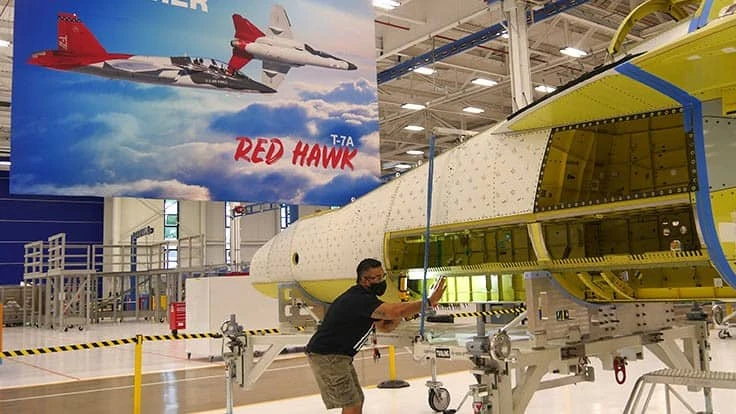
Randy Jackson/Boeing
The front fuselage of the first Boeing-Saab T-7A Red Hawk advanced trainer was joined perfectly with its aft section in less than 30 minutes – a testament to the digital heritage of the U.S. Air Force’s first eSeries aircraft and witness to the benefits of model-based engineering and 3D design.
The digital splice was completed in 95% less time than traditional splices and with substantial quality improvements.
“This moment marks a key stage in the evolution of the T-7A Red Hawk,” said Chuck Dabundo, vice president and program manager of Boeing T-7 programs. “Employing digitally advanced manufacturing and build techniques developed by Boeing over the past two decades, we are bringing this trainer to future pilots sooner than ever before possible and with greater quality.”
The aft fuselage was designed and built by Saab in Linköping, Sweden, under a joint development agreement with Boeing. After making the journey of more than 4,500 miles (7,200km) to St. Louis, the aft section was lined up perfectly to the forward fuselage by Boeing aircraft mechanics.
The aircraft, which will be used for static test, is the first engineering and manufacturing development test asset to be spliced. It will be followed by five engineering and manufacturing development jets as part of 351 T-7A Red Hawk trainers to be produced for the U.S. Air Force.
“What we’re seeing in this new evolution of digitally designed, engineered, and manufactured aircraft is a 50% improvement in overall production quality and as much as a 98% reduction in drilling defects,” said Andrew Stark, Boeing T-7A Red Hawk production director. “It’s a new way of producing airplanes with improved quality throughout the whole journey.”
Get curated news on YOUR industry.
Enter your email to receive our newsletters.Latest from Aerospace Manufacturing and Design
- GE Aerospace secures Air Force engine contract
- Thomson Industries' online sizing and selection tool
- #53 - Manufacturing Matters - 2024 Leaders in Manufacturing Roundtable
- Join us for insights on one of the hottest topics in manufacturing!
- You can still register for March’s Manufacturing Lunch + Learn!
- Ohio creates Youngstown Innovation Hub for Aerospace and Defense
- Tormach’s Chip Conveyor Kit for the 1500MX CNC Mill
- How to Reduce First Article Inspection Creation Time by 70% to 90% with DISCUS Software