
PHOTOS COURTESY ALL METALS & FORGE GROUP
In the aerospace industry, seamless rolled rings serve as critical components in jet engines, landing gear, structural components, and propulsion systems.
Precision-forged rings are often found where strength, heat resistance, and dimensional precision are paramount. Seamless rolled rings have a greater lifespan than other products due to their strength and durability, and are less prone to cracking or warping, making the option ideal for critical components requiring high tensile strength. Depending on the metal and alloy, the rings are also resistant to thermal and chemical damage, which further extends longevity while reducing the need for maintenance, repair, and replacement.
For jet engines, seamless rolled rings can be used in manufacturing components within jet engines, such as combustion chambers and turbine discs; in the propulsion systems of rockets and spacecraft; and for structural integrity and support in landing gear, wing attachments, fuselage sections, and other load-bearing elements.
For the aerospace industry, obtaining large seamless rolled rings in a timely manner remains a significant challenge, however. Currently, it may take many months to receive the forged components after placing an order. This delay can have a severe impact on the production and maintenance schedules of industrial firms that depend on replacement parts.
Rings are typically provided with a rough surface finish, which necessitates the use of CNC machining to achieve the required level of smoothness. This poses a challenge for machine shops with a high workload, as allocating machine time for finishing inevitably leads to a decrease in production speed and an increase in costs, ultimately impacting the end-use cost or profitability.
Fortunately, aerospace manufacturers can rely on forging specialists capable of producing large, custom, seamless rolled rings, and contoured seamless rolled rings with the required surface finish in under two months. One example, All Metals & Forge Group (AM&FG), an ISO 9001:2015 and AS9100D manufacturer of custom and standard open die forged parts and seamless rolled rings can usually deliver these components with the required finish within 8-to-10 weeks.
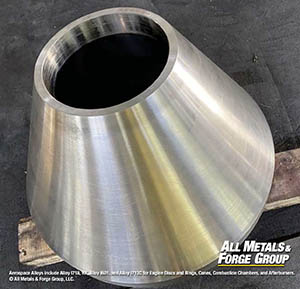
assure quality, performance, safety, and
compliance for the aerospace industry.
The range of forged products includes rings, discs, hubs, blocks, shafts (including step shafts or with flanges), sleeves, gear blanks, cylinders, flats, hexes, rounds, plates, and custom shapes. Carbon steel, alloy steel, stainless steel, nickel, titanium, and aluminum are among the materials used for forging. These forgings meet rigorous industry specifications such as ASTM, AMS, AISI, ASME, Boeing, SAE, GE, DIN, ASME B 16.5, ASME B16.47, and API 6A.
When speed and quality are essential, the aerospace industry can reap the advantages of an accelerated process for obtaining rolled rings.
The benefits of open die forging
One chief advantage of open die forging is the customization it offers in the forged parts and seamless rolled ring manufacturing process.
Open die forging is ideal for providing large, custom parts. As an example, AM&FG can produce seamless rolled rings or contoured rolled rings up to 200" in outside diameter, and custom forgings up to 40ft long or 80,000 lb. The company has been manufacturing and selling open die forgings and seamless rolled rings for more than 50 years.
While open die forging is typically associated with larger, simpler-shaped parts like bars or blanks, the process enables the creation of custom-designed metal components.
Open-die forging facilitates the production of seamless rolled rings to exact specifications with optimized mechanical properties and structural integrity. The rings can be produced in a variety of alloys, sizes, and shapes specific to the requirements. Forged parts finish-machined by machine shops are equally sound in structural integrity and required physical properties.
The forging of seamless or contoured rolled rings is also cost-effective since the process reduces material waste and manufacturing costs. Since the rings are constructed from a single metal piece using a specialized ring rolling machine, there is no need for welding or assembly, saving time and labor. The seamless rolled rings are also more structurally sound because they create a circular grain flow in the material, following the shape of the ring, which increases strength and integrity, creating a refined grain structure. This can enhance the material's fatigue resistance and overall performance, resulting in a stronger, more durable final product compared to other methods of ring making, such as cutting from plate or rolled and welded.
Near net shape parts with finer surface finish
Typically, when shafts or seamless rolled rings are forged, they are often left in an unprocessed state with a rough surface measured at approximately 500RMS. As a result, significant CNC machining time is required to achieve a smoother surface for the finished machined part. This poses a challenge for machine shops as the allocation of machining time for finishing these rough parts directly affects production efficiency, cost, and delivery time to the client.
To optimize efficiency and reduce costs, AM&FG frequently provides near-net-shaped forged parts with more refined surface finishes. Typically, the company provides a 250RMS surface finish. However, it can provide 125RMS, drill holes, and even do contour forgings as needed.
Some forge shops only offer a raw unmachined part. In contrast, AM&FG has already made the first rough cuts off the ring or forged parts.
In addition, the company conducts ultrasonic testing at no added expense to the customer to guarantee the absence of internal cracks, pits, or voids. This instills confidence in the quality of the parts, according to Tim Grady, Management Consultant for AM&FG.
“In many cases, AM&FG can offer ultrasonically tested parts that are more affordable than raw forged rings,” Grady says.
Streamlining delivery
In today’s market, procuring forged, seamless rolled rings can take from 20 weeks to as much as a year, as there are long lead times in receiving the necessary steel from mills.
“When replacement parts are required, a delay of a year or more isn’t acceptable,” Grady says. “Even 20-plus weeks is a serious issue.”
To expedite the process for customers, AM&FG has established strategic partnerships within the industry, enabling the company to deliver many custom forgings in a timeframe of 8 to 10 weeks. Furthermore, to minimize any potential production downtime for machine shops, the company strives to provide accurate quotes within 48 hours.
Positioning for the future
The need to acquire seamless rolled rings will only increase in industries requiring high-quality custom-forged components that can safely withstand extreme forces with minimal repair or replacement. In these cases, working with an expert forger who can expedite the process will convey a significant advantage.
About the author: Del Williams is a technical writer based in Torrance, California.
Latest from Aerospace Manufacturing and Design
- Trelleborg acquires Aero-Plastics
- Industrial automation products, enclosed encoders
- #61 - Manufacturing Matters: CMMC roll out: When do I need to comply?
- AIX shows aircraft interiors are a strategic priority for global airlines
- Machine Tool Builders Roundtable: Turn equipment into expertise
- No time to waste: How to machine MedTech parts more efficiently
- The 5 Best and Fastest Spindle Repair Services
- Mill smarter, not harder: How collaboration optimizes production