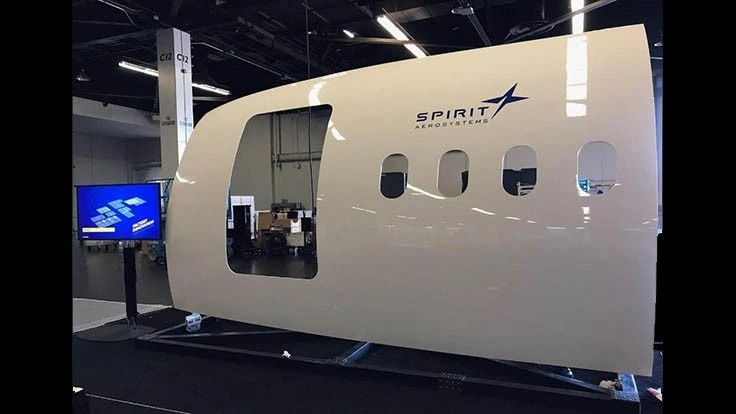
Spirit AeroSystems was recognized at the recent Composites and Advanced Materials Expo (CAMX) with the Award for Composite Excellence (ACE) in Manufacturing: Material and Process Innovation. Spirit received the award for its development of the Advanced Structures Technology and Revolutionary Architecture (ASTRA) demonstrator aircraft panel.
The ASTRA demonstrator is a full-scale composite fuselage skin panel that combines advanced manufacturing technologies and revolutionary architecture to cut roughly 30% of future composite fuselage costs. The National Institute for Aviation Research (NIAR) at Wichita State University (WSU) supported the development of this technology by completing hundreds of structural validation tests.
Spirit collaborated closely with Toray and A&P Technology on the project. The panel includes Toray's new high-performance composite material (T1100/3960) and A&P's new approach to braided composite fabrics (QISO). By combining these with Spirit's design-for-manufacturing capabilities, the ASTRA demonstrator reduces aircraft fuselage weight by roughly 5% – a massive improvement for aerospace.
"Spirit is a leader in materials industrialization and systems integration," said Spirit AeroSystems Vice President and Chief Engineer of Research and Technology Sean Black, Ph.D. "The ASTRA panel is an example of how we can take concepts and emerging materials into the manufacturing process, creating new solutions to meet high demands for quality and scale."
"It was an honor to accept this award on behalf of our team," said Spirit AeroSystems Senior Director of Research and Technology Eric Hein. "The ASTRA demonstrator showcases Spirit's expertise in industrializing new materials for aircraft structures."
The CAMX ACE awards are presented for a material or process that best contributes to efficient manufacturing and product sustainability. Entries demonstrate use of innovative materials, production techniques or methods that result in better quality, reduced production costs, increased production rates and volume, or reduced life cycle costs, and must also demonstrate its application in the manufacturing of a specific, end-use composites product.
Get curated news on YOUR industry.
Enter your email to receive our newsletters.Latest from Aerospace Manufacturing and Design
- Ohio creates Youngstown Innovation Hub for Aerospace and Defense
- Tormach’s Chip Conveyor Kit for the 1500MX CNC Mill
- How to Reduce First Article Inspection Creation Time by 70% to 90% with DISCUS Software
- Jackson Square Aviation orders 50 Airbus A320neo aircraft
- Beckhoff's motion control automation solutions
- #40 - Lunch & Learn with Fagor Automation
- Air Methods to purchase up to 28 Bell helicopters
- AMADA's laser marking capabilities