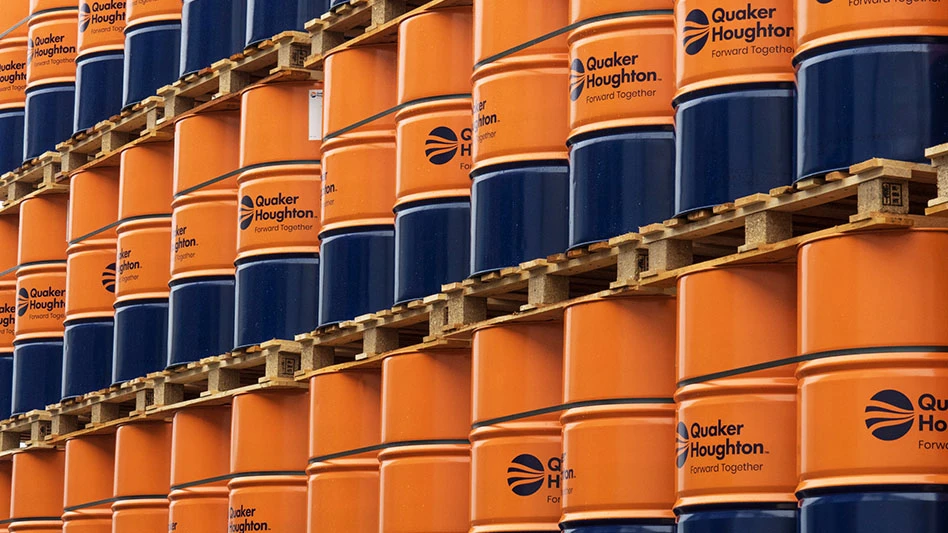
Photo courtesy Quaker Houghton
Characterized by stringent quality control and manufacturing standards, the aerospace industry must consistently meet high performance standards and ensure compliance with regulations and approvals across its day-to-day supply chains and workflow management.
To achieve success in component machining and grinding, only approved metalworking fluids can be used across the supply chain – and many aerospace manufacturers have specific standards for metalworking coolants.
Alongside this, the drive to adopt circular business practices to manage process fluids, sump maintenance, and utilize existing materials and products as long as possible is an increasing priority for original equipment manufacturers (OEMs) and their supply chains.
Challenges on the shop floor
For heavy-duty machining applications that are common across the aerospace supply chain, selecting highly effective metalworking soluble fluids and supply partners is crucial as these decisions can support manufacturers in keeping operations running smoothly, ensuring supply demands can be met while elevating levels of quality.
OEMs also face a significant challenge in finding a single adaptable solution for the diverse machining requirements and the specific materials used in the production process to fit their manufacturing supply chain. These requirements encompass milling, turning, drilling, and grinding, each presenting unique cooling and lubrication needs. Sticky residues, foaming issues during production, machine tool replacement costs, and high total cost of ownership are all issues that factory managers are dealing with on the shop floor.
To overcome these complex challenges, process fluid professionals work with OEMs to understand the intricacies of their processes and the materials machined and introduce solutions that uphold quality and performance across various applications. Specialized process fluids play a pivotal role in ensuring the high quality and reliability demanded by this industry. Essential for tool life, lubrication, and preventing corrosion/staining, process fluids are vital in enhancing the efficiency and precision of the manufacturing process.
Improving workplace safety and performance
Improving reliability and quality is crucial for minimizing coolant usage, reducing drag-out, and prolonging sump life to meet the demanding tolerances and intricate machining processes required. The industry is actively pursuing operational efficiency to reduce waste generation and realize substantial cost savings.
Aerospace manufacturers are starting to adopt a holistic approach to their metalworking process fluids, ensuring consistent quality and cost savings while optimizing operations. By carefully selecting and managing these fluids, manufacturers can enhance performance, minimize waste, prolong equipment lifespan, and prioritize the health and safety of their workforce.
This shift toward proactive safety measures is a testament to how aerospace manufacturers are not only protecting their workers’ wellbeing, it also reflects how they’re taking the lead in transforming the industry into a safer and more responsible one.
Opting for a single metalworking fluid over several specialized fluids is about more than maintaining standards. It’s about simplifying processes and inventory management and improving efficiency and cost-effectiveness. This grants aerospace manufacturers greater operational control, empowering them to steer their operations in their desired direction. Ultimately, this comprehensive approach enables high-quality, sustainable production while minimizing environmental impact and safeguarding the workforce.
Considering sustainability in process fluids
Adopting process fluids which can help contribute to corporate sustainability goals is crucial for enhancing environmental stewardship in the aerospace industry. A key focus for manufacturers operating in this sector is the reduction of waste streams and product consumption and increasing circularity within the manufacturing process.
Implementing process fluids such as HOCUT® 4260 offers a compelling strategy for manufacturers to reduce their environmental impact by prioritizing the reduction of waste and product consumption. Supporting manufacturers in making valuable contributions toward sustainability efforts, HOCUT 4260 – part of the Quaker Houghton soluble metal removal offering – is tailored to minimize environmental impact and improve circular economy practices by reducing consumption and waste generation. Its versatility also makes it suitable for multiple machining processes within the aerospace industry, reducing the need for multiple specialized fluids to be used.
To showcase this in application, an aerospace OEM using HOCUT 4260 in their Canadian machined parts facility reduced consumption and handling costs by $200k in 18 months, and reduced the volume of mixed fluids for disposal by around 250,000 liters annually. Production engineers stated that they have now minimized rework, and rejects are lower by 25%; they also reported no complaints about permanent residue on the machines.
Expertise at its best
To help manufacturers manage and optimize their industrial process fluids effectively, QH FLUID INTELLIGENCE™ provides a digitized solution for fluid management, enabling aerospace manufacturers to measure, control, and optimize their production processes and fostering safe, sustainable, and cost-effective operations. This integrated approach delivers differentiated value, enabling manufacturers to enhance performance, streamline operations, and achieve production goals efficiently.
To conclude, aerospace manufacturers have defined standards for metalworking coolants in order to maintain high performance and regulatory compliance. Working with a market leader in process fluids, such as Quaker Houghton, manufacturers can be confident that this industry expert supplier will have deep knowledge on the intricacies of their processes and introduce solutions that can adapt to different machining requirements. The combination of this expertise with the technical knowledge of OEMs is crucial to maintaining smooth operations and ensuring supply demands can be met while elevating quality and achieving sustainability goals.
Discover how Quaker Houghton is supporting manufacturers across the aerospace industry at: https://home.quakerhoughton.com/aerospace/
About the author: Jonathan Dilley has more than 32 years of industry experience and currently holds the Global Director of Aerospace & Defense position. In this role, he drives strategic initiatives and fosters important industry relationships. Jon started his career as a Service Engineer and progressively advanced through various roles, including Technical Sales Representative. While competing in other roles, Jon was a Global Strategic Account Manager for key aerospace accounts; his notable positions include Director of Sales & QH FLUIDCARE™ and Aerospace Business Development Manager for EMEA.
Latest from Aerospace Manufacturing and Design
- GE Aerospace secures Air Force engine contract
- Thomson Industries' online sizing and selection tool
- #53 - Manufacturing Matters - 2024 Leaders in Manufacturing Roundtable
- Join us for insights on one of the hottest topics in manufacturing!
- You can still register for March’s Manufacturing Lunch + Learn!
- Ohio creates Youngstown Innovation Hub for Aerospace and Defense
- Tormach’s Chip Conveyor Kit for the 1500MX CNC Mill
- How to Reduce First Article Inspection Creation Time by 70% to 90% with DISCUS Software