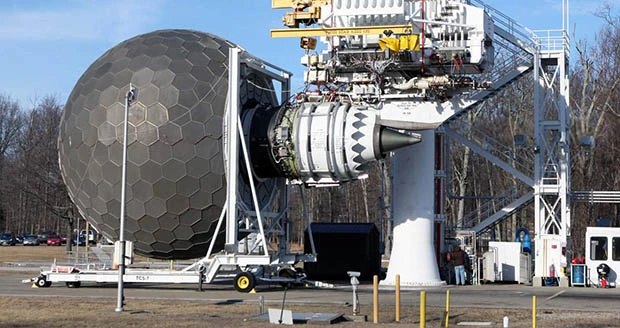
Peebles, Ohio – Ground testing is underway on a GEnx engine that contains lightweight, heat-resistant ceramic matrix composite (CMC) components in the high-pressure turbine (HPT) and combustor as part of the technology maturation program for the GE9X engine that will power the Boeing 777X.
“For the GE9X, GE is applying its extensive knowledge of CMCs into the engine’s hot section,” said Bill Millhaem, general manager of the GE90/GE9X engine programs. “The GEnx engine testing campaign, which began in late January, will allow us to demonstrate the functionality and durability of the full suite of CMC hot section components and help the team lock down the final design for the new GE9X engine by mid-2015.”
The GEnx engine on test at GE’s Peebles, Ohio, testing facility contains the following CMC components: inner and outer combustor liners, high-pressure turbine (HPT) stage 1 shrouds and stage 2 nozzles. CMC HPT stage 1 nozzles will be tested on the second build of this demo engine.
The engine is also testing non-CMC parts for the GE9X including the next-generation HPT stage 1 blades with advance cooling technology and the lightweight low-pressure turbine titanium-aluminide (TiAl) blades produced at Avio Aero, a GE Aviation business, using a new 3D additive manufacturing process.
The GEnx engine is undergoing extensive endurance cycles as part of the demo testing, with more than 350 endurance cycles completed to date.
CMCs are made of silicon carbide ceramic fibers and ceramic resin, manufactured through a highly sophisticated process and further enhanced with proprietary coatings. CMC components are ultra-lightweight with one-third the density of metal, providing weight reduction that enables better fuel efficiency. CMC material is more durable and allows engines to stay on wing longer. The material is also more heat-resistant than metals and requires 20% less cooling air, which improves overall engine efficiency.
CMC development is a key initiative at GE with GE Aviation and GE's Global Research Center pursuing CMC material applications for more than 20 years. GE Aviation’s Newark, Delaware, facility has mastered the manufacturing process for CMCs in its laboratory, and GE Aviation’s newly opened Asheville, North Carolina, facility will be the first involved in the mass production of CMC components.
GE and its partners will spend more than $500 million on technology maturation and product development for the new GE9X engine in 2015. Along with the CMC demo testing, this year’s technology maturation testing will include additional high-pressure compressor testing and the first demonstration core test.
Almost 700 GE9X engines have been ordered by customers since it was launched on the Boeing 777X aircraft last year.
The first engine will test in 2016 with flight-testing on GE’s flying testbed anticipated in 2017. Engine certification is scheduled for 2018.
IHI Corporation, Snecma and Techspace Aero (Safran), and MTU Aero Engines AG are participants in the GE9X engine program.
Source: GE Aviation
Latest from Aerospace Manufacturing and Design
- GKN Aerospace accelerates additive fabrication for fan case mount ring
- Expanded offering of internal coolant live tools
- #47 Lunch + Learn Podcast with INSACO
- Doncasters’ Groton expansion reaches major milestone
- Hardware-encrypted drive with trusted supply chain
- Titanium drop bottom furnace installation underway
- Solid carbide taps for demanding materials
- The Partner Companies acquires Precision Eforming