designed for 3D contouring and chamfering at the fastest possible speed and feed rates, POW-R-ARC cuts and finishes in hardened metals up to 62 HRc, aluminum, stainless steel, low carbon steel, and super alloys such as high nickel alloys, cobalt chrome, and titanium.
“We focused on speed and high feed rates, and POW-R-ARC exceeded all expectations,” says Matt Osburn, IMCO vice president and technical director. “Available with 6 or 8 flutes, POW-R-ARC cutters feature advanced geometries, free-cutting design and a next-generation coating for faster feed rates, greater lubricity, and reliable chip clearance in most materials.
“Increasing the flutes from the traditional 4-flute tools to 6 or 8 flutes dramatically increases speed and feeds,” he says. “POW-R-ARC provides a great finish with a second pass. No stopping to change tools. No need to even stock dedicated finishing tools. And tests show POW-R-ARC lasts longer.”
Nearly 5x faster
In a recent test, a mold maker was cutting P20 steel and 4140 low alloy steel using a competitor’s tool running at 88ipm. After eight hours’ roughing with the competitor’s tool, they threw it away. After 16 hours’ semi-roughing and finishing with the competitor’s tool, they discarded that tool too.
Then they tried a POW-R-ARC cutter, running at 450ipm – nearly five times the speed – and completed roughing and finishing using the same tool. POW-R-ARC cut cycle time by half, from 24 hours (roughing to finishing) to 12 hours, and it more than doubled the tool life; it was still going strong after 32 hours.
“Just one POW-R-ARC tool did all the work and kept on going,” Osburn said.
The POW-R-ARC works well in machines with lower-max-speed spindles as well as high rpm machines. The unique geometry evacuates the chips, reducing the chances of loading up, even at a lower rpm. Long necks can be ordered for working in pockets and around mold guide pins.
POW-R-ARC also is ideal for 5-axis machines, with the added number of effective cutting flutes going from the OD all the way to the tip of the tool.
Cutting dissimilar materials
According to Steve Avers, IMCO’s technical support manager, even greater savings are seen when cutting across dissimilar materials, which typically requires handwork to eliminate digs where materials meet.
“Molds and dies, medical implants, turbine blades and glass molds often have abutting materials with different characteristics,” Avers says. “POW-R-ARC cuts through both materials smoothly, eliminating digs where edges meet. The time-consuming handwork required to remove these digs. POW-R-ARC cutters are serious time savers and game-changers.”