
IMAGE COURTESY DMG MORI USA
From April 29 to May 2, 2025, DMG MORI USA unveils the latest advancements in machining and automation at this year’s Chicago Innovation Days 2025, hosted at the Chicago Solutions Center in Hoffman Estates, Illinois – a cutting-edge, 21,000 sq. ft. (2,000 sqm) test-cut center.
The event focuses on MX – Machining Transformation, a concept built on the pillars of Process Integration, Automation, Digital Transformation (DX) and Green Transformation (GX). By featuring 25 high-tech machines and automation solutions, DMG MORI will offer invaluable industry insights. Among the key highlights are exclusive machine premieres, including the NZ TRE, CTX beta 450 TC, Vertical Mate 85 2nd Generation, and the LASERTEC 30 SLM US – a groundbreaking additive manufacturing solution designed and assembled in the USA.
Live experience of groundbreaking solutions
Visitors to Chicago Innovation Days will experience live demonstrations of cutting-edge machining technologies, from 5-axis milling, turn-mill, to grinding and additive manufacturing. Additionally, visitors can explore a new DXchange area, a showcase highlighting DMG MORI’s latest digital solutions, including CELOS X, DMG MORI Connect, my DMG MORI, and more. Expert-led seminars will cover the latest industry trends and strategies for optimizing manufacturing processes with the daily focus topics Streamlining ROI with MX, Maintenance Management, Innovate & Transform with CELOS X, as well as an Education Day. A strong lineup of DMQP (DMG MORI Qualified Products) partners will also be present, demonstrating peripherals and complementary solutions that enhance manufacturing efficiency. As a total solutions provider, DMG MORI remains committed to supporting customers at every stage of their journey, ensuring long-term success through innovation and expertise.
NLX 2500 2nd Generation: Universal problem solver for all industries
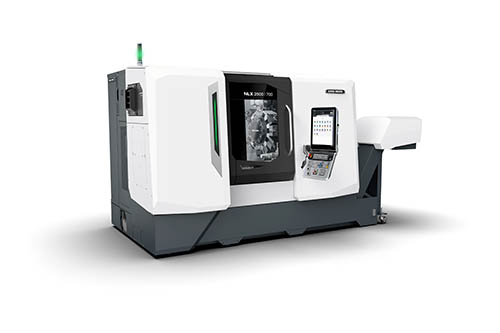
In an industrial world in which precision, efficiency and adaptability are fundamental prerequisites for long-term competitiveness, the NLX series from DMG MORI has proven itself as a universal problem solver and future-proof manufacturing partner. Whether in the automotive industry, in medical technology or in mechanical engineering: The NLX stands for a new era of universal turning in which stability, flexibility, and intelligent technology go hand in hand. The NLX 2500 2nd Generation, the heart of the series, will be presented by DMG MORI at the Innovation Days both as a stand-alone machine and with automation solutions.
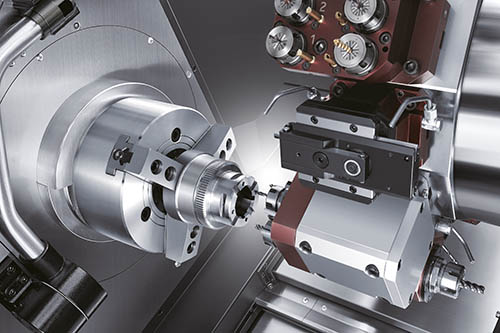
55mm box guideways, ball screws with double bearings and the reinforced machine bed ensure maximum rigidity. turnMASTER spindles with up to 1,273Nm on the left-hand side and 577Nm on the right-hand side allow a wide range of applications, including heavy-duty machining, while the highly dynamic BMT turret with up to 12,000rpm and 100Nm as well as a Y-axis ensure efficient complete machining. With a turning diameter of 366mm, a turning length up to 708mm and 105mm diameter bar capacity, the NLX 2500 2nd Generation allows machining of a wide variety of components.
An NLX 2500 2nd Generation without covers will give visitors to the Innovation Days an insight into the advanced components of the universal turning center. The direct comparison between the latest NLX model and its predecessor will be another highlight. The same machining demo on both generations will allow visitors to directly compare performance to the finished part.
US premiere: NZ TRE – production turning newly defined
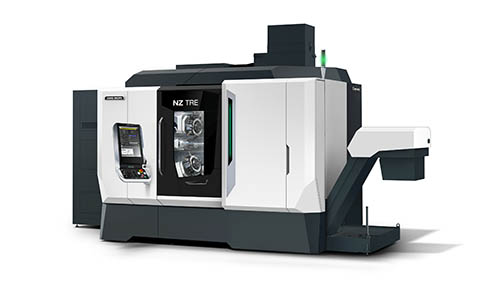
DMG MORI has incorporated decades of experience in production turning as well as the individual requirements of users into the development of the new NZ series. The result is a highly modular platform with two bed sizes that offers customers maximum flexibility and productivity: bar and chuck machining are part of the modular system, as is the option to install two, three – as in the case of the NZ TRE – or four units with B-axis and a TWIN spindle in the Z-axis. Additionally, DMG MORI offers several automation solutions for the NZ platform. Available in two bed sizes, the new NZ platform serves a wide range of components. The short version is designed for workpieces up to 740mm in length, while the long version accommodates components up to 1,290mm. Chuck machining is possible in both cases up to a diameter of 120mm, and for bar machining the passage is 65mm diameter. Including the 3.30m long bar feeder, the NZ requires only 17.8m² of floor space. Stability and precision in machining are ensured by the symmetrical architecture bed with high thermal stability and equal chip removal performance in all positions. On the control side, the NZ platform is equipped with a 19" DMG MORI SLIMline touch panel and FANUC 30iB.
US premiere: CTX beta 450 TC – future-proof 6-sided complete machining
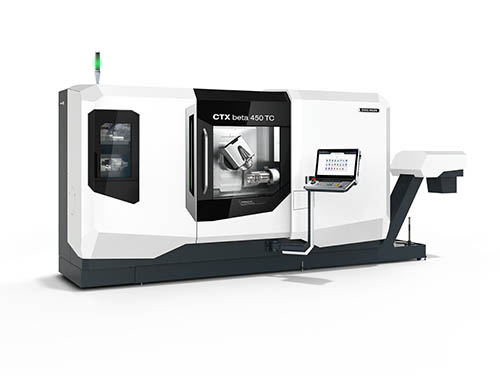
The CTX beta 450 TC stands for ease of use, efficiency, technology and flexible automation options, making the machine the ideal companion for production of the future. For example, the new control generation with CELOS X enables simple, app-based end-to-end workflows and offers the operator innovations such as OPWorkbench for easier and more structured NC programming. 5-axis simultaneous machining, 5-in-1 technology integration and 6-sided complete machining also ensure precision, flexibility and productivity. With a footprint of just 10m², the CTX beta 450 TC is the entry-level model in the CTX TC series. The work area offers space for workpieces with a diameter up to 400mm and a length up to 1,100mm. The bar capacity is 76mm diameter or optionally 102mm diameter for both the main and counter spindles. At the heart of the new model is the compactMASTER turn-mill spindle with a speed of 15,000rpm as standard and 20,000rpm as an option. The main and counter spindles achieve speeds of up to 5,000rpm and a maximum torque of 720Nm. The high performance of the CTX beta 450 TC is also reflected in rapid traverse speeds of up to 50m/min.
US premiere: Vertical Mate 85 2nd Generation – vertical multiprocess grinding with maximum accuracy
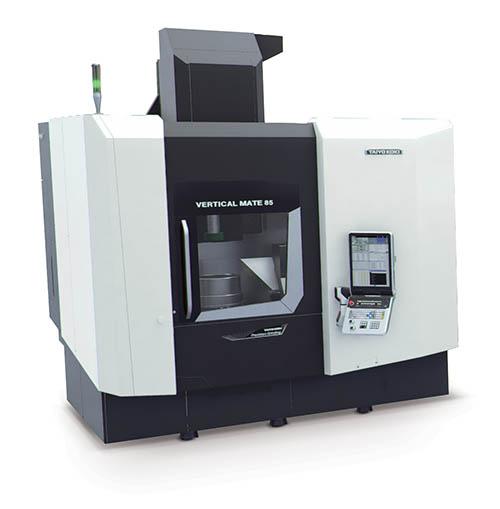
The new Vertical Mate 85 2nd Generation is the latest development in DMG MORI's portfolio of multiprocess grinding machines. Based on over 300 previous models sold and feedback from many customers from focus industries such as aerospace, automotive and semiconductor, the machine tool manufacturer has further optimized the versatile, successful model. The Vertical Mate 85 2nd Generation machines internal, external and end faces with a high-precision roundness of up to 1µm. The basis for this is a mechanical structure that has been further improved with the help of vibration tests and an FEM analysis. The machine now has a rear wall as standard, which contributes to a more stable structure and compensates for thermal influences.
In addition, the high precision is due to the heart of the machine – the speedMASTER LongNose spindle developed in-house. It has an output of 18.5kW, a torque of 35.3Nm and a speed of 10,000rpm.
LASERTEC 30 SLM US – designed for functionality and performance
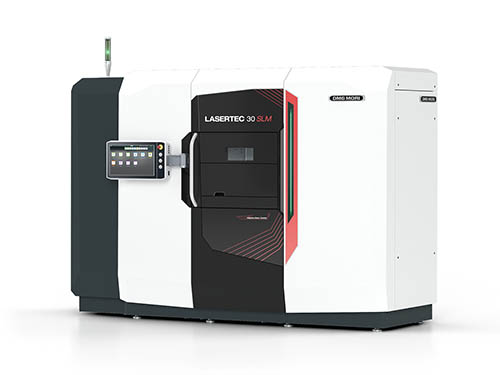
Additive manufacturing allows companies to reimagine the possibilities of metal manufacturing. The LASERTEC 30 SLM US from DMG MORI offers a powder bed machine that has been developed using principles honed over 100 years of machine tool production. The results are a 2-piece cast and machined core assembly for higher accuracy and stiffness, a linear scale encoder with 5nm resolution and a new high accuracy ball screw with high stiffness linear bearings. The build volume of 300mm x 300mm x 320mm and a layer thickness of 30µm allow for large and complex part production. A standard programable high-power 1,200W laser with beam shaping technology enables both high precision and high productivity. Innovative software features enable easy operation and advanced production capabilities. A feedforward control function called Adaptive Beam Control enable precise control of various laser properties ensure the highest quality parts produced for the most demanding applications.
Latest from Aerospace Manufacturing and Design
- AviLease orders up to 30 Boeing 737 MAX jets
- 256-piece general maintenance tool kit
- JetZero all-wing airplane demonstrator achieves milestones
- Cermet indexable inserts for medium turning operations
- Trelleborg acquires Aero-Plastics
- Industrial automation products, enclosed encoders
- #61 - Manufacturing Matters: CMMC roll out: When do I need to comply?
- AIX shows aircraft interiors are a strategic priority for global airlines