
AdobeStock_460846705 | By ronnachaipark
Worker safety is a top priority in any aerospace manufacturing facility. Aerospace engineering and manufacturing is intense work with high exposure to numerous health hazards. Crafting an effective safety strategy requires arming your employees with the appropriate apparel and equipment. Keeping your employees safe means going beyond compliance and taking a proactive approach to preventing injuries.
Understanding the risks and hazards
Aerospace manufacturing is a high-risk industry, involving complex processes, heavy machinery, intense working conditions, and hazardous substances. Aerospace manufacturing requires extreme precision, as mistakes can prove dangerous or even deadly. Some of the most common work-related hazards faced by aerospace manufacturing workers include:
Hazardous substances – Aerospace engineers and manufacturers work with pressurized fluids, hot metals, flammable fuels, solvents, and airborne contaminants. These substances can cause severe burns if they make contact with skin. Metal, glass, fiberglass, plastic, and other materials used in grinding and blasting processes can cause eye, nose, throat, and skin irritation and even make their way into the bloodstream. Furthermore, particles released into the air during welding and grinding like manganese, hex-chrome, aluminum, and titanium can become combustible. When inhaled, toxic fumes can cause serious long term health problems like asthma and several types of cancer.
Heights and confined spaces – The size of the machinery involved in aerospace manufacturing often requires employees to reach overhead or work from dangerous heights. A fall from a significant height can cause permanent disability or death.
Repetitive motions – Repetitive motions can lead to overuse injuries in the lower back, neck, and shoulders. Repetitive motions can also lead to fatigue which can result in dangerous mistakes.
Electrical equipment – Electrical equipment presents the risk of burns and electric shocks. If manufacturing equipment and heavy machinery are not routinely inspected and maintained, a malfunction can prove disastrous. Faulty equipment can lead to crushing injuries, amputations, electrical burns, lacerations, and traumatic brain injury.
Key principles of worker safety
Promoting a safe work environment that protects workers and keeps operations moving requires a multifaceted approach.
Communication – To keep workers safe in a high-intensity work environment like aerospace manufacturing, communication is essential. Workers must know what is expected of them at all times and must be able to clearly communicate with one another in case of a problem. An open channel of communication also means that employees are empowered to report safety violations or mistakes that can be potentially harmful.
Training – Maintaining a safe work environment requires ongoing training. Safety training is not a one-time event but a continuous process for all employees.
Risk management – Managing risks means conducting regular risk assessments and equipping employees with the tools they need to do their jobs safely. Safety equipment includes personal protective equipment, headwear, goggles, gloves, footwear, and face shields, as well as proper clothing for the job.
Safety culture – Ultimately, your company must treat safety not as a box to be checked off but a central part of your company culture. Building a culture of safety begins with company leadership and extends to every level of the organization. When leaders display a disregard or disinterest in necessary safety measures, it’s the workers on the front lines (or assembly lines) who suffer the consequences.
The crucial role of safety apparel
In addition to proper training and policy enforcement, something as simple as workwear can make a difference in keeping aerospace workers safe on the job. Safety apparel – such as protective clothing, gloves, safety glasses, and hearing protection – serves as the first line of defense against workplace hazards. These items shield workers from physical injuries, chemical exposure, heat, cold, noise, and other occupational hazards encountered in aerospace manufacturing environments.
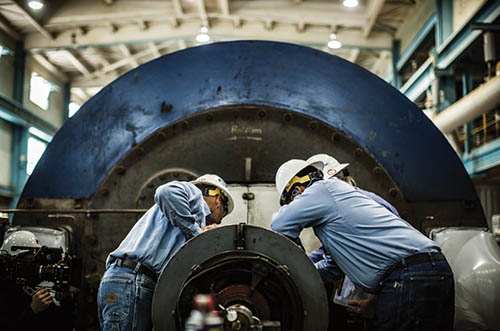
Wearing appropriate safety apparel can significantly reduce the risk of injuries and illnesses among aerospace workers. For example, wearing cut-resistant gloves can prevent lacerations during handling of sharp materials, while wearing respirators can protect against inhalation of harmful airborne contaminants.
In environments where cleanliness and contamination control are critical, such as in aerospace cleanrooms or facilities handling sensitive components, specialized safety apparel such as cleanroom suits and protective shoe covers help prevent contamination of products and equipment by dust, particles, and other contaminants carried on clothing or footwear.
Flame-resistant clothing, electrically insulated apparel and ESD (electrostatic discharge) clothing is essential for protecting workers from fire and electrical hazards present in aerospace manufacturing environments. Aerospace professionals can also wear clothing designed to stop the buildup of static electricity that can ignite flammable mixtures and damage electronic components.
Factors to consider in workwear selection
Selecting the right apparel for aerospace workwear involves careful consideration of several factors to ensure optimal protection, comfort, and compliance with industry regulations. To choose the right apparel for your workforce, assess the most significant risks at your worksite. What are the most common pain points and the most serious hazards? Choose workwear that provides protection against these.
Familiarize yourself with relevant safety regulations, standards, and industry guidelines governing personal protective equipment (PPE) in aerospace manufacturing. Ensure that the selected workwear meets or exceeds the requirements set forth by regulatory authorities such as OSHA (Occupational Safety and Health Administration), ANSI (American National Standards Institute), NFPA (National Fire Protection Association), and ASTM International.
Consider also the durability of materials, maintenance requirements, and comfort and mobility afforded by the work apparel you choose. Is visibility a concern (i.e. safety yellow)? Do your workers need flame retardant or insulated fabrics?
Challenges in selecting workwear
One of the biggest challenges in selecting workwear for industrial employees is the sheer volume of different options available. While it is important to select workwear that protects workers from the top hazards at your worksite, it can be difficult to identify and address all these factors at once. To encourage your workforce to adopt new apparel and wear it correctly, you must balance protection with comfort and mobility. And of course, there are cost concerns, regulatory compliance, and supplier availability to consider. Addressing these challenges requires a collaborative approach involving employers, safety managers, suppliers, and workers themselves. By carefully considering the unique requirements and constraints of the aerospace manufacturing environment, organizations can overcome these challenges and select workwear that effectively protects workers while promoting comfort, compliance, and productivity.
All Seasons Uniforms
https://www.allseasonsuniforms.com
About the author: Nick Warrick is the Sales Manager at All Seasons Uniforms. With more than 15 years of experience in the work uniform business, he has worked with over 100 clients across 20 different industries. Holding bachelor’s degrees in both Business Administration and Information Technology, Warrick revamped the company’s online presence, offering its customers a new uniform shopping experience.
Get curated news on YOUR industry.
Enter your email to receive our newsletters.Latest from Aerospace Manufacturing and Design
- NASA offers free high school engineering program this summer
- Pemamak's PEMA Vision 3D software
- Aerospace Industry Outlook - Spring 2025, presented by Richard Aboulafia
- Panama’s National Air and Naval Service selects Embraer Super Tucano
- Model 5770 Linear Abraser
- #42 Lunch + Learn Podcast - Quell Corp
- RECARO Aircraft Seating showcases advanced comfort solutions at AIX 2025
- Mitutoyo America’s MiSTAR 575 Shop Floor CNC CMM