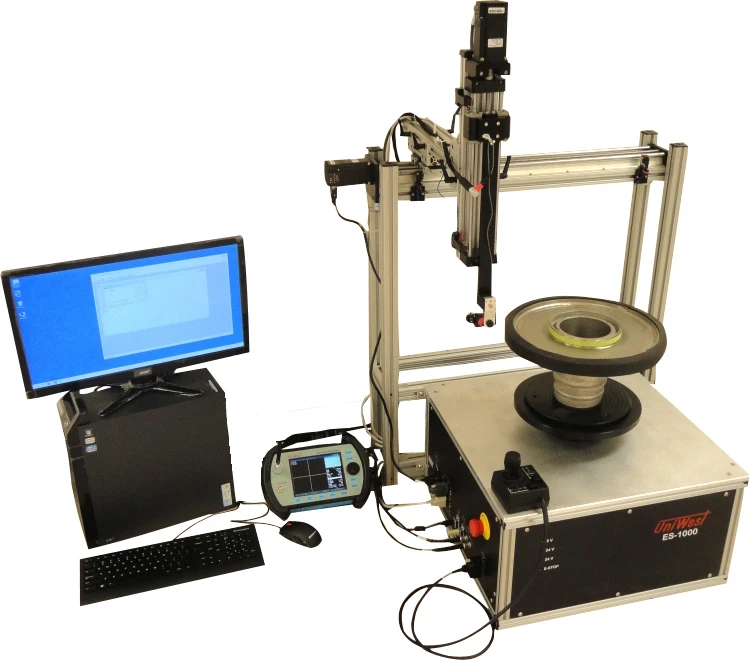
Engineers at UniWest have developed a new tabletop, 3-axis, semi-automatic ECT inspection system. The ES-1000 provides precision eddy current testing for rotationally symmetric parts, such as engine disk bores and webs.
The new unit enables substantial capacity utilization efficiencies for global OEMs at the same time it places semi-automated eddy current testing within the financial reach of smaller regional jet engine maintenance facilities.
For large organizations, including aircraft manufacturers and global aircraft maintenance facilities, many of whom already own one or more full-scale ETC-2000 systems, the ES-1000’s modular design allows sharing of existing components, such as probes, part-mounts, and signal processing instruments as well as computers and monitors, between eddy current testing systems. All of UniWest’s eddy current instrument series, such as the US-454, US-454A and the new EddyView Pro and Premium can be used with the ES-1000. In addition to equipment acquisition cost-efficiencies, component sharing allows larger organizations to allocate their eddy current testing workload across all UniWest ECT resources.
For regional facilities servicing smaller jet aircraft, the ES-1000’s acquisition cost makes investing in a semi-automated eddy current system a viable business proposition when compared to a full-scale system.
The modular ES-1000 system comprises four operationally independent components: 1) turntable and gantry module; 2) eddy current generation and processing instrument; 3) eddy current probe, and 4) computer and display, running Windows 7 or higher.
The systems’ essential component is the 24”square turntable which is fully compatible with all UniWest mounting mechanisms. The turntable and extendable gantry accepts parts up to 30 inches in diameter and 12 inches tall. For inspection of larger parts, custom gantry and probe-arm configurations can be readily fabricated.
The turntable module’s 32” wide gantry rail and attached probe arm are fitted with servo-driven lead screws for horizontal and vertical placement of the probe. Any of UniWest’s full complement of more than 3,000 eddy current probes may be attached to the probe arm by means of appropriate holders.
System setup is a simple matter of placing a part on the turntable, positioning the probe-head at the scan initiation point and pressing the software start button. The system then automatically scans the part using a pre-programmable routine.
In addition to the obvious cost efficiencies associated with component interchangeability, the ES-1000 is subject to less downtime because components are easily swappable from one system to another. For instance, while an instrument is out of service for factory calibration, or when a hard drive or video monitor fails, the problem can be quickly remedied by simply replacing the out-of-service component, reinstalling the ES-1000 software, if necessary, and rebooting the system.
Although the ES-1000 system is not designed for multi-dimensional motion at this time, minor contour following is afforded by spring compliance of the probes. UniWest anticipates the future development of software upgrades to accommodate inspection of curvilinear parts such as turbine fins.
The ES-1000 provides essentially the same precision as UniWest's full-featured ETC-2000 jet engine scanning system, with a reduced number of more complex performance features, for about a quarter the cost of the larger system. This new, value-optimized system is suited for both original equipment manufacturers where work allocation and capacity utilization are important, as well as for regional maintenance facilities where larger ECT systems have been prohibitively expensive.