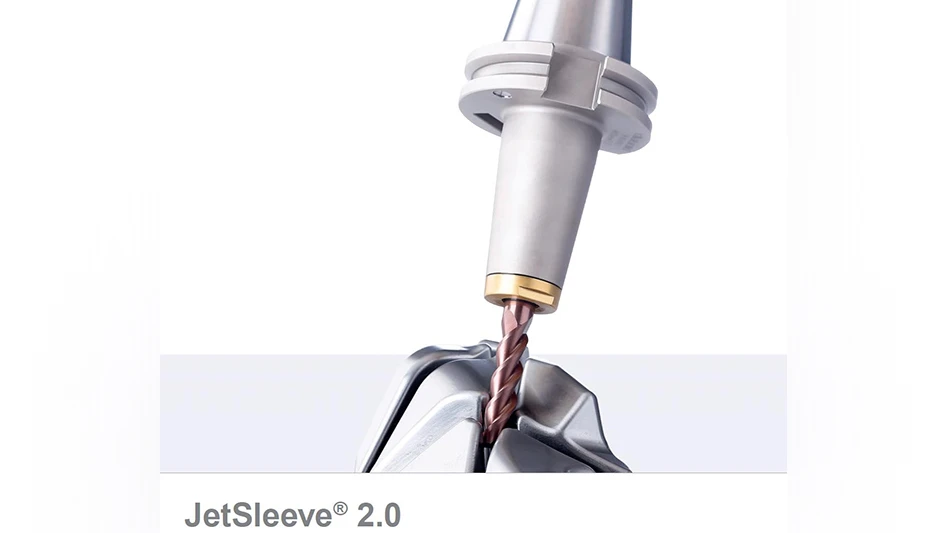
Accutek USA
Milling of deep contours and cavities has caused problems in every milling operation in the recent years, because chips could not be flushed away and the cutters did overrun the chips they were making. This caused milling cutter breakage with consequences to quality, surface finish, and accuracy of the workpiece. The first innovation step was in 2008; a separate coolant supply sleeve was put over the shrink holder including an injection adapter that was mounted near the spindle nose of CNC milling machines. This required mounting work on the machine and a retooling of the machine magazine. Machine tool builders did not like to modify their machines just for the coolant supply purpose. The Diebold designers then came up with the idea that an aluminum sleeve with integrated nozzles should be screwed directly onto the shrink fit holder. JetSleeve was born and could be inserted into the spindle like any standard tool holder.
In 2015, the Diebold engineers succeeded in a further breakthrough development and came up with the JetSleeve 2.0: the aluminum sleeve was replaced by a ring the size of a wedding ring, like the classic Diebold Goldring design that is being used on other Diebold tool holder types. The ring does not need to be removed for the shrink fit process when tools must be changed. The ring is made of the same material as the tool holder and is therefore stable to temperature.
The tiny nozzles are still incorporated into this jet ring, air-oil mixture, coolant or only air can be sprayed to the tip of the milling cutter at high pressure caused by the nozzles. Diebold offers a modified MQL (minimum quantity lubrication) JetSleeve tool holder for air-oil injection that allows to work with true Minimum Quantity Lubrication - a real breakthrough in MQL technology, even for high-speed machining at 50.000rpm. The inner contour is designed for this purpose to make sure that MQL is available immediately after any tool change and even up to 50,000rpm. When using JetSleeve 2.0, chips are immediately blown away from the cutter area even in difficult-to-access deep cavities. Now cutter damage by overrunning chips is impossible. This increases tool life by 100 to 300% and frequent re-start of the CNC programs, as required earlier after changes, is no longer necessary. Now, with this extra insurance, “lights-out” production is possible.
Like an internal coolant supply, the cooling medium is passed through the JetSleeve 2.0 tool holder. High coolant pressure is created by tiny nozzles at the nose of the tool holder and sprayed towards the tip of the cutter. The Venturi Effect points the coolant directly to the cutter tip to blow away the chips effectively in milliseconds. The JetSleeve 2.0 offers some more advantages: because the aluminum sleeve has been replaced by a ring, the shrink fit holder has a thicker wall which results in a higher holding force for the cutter, higher vibration dampening and less unbalance. For the shrink fit process, no aluminum sleeve must be removed.
Shrinking is done with the nozzle ring attached. The nozzle ring is TIN-coated, which makes the nozzles more abrasion-resistant against media flow under high pressure. The nozzles will not wear out, they’ll keep their correct size, and the angle of attack of the coolant will not change. With the innovative JetSleeve 2.0 all workpieces can be milled completely in one operation. Many contours can be finished on milling machines without the need to manufacture electrodes for EDM, a separate process on EDM machines or additional clamping of the work piece. JetSleeve 2.0 can be used in heavy-duty machining, standard milling and in micro-production. Summing up all the advantages of the innovation JetSleeve 2.0, users will achieve a much higher output of their machines, easily saving money on each operating minute.