
Image credit: unsplash.com
In the aerospace industry, where precision and efficiency are of utmost importance, digital technologies such as Building Information Modeling (BIM) and digital twins are transforming facility design and operations. Using these technologies allows for enhanced visualization, simulation, and data-driven facility management.
BIM and digital twins enable aerospace facilities to optimize operations and streamline maintenance tasks. Through the integration of BIM and digital twins, aerospace facilities can not only achieve superior design accuracy but also anticipate and address operational and lifecycle challenges.
How BIM enhances the design process for aerospace facilities
In aerospace facility design, BIM offers specialized tools and functionalities that enhance each phase of the design process. BIM allows architects and engineers to simulate real-world conditions and assess design feasibility before any construction takes place. Below is a list of some aspects of BIM that propel facility management and design to the next level.
- Collision detection aids in preventing physical conflicts between electrical/mechanical systems during facility design. This critical feature prevents issues during construction before any building is done.
- Parametric modeling allows the designer to make changes to critical components without a subsequent remodel of elements upstream. Dependent components will update automatically.
- Quantitative analytics provide feedback related to energy usage by the facility and structural loading of various plant components. Simulating energy consumption, facility designers can make informed decisions on sustainable materials and systems to reduce environmental impacts.
- Data sharing and collaboration with BIM tools fosters synchronization of cross-functional teams. All members of the project management, engineering, and architectural teams will be able to collaborate on design decisions in real-time.
Benefits of integrating BIM and digital twins in aerospace projects
BIM is only the first part of the formula. The BIM will act as a reference point showing a relatively constant data stream to be viewed by the team. After construction, a digital twin can be created to represent a digital replica of the facility or project. Internet of Things (IoT) devices can be added to various facility components to track real-time data. Environmental data, energy usage, and operational data can all be tracked by the digital twin which allows for optimization of the facility.
BIM and digital twins were integrated into the infrastructure of Hong Kong’s International Airport. Alex Kwan, the then director of engineering and technology, spoke eagerly of the implementation of new technology solutions to create a Smart Airport. A digital twin of the airport facilities was created and actively monitors the operations of several facilities at the airport. Proper, more informed decision making as it relates to building function and general maintenance can be made through the collaborative environment of the digital twin.
Leveraging BIM and digital twins for predictive maintenance
Preventative maintenance is historically based on probability models and requires routine checks. This is a critical aspect of the aerospace industry ensuring the safety of aircraft users and preventing catastrophic failure. Integration of a digital twin introduces real-time monitoring of virtual replicas of the real-world systems to help predict these maintenance needs.
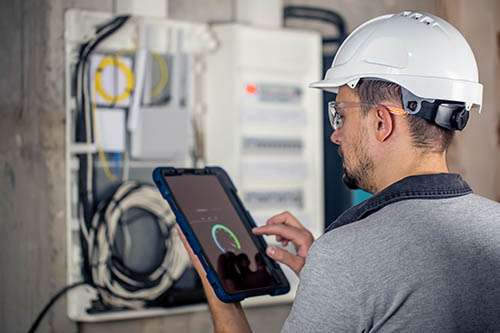
One intriguing example of this is from Rolls Royce, who created a digital twin of one of their engines. Engineers installed sensory equipment onto a real engine, which transmits data back to the digital twin. The digital twin operates in the virtual world the same way it does in the physical world. The digital twin receiving information from the in-service engine can flag potential issues, reducing the need for predictive models for preventative maintenance. This greatly increases the reliability of the engine and reduces the need for long down-times of the aircraft.
The future of BIM and digital twins in aerospace
Looking to the future, BIM and digital twins will enable fully connected, self-optimizing facilities. By combining BIM’s intuitive 3D modeling with the real-time predictive capabilities of digital twins, aerospace facilities will be capable of performing automated adjustments. For instance, through artificial intelligence (AI) integration with data collection via IoT sensors, digital twins will be able to identify and resolve performance deviations, reducing the need for manual intervention and enhancing the integrity of the facility. AI is also expected to further amplify the utilization of digital twins. It’s predicted that AI-powered digital twins will be able to more precisely analyze data patterns to aid in the detection of potential issues across an entire facility.
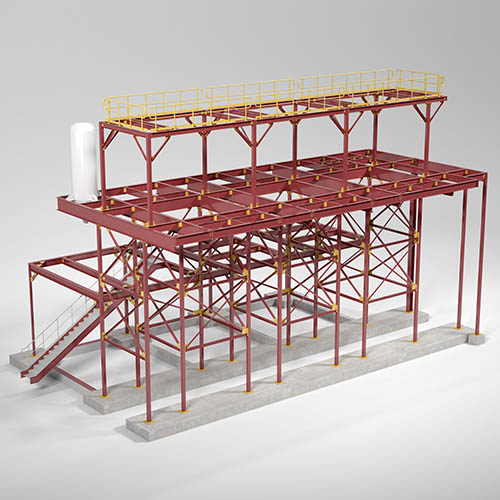
BIM and digital twins are also expected to drive sustainability in aerospace facility management and construction. As the aerospace industry faces increasing regulatory pressures to reduce its environmental impact, digital twins will offer more accurate data on resource usage and emissions. BIM’s advanced simulation tools will further support this front by enabling designers to test sustainable building materials and energy-efficient designs.
Digital twins are also beginning to reach for the stars by aiding in space-based engineering projects. Dr. Ricardo Sanfelice, professor and department chair of Electrical and Computer Engineering at UC Santa Cruze, is currently working on the development of digital twins that will aid in spacecraft maintenance and removal of space junk. Because spacecraft technology is expensive, using digital twins allows for the development of complex systems while reducing the number of physical prototype iterations.
About the author: Anna Liza Montenegro is the director of marketing forMicrosol Resources and a trained architect. She develops design technology conferences that Microsol Resources offers as a forum for architecture, engineering, and construction (AEC) professionals to exchange innovative strategies and best practices and facilitate discussions into the technology trends driving significant change in building design and construction. Microsol Resources is a value-added reseller of Autodesk, Bluebeam, Enscape, Rhino, V-Ray, CADLearning, and other technology partnerships.
Latest from Aerospace Manufacturing and Design
- Revitalizing the Defense Maritime Industrial Base with Blue Forge Alliance
- Safran Defense & Space opens US defense HQ
- Two miniature absolute encoders join US Digital’s lineup
- Lockheed Martin completes Orion for Artemis II
- Cylinder CMMs for complex symmetrical workpieces
- University of Oklahoma research fuels UAS development
- Motorized vision measuring system
- Everyone's talking tariffs