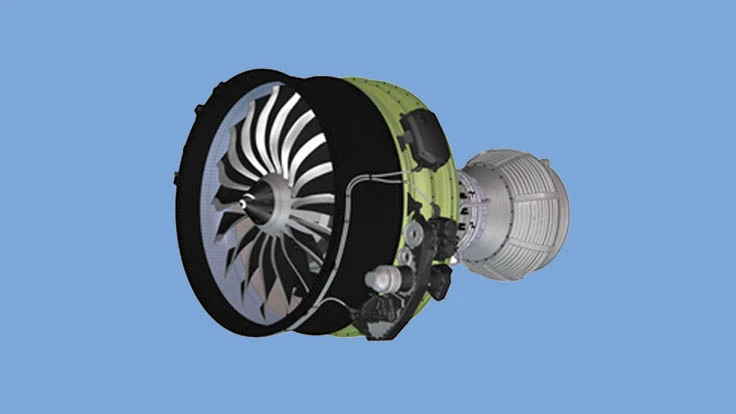
Huntsville, Alabama – GE Aviation is creating adjacent factories in Huntsville, Alabama, to mass-produce silicon carbide (SiC) materials used to manufacture ceramic matrix composite components (CMCs) for jet engines and land-based gas turbines.
GE Aviation will invest more than $200 million to construct two factories on 100 acres in Huntsville. When the factories are operational later this decade, they are expected to employ up to 300 people.
GE Aviation’s Sanjay Correa was joined by Gov. Robert J. Bentley and members of the Alabama delegation at the Alabama State Capital in Montgomery to make the announcement.
“Establishing the new GE factories in Alabama is a very significant step in developing the supply chain we need in order to produce CMC components in large volume,” said Correa, vice president, CMC program at GE Aviation.
One plant will produce silicon carbide (SiC) ceramic fiber. It will be the first such operation in the United States. Today, the only large-scale SiC ceramic fiber factory in the world is operated by NGS Advanced Fibers in Japan, which is a joint company of Nippon Carbon, GE, and Safran of France. The adjacent GE factory in Alabama will use the SiC ceramic fiber to produce the unidirectional CMC tape necessary to fabricate CMC components.
Construction of the two plants will begin in mid-2016, with full completion by the first half of 2018. Production begins in 2018. GE has already begun hiring the technical team that will transfer to the Huntsville operation. GE expects to begin hiring the hourly workforce in late 2016.
The use of lightweight, heat-resistant CMCs in the hot section of GE jet engines is a breakthrough for the jet propulsion industry. CMCs comprise SiC ceramic fibers in a SiC matrix, enhanced by proprietary coatings.
With one-third the density of metal alloys, these ultra-lightweight CMCs reduce the overall engine weight. Further, their high-temperature properties greatly enhance engine performance, durability, and fuel economy. CMCs are far more heat resistant than metal alloys, hence requiring less cooling air in the engine’s hot section. By using this air instead in the engine flow path, an engine runs more efficiently.
For more than 20 years, scientists at GE’s Global Research Centers and GE’s industrial businesses have worked to develop CMCs for commercial applications. The LEAP engine, being developed by CFM International, the 50/50 joint company of GE and Snecma (Safran) of France, is the first commercial jet engine to use CMCs in the high-pressure turbine section. The LEAP engine, with more than 9,500 orders and commitments, is currently completing certification testing. It is scheduled to enter airline service next year powering the Airbus A320neo, and in 2017 powering the Boeing 737 MAX.
Also, CMCs are being used in the combustor and high-pressure turbine section of the new GE9X engine under development for the Boeing 777X twin-aisle aircraft. GE is incorporating CMC components in advanced military engines including the GE3000 for the U.S. Army.
Ceramic Fiber Plant. Supported by funding ($21.9 million) from the U.S. Air Force Research Lab Title III Office, this plant will dramatically increase U.S. capability to produce SiC ceramic fiber capable of withstanding temperatures of 2400°F.
CMC Tape Operation. This adjacent plant, financed solely by GE, will apply proprietary coatings to the ceramic fiber and form them into a matrix to produce CMC tape. The ceramic tape will be used by GE Aviation at its new CMC manufacturing site in Asheville, N.C., which opened in 2014. The Asheville facility fabricates CMC shrouds for the LEAP engine’s high-pressure turbine section.
Since 2013, GE Aviation has also invested more than $100 million in a 300,000ft2 factory in Auburn, Alabama, where the company is engaged in jet engine component manufacturing (super-alloy machined parts) as well as establishing the world’s highest-volume additive manufacturing center.
Source: GE Aviation
Latest from Aerospace Manufacturing and Design
- Piasecki acquires Kaman's KARGO UAV program
- PI Americas’ long-travel XY piezo nanopositioners-scanners
- AAMI project call submission deadline extended to May 12
- Jergens launches cast iron tooling column additions
- Airbus to acquire assets relating to its aircraft production from Spirit AeroSystems
- FANUC America's Cobot and Go web tool
- Chicago Innovation Days 2025: Shaping the future of manufacturing
- High-density DC/DC converters for mission-critical applications