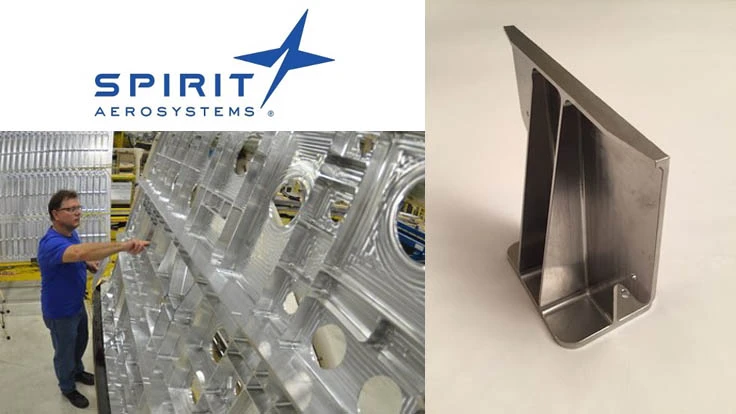
Spirit AeroSystems has created a 3- and 4-axis machining center of excellence (COE) at its McAlester, Oklahoma, facility in addition to creating a 5-axis machining COE at its headquarters in Wichita, Kansas.
The 5-axis COE at Wichita will specialize in large, complex aluminum and titanium parts for fuselage, pylon, and wing structures for commercial and military aircraft. It also will include expanded chemical processing capabilities for parts finishing and corrosion protection.
Spirit, already one of the world's largest fabricators of aerospace parts, has invested more than $30 million in the Wichita 5-axis COE, which now includes 120 machine tools. The Wichita center is to be fully operational later this year.
"We continue to invest in fabrication capabilities, and these expansions will help us better compete globally and remain leaders in the industry," said Spirit Senior Vice President of Operations Ron Rabe.
The McAlester COE will specialize in small- to medium-sized parts fabrication work in aerostructures. It also is expected to be fully operational later this year. More than 1,000 unique parts are in process of being scheduled for production.
The purchase and installation of new equipment in McAlester includes 18 new machines purchased from a fabrication shop in Juarez, Mexico.
"The McAlester center of excellence solidifies Spirit as a world leader in the fabrication of detailed parts for the aerospace industry," said Spirit President & CEO Tom Gentile. "Spirit has decades of experience doing this type of work for use internally. Now we can deliver that expertise to other customers around the globe."
Spirit's Oklahoma operations include facilities in McAlester and Tulsa.
Spirit's total fabrication capability spans more than 2.6 million square feet and produces more than 38,000 parts daily.
Spirit AeroSystems, Norsk Titanium to collaborate
Spirit AeroSystems and Norsk Titanium AS have entered into a commercial agreement to produce 3D-printed structural titanium components for the commercial aerospace industry. Norsk Titanium's proprietary plasma arc Rapid Plasma Deposition (RPD) technology will be used to build up the parts to a near-net shape, reducing waste, using less energy, and reducing product costs by up to 30%.
Spirit currently builds thousands of titanium parts for multiple customers around the globe and expects that at least 30% of them could be candidates for the RPD process.
Spirit’s Gentile said, "Reducing our material cost and our environmental impact is a win-win for Spirit, our customers, and the communities where we do business."
Spirit AeroSystems and Norsk Titanium have been working together to develop this technology for the aerospace industry since 2008. This commercial agreement between the two companies solidifies and extends the partnership and identifies specific parts that can be immediately produced using RPD.
"As the Spirit and Norsk Titanium relationship approaches its 10th year, we reflect on the value of this partnership and the significant milestones achieved during the transition from R&D to production," said Norsk Titanium CEO Warren Boley. "We recently announced becoming the world's first FAA-approved 3D-printed structural titanium provider and Spirit is the ideal Tier 1 aerostructures partner to leverage this pioneering capability."
Latest from Aerospace Manufacturing and Design
- Ulbrich Stainless Steels & Special Metals acquires two ATI operations
- Abaco Systems' SBC3215 high-performance, rugged single-board computer
- IMTS 2024 Booth Tour: Hurco
- Soracle to bring AAM services to Japan with Archer eVTOLs
- Veterans Day
- Carter Manufacturing's bearings for ultra-high vacuum applications
- IMTS 2024 Booth Tour: Greenleaf Corporation
- Register now for November’s Manufacturing Lunch + Learn!