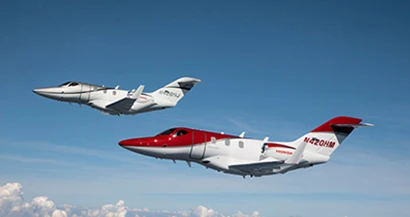
Officials from the Honda Aircraft Co. announce a number of achievements and significant milestones in the development of the HondaJet at the 2013 European Business Aviation Convention and Exhibition (EBACE) in Geneva, Switzerland.
"The HondaJet program is steadily approaching the final phase of flight testing, and manufacturing has transitioned to production of customer aircraft," says Michimasa Fujino, president and CEO of Honda Aircraft Co. "I am committed to bringing new value to aviation by introducing the HondaJet. At the same time, Honda Aircraft Co. continues to build the infrastructure and talent to design, manufacture, and service this revolutionary aircraft."
Testing and Certification
The HondaJet flight test fleet has been busy completing milestones and testing various systems. The program has flown approximately 3,300 test points for stability and control, aircraft performance, landing gear, flight controls, environmental controls, steering, braking, avionics and electrical systems. Below are a few of the highlights:
- Aerodynamics – The program has completed flight testing from stall to high speed dive. Stall testing included stall characteristics, stall speeds, handling qualities and performance. The flight test engineering team also recently conducted flutter testing at high and low altitude, and the aircraft flight envelope was expanded to the maximum dive speed (VD).
- Function and Reliability – On May 16, 2013, the program’s fifth FAA-conforming HondaJet achieved its first flight. This aircraft will be used for function and reliability (F&R) testing. F&R testing will simulate in-service flight operations of the aircraft. It has a production interior with standard lavatory and options including a side-facing seat, and will be used for interior and cabin systems tests. (Details of the fifth FAA-conforming aircraft’s first flight are included in a related release.)
- Environmental – In March, Honda Aircraft conducted cold weather testing in International Falls, Minn., to examine aircraft systems under extreme temperatures. Testing included windshield heat and anti-icing systems, mechanical systems operations, avionics functional checks, and electrical system testing. HondaJet wing anti-ice and nacelle inlet anti-ice tests were also conducted at the NASA Glenn Research Tunnel in Cleveland, Ohio. This remote testing augments hot weather testing conducted in Yuma, Ariz., last year, which included critical case tests for aircraft systems.
- Structural Testing – The test program successfully completed abnormal operation testing for the main entry door (MED) and emergency exit door (EED). These tests were conducted with the HondaJet program’s second structural ground test aircraft, which joined the program in October 2012. It is being used for both static testing and damage tolerance testing to analyze the durability of composite structures. This testing supplements the previously completed ultimate load, European Aviation Safety Agency (EASA) bird strike and component structural testing.
"Our team is working very hard to bring the HondaJet to market as quickly as possible,” Fujino says. “Customer and market expectations are high, and I am dedicated to certifying and delivering an aircraft that will bring our customers lasting joy. The more than 800 people working at Honda Aircraft Co. will continue to challenge and achieve milestones."
Manufacturing Transitioned to Production of Customer Aircraft
Honda Aircraft Co. manufacturing has fully transitioned to the production of customer aircraft. Collaboration between engineering, production control, supply chain, and manufacturing continues to fine-tune the processes and workflow necessary to achieve lean production and quality requirements for FAA Production Certificate (PC).
- Production Efficiencies– Manufacturing’s experience building the program’s test fleet has influenced best practices to more efficiently produce a high quality customer aircraft. A recent line balance project reduced the overall work footprint and created a more efficient workflow. Technology is also playing a vital role in HondaJet manufacturing. Handheld tablet devices will electronically deliver orders and visual work instructions to technicians on the assembly floor; an Automatic Guided Cart (AGC) will pick up and deliver parts to assembly areas; and an innovative, on-site paint mixing system will deliver a superior aesthetic quality while reducing the overall quantity of paint needed to finish aircraft.
Building Infrastructure to Support the otal HondaJet Ownership Experience
Construction continues on Honda Aircraft’s new customer service center to provide aftermarket support for the HondaJet in Greensboro, N.C. Once in service, the facility will complement the HondaJet dealer network, which includes three dealers in Europe and seven in North America. The facility will be complete in the fall of 2013. Honda Aircraft is targeting the end of 2013 for facility FAA certification as a Part 145 repair station.
Honda Aircraft Co. has invested in advanced technologies that fully integrate engineering, manufacturing, customer service and administration functions. The company’s extensive IT infrastructure underscores Honda Aircraft’s commitment to deliver superior customer service and support that is consistent with Honda’s reputation for quality.
For aircraft maintenance tracking, Honda Aircraft will be endorsing CAMP. The program will help HondaJet customers monitor aircraft service requirements including reviewing scheduled inspections, service, maintenance planning documents, and regulatory airworthiness directives. In addition, Quantum Control is being used to integrate inventory, accounting, service and other critical functions.
"The energy and excitement on our campus is building, especially in manufacturing where customer aircraft can be seen on the assembly line" says Fujino. "We are not only building a game changing product, but also building the industry’s best product support and customer service. Honda will continue to deepen our roots in aviation and create a higher standard for private aircraft ownership."
Latest from Aerospace Manufacturing and Design
- Boeing selects Collins Aerospace ejection seats for F-15EX
- Exxelia's mica capacitors
- Embraer clinches firm order from Japan’s ANA Group
- Fabrum and Sumitomo's expanded liquid hydrogen technology
- Siemens, U-M online course to drive metal AM adoption
- Seco’s Octomill 06 face milling cutter
- #51 - Manufacturing Matters - The Impact of M&A in MedTech 2024
- Discover an innovative technology for EMI/ESD/TVS suppression