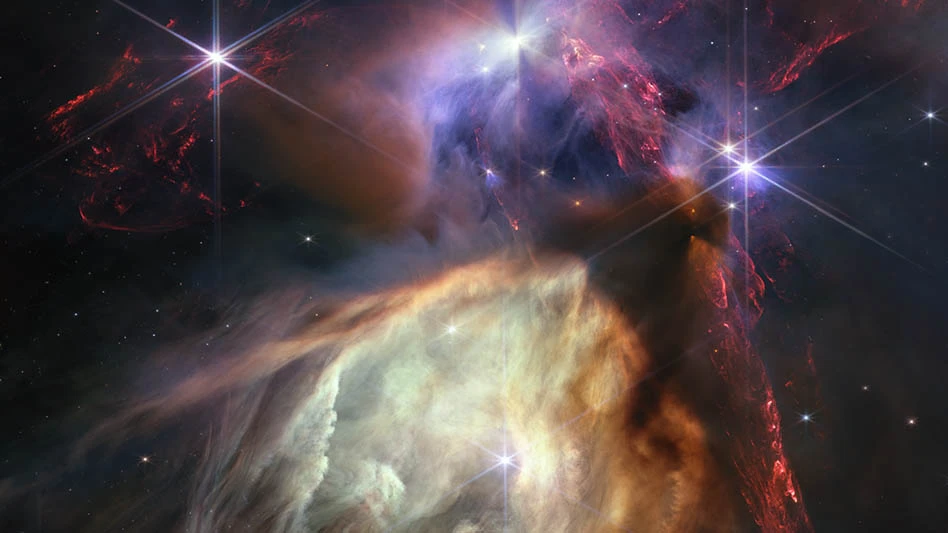
CREDIT: NASA, ESA, CSA, STScI
“Webb’s first year of science not only taught us new things about our universe, but it’s revealed the capabilities of the telescope to be greater than our expectations, meaning future discoveries will be even more amazing,” says Eric Smith, associate director for research in the Astrophysics Division at NASA Headquarters and a Webb program scientist.
“An engineering marvel built by the world’s leading scientists and engineers, Webb has given us a more intricate understanding of galaxies, stars, and the atmospheres of planets outside of our solar system than ever before,” adds Nicola Fox, associate administrator of NASA’s Science Mission Directorate in Washington.
Origins, challenges
The JWST – an international program led by NASA with its partners the European Space Agency (ESA) and the Canadian Space Agency – was conceived in 1988 as a follow-on to the Hubble Space Telescope. To see farther than Hubble, the new observatory, named for the NASA administrator who crafted the Apollo program and staunch supporter of space science, would have to use IR light. These wavelengths would enable the JWST to probe dust surrounding stars being born, stellar material too cold to be revealed in visible light, and galaxies so far away the light they emit has shifted below the visible spectrum.
Such a telescope required a lens more than 20ft (6.5m) across, and a sunshield the size of a tennis court to protect it from interfering heat sources that would overwhelm the faint IR signatures of distant stars. In operation, these structures are too large to fit atop any rocket, so they had to be designed to collapse into a compact structure that could be carried within the 18ft (5.5m) diameter payload fairing of the Ariane 5 launch vehicle. The lens and sunshield would have to survive launch, then unfold flawlessly to be reassembled in space.
Mirror

The JWST mirror collecting the IR light is composed of 18 hexagonal segments, each nearly 5ft (1.5m) across. On orbit, small motors carefully realign the segments into a honeycomb surface larger than any yet flown into space.
Northrop Grumman was the prime contractor for the JWST. In 2004, the contractor responsible for the mirror, Axsys Technologies, selected Mitsui Seiki to supply the machine tools needed to produce the JWST’s mirror segments.
The president of Mitsui Seiki USA at the time, Scott Walker, recalls the challenges of building eight Mitsui Seiki HS6A horizontal machining centers, with near-identical tolerances, to manufacture the mirror segments.
“The [machines’] axes are straight to 2µm, and the perpendicularity is within 3µm over 1m. This is remarkable for machines of this size.”
For comparison, 2µm (0.002mm) equals 0.00007874", about 1/50 the thickness of a human hair.
The 18 mirror segments would be machined from billets of cast beryllium – a light, stiff, strong, thermally stable metal with some toxicity – “and very difficult to polish into the perfect shape,” Walker says.
Each billet weighed 700 lb (318kg), reduced to 28 lb (13kg) by the end of 18 weeks of machining time. The mirror surface’s specified thickness was 0.098" ±0.003" (2.49mm ±0.076mm).
The 600 pockets cut into the back of each mirror panel featured eight different rib segments, 0.021" to 0.2" (0.53mm to 5mm) thick.
Tolerances for mirror finishing were +0.0002" (5µm).
Walker notes, “The contractor didn’t think it was achievable to build machines this size and reach such geometrical characteristics. We did something extraordinary.”
The experience had lessons for future Mitsui Seiki machines. “What we learned on those big horizontal 4-axis machines was how to build accurate, big 5-axis machines,” Walker says. “I don’t think we could have successfully built a big 1m or 2m trunnion machine, and 20µm in the cube, without doing those eight machines.”
Sunshield

Mike Menzel is the NASA mission systems engineer for the JWST at the Goddard Space Flight Center in Greenbelt, Maryland. He explains the challenges he and his team of engineers experienced making the JWST function in its IR sweet spot to see the dimmest things in the universe.
“We don’t want the telescope to glow brighter than the stars it’s looking at, so the telescope has to be cold – only 55°F above absolute zero or -361°F (-218°C),” Menzel says.
How do you get 3 metric tons of telescope to that temperature? The first part is putting it 1 million miles away from the Earth at Lagrange point 2 (L2), a place where the Earth, sun, and moon can be behind the spacecraft.
“We’ll build a big umbrella called the sunshield that’ll keep the telescope in the shade, and the telescope will naturally cool down to that temperature,” Menzel explains. The sunshield is illuminated by 200,000W of solar radiation, but it must only transmit 0.02W. “I tell people if it were suntan lotion, it would have a sun protection factor (SPF) of 10 million.”
The sunshield is about 21m x 15m (69ft x 49ft). And it must fit into an 18ft (5.5m) diameter launcher. The only way to do that is to fold it up.
“Folding up the sunshield was one of the banes of my existence, because now it has to unfold in orbit,” Menzel says. “When I started in this business in 1981, the very first thing I learned was never deploy anything in space. Something always goes wrong.”
Menzel admits to feeling stressed. “My colleagues are all standing around, thinking of how this thing needs to get out there, unfold, and work. And I’m thinking, I’m either going to have a job, or I’m not going to have a job or ever be able to get another one.”
During ground testing, every time the delicate sunshield was unfolded, it took about three months to fold it back up, requiring three-story tall cherry pickers to accomplish the repacking. The development program for the process took about three years.
The JWST required 50 of the most complex deployments ever attempted. Once the JWST reached space, the solar panel array deployed to start putting electrical power back into the batteries used during launch. After the JWST passed the moon’s orbit, two big panels which carry the folded-up sunshield were rotated. All the deployments were controlled from the ground and took 14 days.

“We released 107 actuators that allow roll-up covers to unfold the sunshield,” Menzel states. Complicating matters, the sunshield is composed of five individual layers of reflective material, made of specially coated Kapton. Individual pulley systems tighten up the layers into the correct trapezoidal shape. Each layer must be the correct distance from each other, and extend fully to properly isolate the telescope from stray IR radiation.
Next, the telescope’s secondary mirror must move into position, and the wings of the main mirror rotate from their stored position and lock in place.
“All the deployments went successfully: 344 single-point failure items all had to work correctly for this to happen,” Menzel says, grateful they all did.
The cool-down period went correctly, and the telescope was aligned. “We literally had to rebuild that telescope and realign it on-orbit. That has never been done before,” Menzel says.
By April 2022, all the instruments were working, and the first images were revealed in July.
“The first image I saw was a galaxy cluster about 4 billion light years from us. But so many objects in it are about 13 billion light years away,” Menzel recalls.
It took Hubble 14 days to gather the images to assemble a similar image. This JWST image required only 12 hours. After he saw that first image, Menzel knew he had a job for the next 20 years. He’s confident the JWST will be operational that long because the rocket put it exactly on target at L2. “We put 10 years of maneuvering fuel on it, but because we had such a great launch, the fuel will last for 20 years,” Menzel says proudly.
The telescope is working twice as good as it’s supposed to, Menzel says. “We’re supposed to be diffraction limited at a wavelength of 2µm. We’re currently diffraction limited at 1µm, meaning the total error on that telescope is only about 1µm divided by 14.”
Menzel adds, “Aside from the fact that astronomers love it, as an engineer, I like the JWST is already showing new and better ways to engineer new observatories.”
It’s a legacy that traces back to the challenges of the Hubble Space Telescope. “The methods used to diagnose the initial Hubble mirror focus problem are now the methods that enable us to rebuild a telescope on orbit and re-align it,” Menzel says. “The techniques used to correct that problem are now the techniques that enabled us to build a telescope on orbit that was bigger than the launcher that put it up there.”

Goals
What can the JWST accomplish? Menzel lists the project’s goals: “When this started, we had four science objectives. First, we want to see the first light that turned on in the universe, which we believe began about 13.7 billion years ago, right after the big bang. There was a dark period where there’s no light, but maybe about 400 million years after that, the first stars came and we want to see them.
“Next, we want to see how galaxies evolve through cosmic time. When you look at the galaxies very far away in the universe, they look like blobs. We want to see how those blobs evolve into spirals or other structures. We want to see how stars are born in our own Milky Way galaxy. And finally, we want to see how solar systems are born and how they evolve to make planets.”
NASA officials are also enthusiastic about what the JWST can offer.
“Thousands of engineers, scientists, and leaders poured their life’s passion into this mission, and their efforts will continue to improve our understanding of the origins of the universe – and our place in it,” says NASA Administrator Bill Nelson.
“With a year of science under our belts, we know exactly how powerful this telescope is, and have delivered a year of spectacular data and discoveries,” says Webb Senior Project Scientist Jane Rigby of the Goddard Space Flight Center. “We’ve selected an ambitious set of observations for year two that builds on everything we’ve learned so far. Webb’s science mission is just getting started – there’s so much more to come.”
Latest from Aerospace Manufacturing and Design
- Piasecki acquires Kaman's KARGO UAV program
- PI Americas’ long-travel XY piezo nanopositioners-scanners
- AAMI project call submission deadline extended to May 12
- Jergens launches cast iron tooling column additions
- Airbus to acquire assets relating to its aircraft production from Spirit AeroSystems
- FANUC America's Cobot and Go web tool
- Chicago Innovation Days 2025: Shaping the future of manufacturing
- High-density DC/DC converters for mission-critical applications