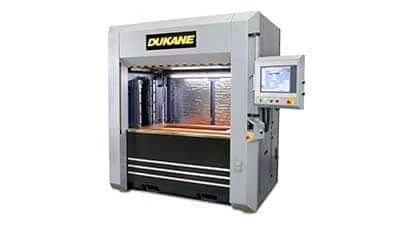
St. Charles, Illinois – The VW6000 series with Melt-Match line of servo driven vibration welding tools simplify vibration welding, providing faster cycle times driven by high speed servo motors that improve weld quality and consistency.
The VW6000 provides a larger welding table in the industry’s smallest footprint, 25% smaller than current models. The Melt-Match plastic welding process repeatably detects melt transition from solid to molten state, then accurately controls the melt flow of a thermoplastic material during the weld and transitions from the molten to solid state.
A servo drive and servo controller deliver the fastest approach and provide optimal contact force. Force sensing and digital force read-out provide better control of the trigger and welding force.
The patented Melt-Detect feature resumes motion once the plastic material has started to melt. Melt-Detect avoids weld joints deformation and cold welds for uniform melt and a hermetic seal.
Melt-Match parameters control the welding process in motion with real-time, closed-loop force control in addition to the real-time velocity control. Force and weld velocity can be programmed in 10 independent segments to match the melt flow rate of the material.
VW6000 series is Industry 4.0 ready providing remote connectivity for faster diagnosis, data acquisition, and service via most prevalent industrial communication protocols.
HMI software can store up to 200 weld setups/recipes for continued production of different parts or manage parts from different vendors. On-tool controls assure parts are present, held in place, and reduce manual errors.
Incorporating servo driven controls eliminates hydraulic power units. It includes four continuously supported rails with eight reciprocating bearings to eliminate table chattering, improve table alignment, and eradicate unwanted machine resonance. Large mechanical mass of the linear vibration head coupled with the solid welded tubular steel frame construction eliminates machine failure due to vibration process and provides one of the quietest machines in the industry, reducing operator fatigue.