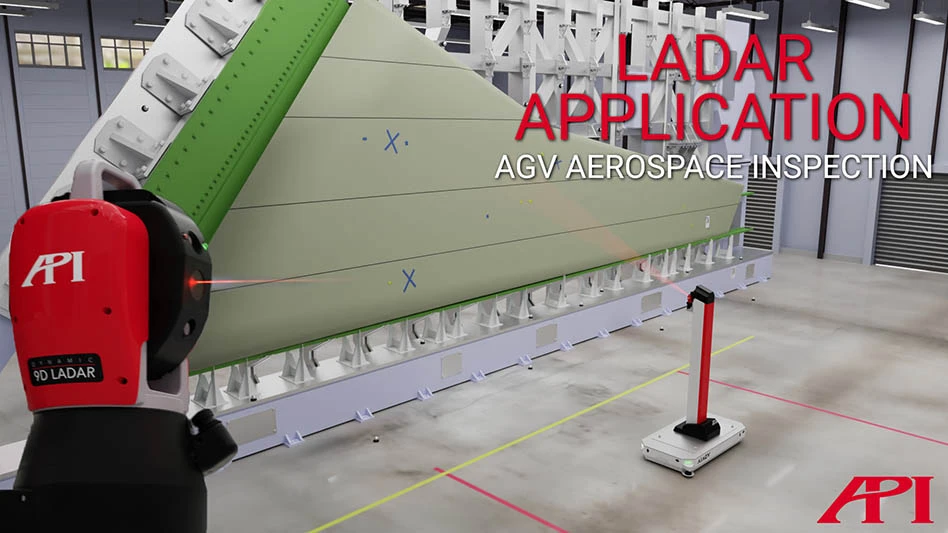
Automated Precision Inc. (API)
Automated Precision Inc. (API), a global pioneer in dimensional metrology solutions, introduces a new approach to aerospace manufacturing inspections with its Dynamic 9D LADAR mounted on an autonomous guided vehicle (AGV).
The aerospace sector, known for its rigorous quality standards and precision manufacturing requirements, has long sought ways to automate its processes for faster, more accurate data collection. API's Dynamic 9D LADAR represents a fast and precise non-contact measurement system.
When integrated with an AGV, the 9D LADAR system offers flexibility and coverage across the manufacturing floor, navigating autonomously and adjusting its measurement height as needed. With a 2m range and a scanning speed of 0.2seconds/cm², the non-contact system captures dimensional and surface geometry data.
Key Benefits of the 9D LADAR System for Aerospace Manufacturers:
• Accuracy: With 3D accuracy of 25μm + 6μm/m (2 sigma), the system guarantees precision in every scan.
• Efficiency through automation: By eliminating manual inspections, the system reduces potential human errors and allows skilled workers to focus on more intricate tasks.
• Seamless integration: The system can be easily integrated into existing manufacturing processes and is compatible with third-party metrology software.
• Boosted productivity: Rapid, precise, and automated inspections lead to increased measurement throughput, resulting in cost savings and enhanced performance.
With a global presence and dedicated customer support, API ensures that aerospace manufacturers worldwide can leverage this state-of-the-art technology.