
ALL PHOTOS COURTESY ADVANCED STRUCTURAL TECHNOLOGIES
Last November, I gave a presentation on advanced metal forming at Space Tech Expo Europe in Bremen, Germany. The title was Artful Engineering, and I talked about how metal spinning has evolved over the centuries from a manual process performed by skilled artisans to one that today is done almost entirely on CNC machinery.
I called it, “The intersection of metals and mechanics, of art and engineering science.” Because I was standing before a room filled with rocket enthusiasts, I also explained how spin forming and flow forming, together with their sister technology, rotary forging, are now the preferred methods for producing nose cones and injector rings, nozzle liners and extensions, chamber liners, diaphragms, fuel tanks, and other rocket components.
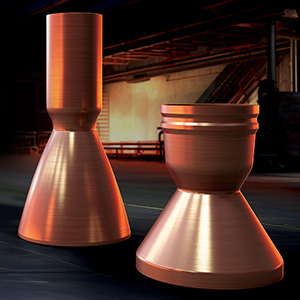
Spin-formed copper rocket components
possess a highly controlled and fine-grained
metallurgical structure, giving them
exceptional performance characteristics.
These mature processes have become the de facto standard for several reasons, chief among them being the ability to make seamless, single-piece, axially symmetric parts with a controlled flow, fine-grain metallurgical structure. We make many such components at AST, and if you want to learn the details, visit our blog.
Flying the flag
It might seem strange to suggest there’s anything artistic about a manufacturing process that delivers critical componentry to one of the most technically complex endeavors ever undertaken: space flight.
Soon after my return from Bremen, I had a conversation with a potential customer interested in our use of Industry 4.0 technology. For starters, he wanted to know how we use automation in the spinning process. He kept asking about artificial intelligence (AI), and why can't we install sensors in the machine, collect data, and then have the computer determine the optimal process parameters?
These are legitimate questions, and while we do have a new CNC spinning machine that will accommodate some of that Industrial Internet of Things (IIoT) technology, I eventually grew frustrated with the line of questioning. Mentally, at least, I said, “STOP!”
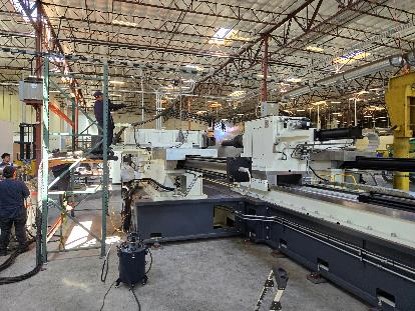
Engineering boasts a 500hp spindle,
advanced control technology, and the
ability to process parts up to 110" in
diameter and more than 200" in length.
I explained to him that advanced metal forming, whether a spin forming operation, flow forming, or even rotary forging operation, is like most manufacturing technologies – skilled people program and set up the machine, load the material, then keep an eye on the process and correct anything that needs adjustment. It’s an automated process, but not the way he was suggesting. Our production quantities of space components range from one or two to the high teens, much too low volume to worry about robotic loading and unloading. Yet.
As for AI, there isn’t nearly enough training data to even consider having it control any manufacturing process, especially given its reputation for “hallucinations” and drawing people with three arms and six-fingered hands. Maybe someday, but for now, I’ll put my money on human knowledge and experience.
Secret sauce? It’s not so secret
Yet humans are fallible. How, then, do we ensure accuracy and consistency in our manufactured space components and other products? Speaking for AST, I could go through the facilities list – CNC machinery, portable measuring arms, laser light scanners, advanced modeling software, and so on – but it wouldn’t be all that different than many machine shops, sheet metal houses, and other manufacturing firms. Simply put, we and others like us must have the tools needed to meet whatever comes our way and use them efficiently and cost-effectively. That’s the nature of manufacturing.
So, what are the differentiators? What's the secret sauce to successful spin- and flow-forming of space components, and how does one keep up with an industry that’s new and constantly evolving?
The OEMs in this high-flying market continually ask for lighter yet ever larger components. Many of these must be reusable and therefore expected to be exceedingly durable, with most made of exotic materials like tungsten and GRCop-42, to name a few. And due to the same budgetary concerns that exist elsewhere in manufacturing, the buyers typically expect these parts with shorter lead times at reasonable costs. Bluntly put, launching stuff into space can be damned demanding.
The key to meeting these various challenges comes down to some basic business best practices – namely, good planning, flexibility to meet the customer's needs, and a willingness to experiment. Let’s start with the latter.
Moving metal
Despite the past couple hundred years or so of metallurgical studies, forcing metal to move under extreme heat and pressure isn’t an exact science. Therein comes the requirement for experienced engineers and machine operators, who can make adjustments to the forming process in response to minor variations in the raw materials.
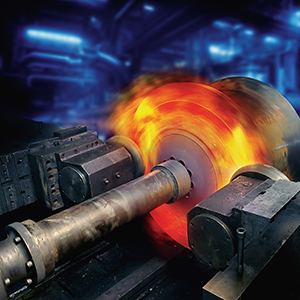
extreme heat and pressure might not be an
exact science, spin forming is both
predictable and flexible, producing parts with
unparalleled quality, performance, and
mechanical characteristics.
This situation is compounded by the fact that the space industry is quite dynamic – aside from a continuous barrage of novel shapes, sizes, and requirements, our customers routinely develop new alloys, or ask for new and more complex shapes, which must then be figured out as we go.
It's not a guessing game – far from it. We have simulation and modeling tools, most developed in-house, that we use to predict how materials will behave during the spinning process. But these alloys are also quite expensive, so it’s important to approach process development carefully, documenting each step and measuring the results. This also requires a great deal of collaboration with the customer to ensure their unique needs are met.
Try, try again
That also means a willingness to fail, learn from the experience, and try again. That’s the nature of manufacturing, but spin forming raises the bar even further. For one thing, many of the materials are not available off-the-shelf, making it necessary to work directly with the mill to specify a particular chemical composition, as well as heat treatment and other post-processing steps. As noted, spin formers must then develop a process to deliver the required geometry and mechanical characteristics, usually on a prototype basis, back and forth until everyone signs off.
That's the other part of the secret sauce: good planning. It’s necessary in any manufacturing environment, but when you’re working with forgings that might cost more than a new pickup truck, it’s crucial. Good planning also assures the customer the process is repeatable; because launches are becoming more frequent and the part they order today will come around again in a few months or even years, they can rest assured the quality will be the same.
Responsiveness and communication are similarly critical. Talk to your customers. Learn their key pain points and milestones. Explain to them where you are at all stages of the manufacturing process, starting with the quote all the way through to delivery of the finished product. There should never be any unanswered questions when you hang up the phone, nor any surprises later.
This last part is especially important when engaged in concurrent engineering. With spin forming, finished parts must not only comply with the geometric and tolerance specifications but also meet the customer's requirements for grain structure, flow, and mechanical properties, which can mean making multiple prototypes and test coupons until the optimal design is achieved.
Keep talking
Lastly, internal communication is equally important. This is somewhat easier with a small, knowledgeable group of people, but as everyone knows, skilled labor is in short supply, so it’s up to us as manufacturers to share what we know with the younger employees. Mentor them, whether they’re a machine operator, an engineering intern, or that newbie inspector you just hired.
Everyone in the company should be aware of customer needs and work toward the same milestones. Be a partner to your customers, but also work as a team, with everyone pulling in the same direction. Doing so is how manufacturers succeed, whether building hardware-grade widgets or mission-critical space components. That's the secret sauce.
About the author: Marshall Dormire is business and product development senior leader at Advanced Structural Technologies (AST)
Get curated news on YOUR industry.
Enter your email to receive our newsletters.Latest from Aerospace Manufacturing and Design
- AAMI project call submission deadline extended to May 12
- Jergens launches cast iron tooling column additions
- Airbus to acquire assets relating to its aircraft production from Spirit AeroSystems
- FANUC America's Cobot and Go web tool
- Chicago Innovation Days 2025: Shaping the future of manufacturing
- High-density DC/DC converters for mission-critical applications
- #59 - Manufacturing Matters: Additive manufacturing trends, innovations
- ACE at 150: A legacy of innovation and industry leadership