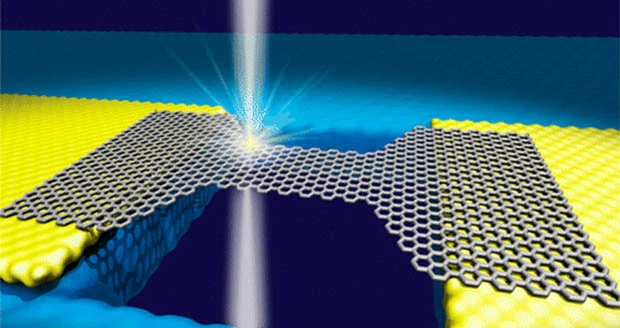
Graphene, a material that consists of a lattice of carbon atoms, one atom thick, is widely touted as being the most electrically conductive material ever studied. However, not all graphene is the same. With so few atoms comprising the entirety of the material, the arrangement of each one has an impact on its overall function.
Now, for the first time, researchers from the University of Pennsylvania have used a cutting-edge microscope to study the relationship between the atomic geometry of a ribbon of graphene and its electrical properties.
A deeper understanding of this relationship will be necessary for the design of graphene-based integrated circuits, computer chips, and other electronic devices.
The study was led by professors A.T. Charlie Johnson and Marija Drndic, both of the Department of Physics and Astronomy in Penn’s School of Arts & Sciences.
The team’s experiments were enabled by Brookhaven’s aberration-corrected transmission electron microscope, or AC-TEM. By focusing the microscope’s electron beam, the researchers were able to controllably cut sheets of graphene into ribbons with widths as small as 10nm, while keeping them connected to an electricity source outside the microscope. They then could use the AC-TEM’s nanoscopic resolution to distinguish between individual carbon atoms within those ribbons. This level of precision was necessary to determine how the carbon atoms on the edges of the nanoribbons were oriented.
“We’re relating the structure of the graphene – its atomic arrangement – to its electrical transport properties,” Drndic says.
“Graphene looks like chicken wire, and you can cut up this hexagonal lattice of carbon atoms in different ways, producing different shapes on the edge,” she explains. “But if you cut it one way, it might behave more like a metal, and, if you cut it another way, it could be more like a semiconductor.”
Because the graphene nanoribbons were connected to an electricity source while they were inside the AC-TEM, the researchers were able to simultaneously trace the outline of the ribbons and measure their conductivity. This allowed the two figures to be correlated.
After studying the nanoribbons with relatively low levels of electron flow, the researchers turned up the intensity, much like turning up a light bulb using a dimmer switch. The combination of the electron bombardment from the microscope and the large amount of electrons flowing through the nanoribbons caused their structures to gradually degrade.
As carbon bonds within the nanoribbons broke, they became thinner and the shape of their edges changed, providing additional data points.
“By doing everything within the microscope,” Rodríguez-Manzo states, “we can just follow this transformation to the end, measuring currents for the nanoribbons even when they get smaller than 1nm across. That’s five atoms wide.”
This kind of stress testing is critical to the future design of graphene electronics.
“We have to see how much current we can transport before these nanoribbons fall apart. Our data shows that this figure is high compared to copper,” Rodríguez-Manzo says.
The harsh conditions also caused some of the ribbons to fold up on themselves, producing nanoscopic graphene loops. Serendipitously, the team found that these loops had desirable properties.
“When the edges wrap around and form the loops we see,” Johnson explains, “it helps hold the structure together, and it makes the current density a thousand times higher than what is currently state of the art. That structure would be useful in making interconnects, which are the conducting paths that connect transistors together in integrated circuits.”
“Once we can cut these nanoribbons atom by atom,” Drndic says, “there will be a lot more we can achieve.”
University of Pennsylvania
Latest from Aerospace Manufacturing and Design
- Our first webinar of 2025 highlights additive manufacturing
- Pegasus Airlines orders up to 200 Boeing 737-10 airplanes
- ModuleWorks' 2024.12 software components
- Archer completes construction of high-volume manufacturing facility
- Curtiss-Wright’s NXP 16-Core Arm-based VPX single board computer
- Happy New Year
- 2024 Favorites: #1 Article –2024 Forecast
- 2024 Favorites: #1 News – Honeywell to expand Kansas aerospace manufacturing facility