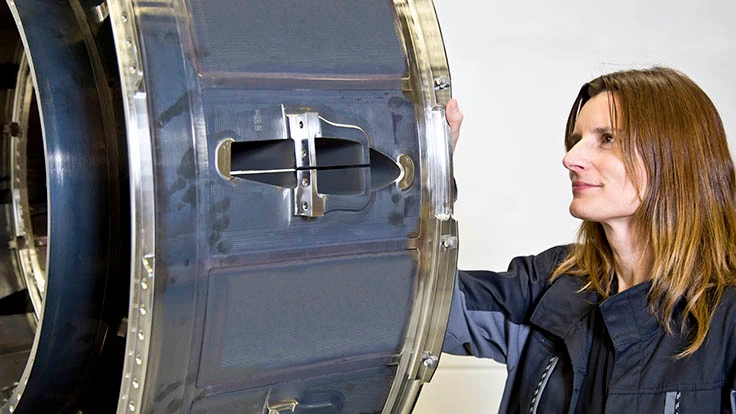
GKN Aerospace aft rotating frame for the SAGE 2 open rotor demonstrator, ready for delivery from the GKN Aerospace facility in Trollhättan, Sweden.
Redditch, U.K. – GKN Aerospace has delivered the two rotating frames for a major research program exploring open rotor aero-engine designs and with the goal of achieving a 20% reduction in fuel consumption and CO2 emissions.
The Open Rotor engine project is part of the Clean Sky Sustainable and Green Engines (SAGE) program, a 50% European Union-funded, multi-partner activity aimed at lowering fuel consumption and emissions through more efficient aero-engine architectures.
The company has delivered the front and aft rotating frames for the SAGE2 Open Rotor demonstrator engine to Snecma S.A. These rotating frames act as hubs for the two rows of propellers and are located in the propulsor module at the rear of the engine. In total the company will deliver 27 individual parts for these rotating frame modules. GKN Aerospace deliveries will be completed by the end of February in preparation for engine assembly and testing at the Snecma test center in Istre, France. The test program is scheduled to complete this year.
Henrik Runnemalm, vice president, Research and Technology at GKN Aerospace Engine Systems said: “The challenge with the design and manufacture of rotating frames lies in the fact that they have the geometric complexity of a traditional static turbine structure but, because they rotate and transfer torque to the propellers they are safety critical parts with quality requirements, stress concentrations, and load paths that are completely different to current static frame designs.”
Runnemalm continues: “We have applied a number of novel, precision manufacturing technologies – including new welding and machining techniques – to produce these structures and have evolved new non-destructive inspection methods which will inspect these complex geometries to the level required for critical rotating parts. Throughout this development program we have worked closely with the Swedish manufacturing technology center, (Produktionstekniskt Centrum - PTC), at Innovatum in Trollhättan as well as a number of smaller, highly specialized Swedish companies.”
Source: GKN Aerospace
Latest from Aerospace Manufacturing and Design
- 2024 Favorites: #9 Article – 5 tips for upskilling your aerospace machinists
- 2024 Favorites: #9 News – Siemens acquires Altair Engineering
- 2024 Favorites: #10 Article – How 3D-printed aviation parts can accelerate return to air
- 2024 Favorites: #10 News – Boom Supersonic completes Overture Superfactory
- OMIC R&D hosts Supporting Women in Manufacturing Day 2024
- 4D Technology's AccuFiz SWIR interferometer
- Seventh Lockheed Martin-built GPS III satellite launches
- KYOCERA AVX's CR Series high-power chip resistor