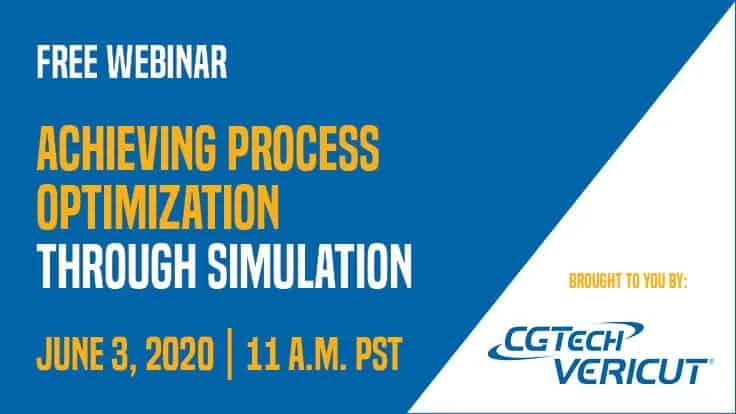
A digital twin involves 3-D representations of the part, workpiece being machined, fixturing, cutting tools and NC machine, along with machine kinematics and CNC control functionality. Integration improves digital twin accuracy to raise the bar for simulating, verifying, and optimizing NC programs. This unique and powerful environment enables operators to create collision-free NC programs that machine parts as fast as safely possible on their NC machines.
Process optimization goes beyond optimizing a single tool or program and links all machining operations together end-to-end to evaluate the entire manufacturing process. Using simulation software in this manner ensures NC programs are error-free, and that all operations work together as intended. This higher form of optimization is essential to any manufacturing environment where parts are machined through a series of setups (machining stages) or run across multiple CNC machines.
Process optimization ensures the entire manufacturing process flows seamlessly from one operation to the next – problems do not exist between setups, that all cutting tools are used as they were designed to be used, and all tools perform at optimal yet safe levels.
Learn the details during this free webinar.
Latest from Aerospace Manufacturing and Design
- Bell awarded funding for X-plane build phase of SPRINT program
- Shaft coupling clamps
- #46 Lunch + Learn Podcast with SMW Autoblok
- Gleason Corp. acquires the Intra Group of Companies
- Thread milling cutter reduces cutting pressure, vibration
- Malaysia Aviation Group orders 20 more Airbus A330neo widebodies
- More displacement from space-tested piezo actuators
- Textron Aviation to bring its largest-ever lineup to 2025 EAA AirVenture