
Photo credit: Media Whalestock/iStockphoto, courtesy Cetec ERP
In aerospace and defense manufacturing, rigorous inventory tracking and traceability – from raw materials and components to subassemblies and final products – are essential for regulatory compliance and quality assurance. Each item must be traceable by a lot/batch or serial number, enabling manufacturers to address quality or safety issues quickly and effectively.
Supplied materials come with crucial documentation, such as Certificates of Conformance, original equipment manufacturer (OEM) documentation, lot codes, and heat codes. However, maintaining a centralized database for this information can be challenging, especially in fast-paced environments with limited resources and disparate systems.
It is especially important for aerospace and defense manufacturers to establish practical strategies and solutions for a robust traceability and document management system that seamlessly integrates with daily inventory management processes.
Material receipt and documentation
Inventory traceability begins when raw materials and components are received. Each receipt should be meticulously documented at the point of receipt to ensure that if a defect is discovered, the specific batch or part can be identified and isolated, preventing widespread failures. This level of traceability is vital to maintaining product safety, reliability, and meeting regulatory requirements from awarding bodies. It also aids in managing recalls and ensuring that only certified parts are used.
This begs the question: How can we quickly and effectively maintain receipt documents throughout the life cycle of all products?
Having a centralized information system, like ERP (enterprise resource planning) software, that can connect each lot or serial to each subassembly and final product in which it is consumed is crucial. This allows a material control employee to easily collect essential documentation and critical data at the point of receipt and track the use of this receipt later in the process using the unique receipt object as an internal identifier.
Advantages of adapting an ERP system:
1. Critical data collection: At receipt, the lot code (or heat or batch number) and date code is collected, along with serial numbers and expiration dates. The receipt centralizes materials tracking which makes data retrieval quick and accurate, minimizing manual entry errors. For example, recording a liquid coating’s lot code and expiration date upon receipt ensures it can be traced if issues arise later in the production process.
2. Effective document control: The material control employee can easily locate the receipt object to upload necessary documentation such as Certificates of Conformance (CoC) and OEM specifications. For instance, a specific alloy used in aerospace parts would come with CoC and OEM information, verifying it meets quality standards and allowing for future traceability.
3. Automated tracking solutions: Automated systems using barcoding and digital records reduce the risk of misplaced documents or manual entry errors. This ensures that all relevant data is accurately linked to each item from the outset.
In an ERP system designed for contract manufacturers in regulated industries, a Receipt object is created with a unique internal ID called a Receipt Code. Linked to this Receipt is the purchase order (PO) line and supplier information, the incoming inspections (and failures/non-conformance reports [NCRs]), and the attached documentation. Through the software, a barcoded Receipt label is automatically printed to attach to the received materials. This allows you to require a scan downstream in the process at put-away or picking/kitting, ensuring that lot code and associated data are linked to the work order.
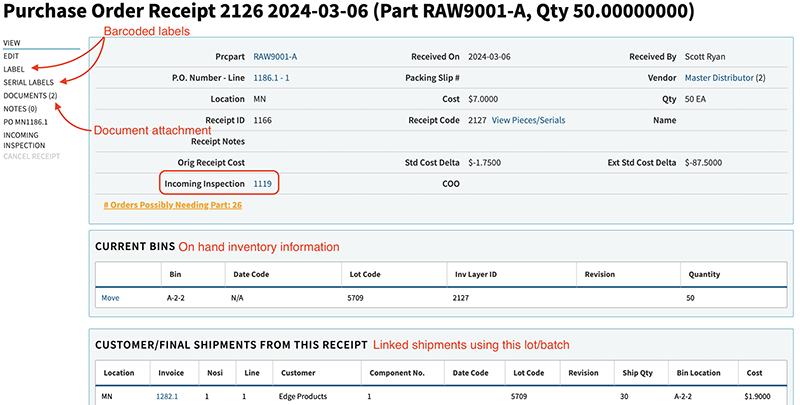
Reporting and data retrieval
Once information is stored in a centralized system, robust reporting capabilities are critical for maintaining compliance and supporting efficient inventory management. Accurate, up-to-date reports facilitate product recalls, quality assurance, and regulatory audits, and provide insights into inventory lifecycle, vendor reliability, and production quality.
Key traceability metrics include:
1. Receipt history: Provides quick access to lot codes, vendor information, and expiration dates, allowing for proactive quality checks. In the event of a recall, you can quickly search a lot code, pull up the documentation, and identify all associated work orders and final shipments for an auditor.
2. Work in progress (WIP) tracking: Enables monitoring of materials during production, helping to ensure that only compliant materials are used. This is particularly important when managing complex builds with multiple levels of subassemblies and suborders. It is important to see how a defect on a raw material lot code impacts your active, in-process work orders, and then adjust the schedule for the finished product accordingly.
3. Shipment history: Maintains comprehensive shipment records, aiding manufacturers in responding swiftly to customer inquiries or regulatory requests. This identifies every lot used in a shipment of final product, providing the top-down reporting.
A searchable database that’s connected to other manufacturing, warehouse, and quality control processes simplifies traceability, allowing users to locate any part or batch by querying lot numbers, part IDs, or vendor details. This enhances audit efficiency and confidence in regulatory compliance.
Preparing shipment documents
As products finish final inspection and are prepared for shipment, assembling and providing all relevant source traceability documentation is a requirement that can be time consuming. Gathered various documentation is often arduous and error prone. A centralized information system will automatically link all receipts to a final shipment, even traversing through multiple levels of assemblies for quick and easy preparation.
An example of what this could look like is Cetec ERP’s Traceability Document. For a finished product, this will show all Lot/Batch code data for each raw material through every level of the build, linking the raw material to the associated subassemblies. This doubles as both a customer-facing deliverable and as a tool to easily access each receipt object to print the associated documentation.

Leveraging a centralized information system makes the shipping process simpler with less room for error, allowing employees to access and print all shipping-critical documents at once. The software also ensures secure, accessible, and long-term storage of critical records, protecting them from potential loss or damage common with paper files.
Conclusion
Effective traceability and document management are crucial for maintaining compliance and quality in aerospace and defense manufacturing. By implementing a centralized system that tracks items from receipt through shipping, manufacturers can confidently meet industry standards while saving labor hours. These practices not only enhance traceability but also support operational integrity and provide peace of mind in a highly regulated field.
About the author: Scott Ryan is a senior consultant for Cetec ERP LLC. He can be reached at scott@cetecerp.com
Get curated news on YOUR industry.
Enter your email to receive our newsletters.Latest from Aerospace Manufacturing and Design
- Revitalizing the Defense Maritime Industrial Base with Blue Forge Alliance
- Safran Defense & Space opens US defense HQ
- Two miniature absolute encoders join US Digital’s lineup
- Lockheed Martin completes Orion for Artemis II
- Cylinder CMMs for complex symmetrical workpieces
- University of Oklahoma research fuels UAS development
- Motorized vision measuring system
- Everyone's talking tariffs