
PHOTO COURTESY TITAN ABRASIVE
If you were to ask someone to point out the difference between a blast room and a blast cabinet, it’s almost certain they would say, “The size.” And they wouldn’t be wrong.
After all, a blast room is literally a huge walk-in area where abrasive blasting is performed. The blast cabinet is a fraction of the size, with operators performing their work outside. Typically, one person is in the room, but if it’s on the larger size, two or three operators can be working together (but it’s got to be a really spacious room so they’re not blasting each other).
But size differential is only the top of the iceberg when it comes to the distinction between these two apparatuses. Though both are integral parts of any manufacturing process that involves finishing or coating, the decision of which one to use is not exactly a clear-cut choice. Let’s look at the most critical differences, both in physical properties and functionality.
1. Footprint
Accommodating a blast room can be a challenge, not only because of the size of the footprint but the potential obstructions (e.g., overhangs) that can make installation of a blast room difficult – or impossible. Conversely, a blast cabinet – even multiple cabinets – can not only be dropped almost anywhere, but they can also be easily moved to different locations within the plant as needed.
Blast rooms can be customized to just about any dimensions, but some of the more common standard sizes are:
- 10ft x 10ft x 10ft
- 10ft x 10ft x 15ft
- 15ft x 10ft x 25ft
A blast cabinet, by contrast, would be measured in inches. While there certainly are exceptions, a quick online scan shows a variety of cabinet sizes within a certain range:
- 36" x 42" x 48"
- 46" x 52" x 48"
- 48" x 36" x 40"; etc.
2. Modes of access
Operators do not physically enter a blast cabinet. Rather, parts are put in place through a swing door, after which operators work the internal blast controls by inserting their arms into the gloves attached to glove holes on the cabinet, viewing the part to be blasted through a view window, and turning the blast on and off using a foot pedal.
A standard size blast room typically has one personnel door, though larger rooms can have two or more. In addition, a blast room can have one entry/exit door, or it can have pass-through doors on either end, large enough to accommodate a forklift, vehicles, or very large assembly. Windows are optional, though most companies opt for at least one as a safety precaution (or more, based on their safety protocols).
3 Part size and quantity
A blast cabinet is the perfect vehicle for blasting smaller parts. Obviously, if a part is exceedingly large – like rail cars, commercial and military vehicles, construction equipment, and aircraft – the blast room is a necessity.
When blasting smaller parts in large quantities, it can be more convenient to lay them all out in a blast room, rather than putting a few at a time into the cabinet, removing them after completion, putting in the next batch of parts, and repeating the process over and over. There is no “magic number” of parts that would make a blast room a sound investment; it is an internal decision based on several factors, including operator availability and scheduling concerns.
4. Part weight
Because the blast room is exceedingly heavy, they require a solid foundation of at least 6" thick concrete. Consequently, they have a floor capable of supporting the blast room itself and parts that can weigh as much as 10 tons.
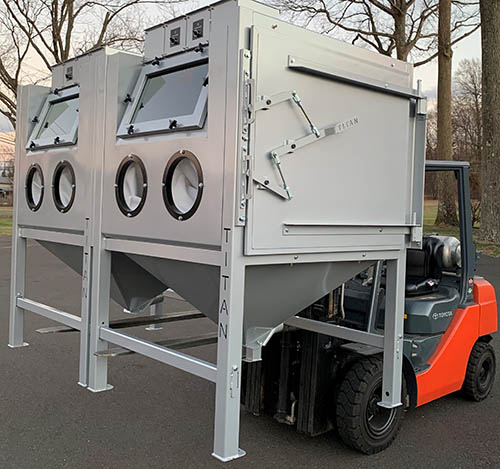
Standard blast cabinets can’t hold nearly the same weight. If you’re going to be blasting heavy parts (i.e., over 1,000 lb), you’ll likely need to provide structural support to the cabinet. What’s more, the weight of your parts may necessitate the addition of a turntable so that the part can be spun around inside the cabinet to ensure all surfaces get blasted. Sometimes, a track extension is required as well, essentially creating a small work cart on wheels. Operators can slide the turntable out of the cabinet through the swing doors (or through an optional vertical sliding door), drop the part onto the turntable with a forklift or manually, and slide the part back inside.
5 Ergonomics
In a blast room, a sizable percentage of the parts are brought in via forklift, truck, even crane; most do not require manual intervention. And when they do, the operator has freedom of movement, allowing use of optimal ergonomics (i.e., knees bent, straight back),
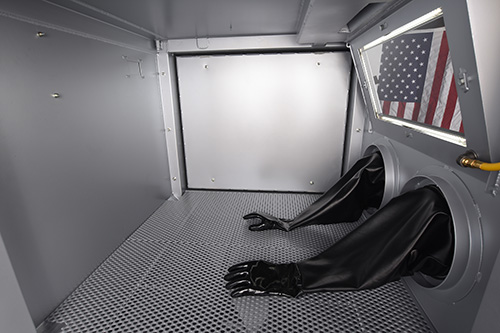
Blast cabinets present different issues. Using turntables and track extensions does facilitate getting parts into the cabinet. But even when parts are on a turntable (or just on the floor) operators often need to pick them up to ensure full blasting coverage. However, after a while, lifting or rotating parts in a blast cabinet can become quite taxing, even if they weigh just 2 lb or 3 lb each. That’s because it’s tough to generate arm strength with the operator’s arms being locked in at a fixed level. Further, since your back does not really come into play, your arms are the sole source of power.
6. Mixing blast media
Whether in a blast room or blast cabinet, if you want to use different types of blast media, you’ll need to clean everything out when switching from one media type to another. This includes the blasting equipment and recovery system (though the recovery system can be temporarily blocked off). And while the changeover and cleaning process for a blast cabinet is relatively quick, it can be tedious and time-consuming for a blast room.
This is not a huge concern for companies handling just their own parts. However, it can be a problem for job shops blasting a wide array of parts, requiring different types of abrasive media. For them, purchasing multiple blast cabinets is a logical investment (if the size of the part is small enough). Each cabinet can be dedicated to a specific abrasive material, eliminating switchover or contamination. They will still need a blast room for larger parts, but multiple blast cabinets ensures that numerous jobs using diverse blast media can keep humming along.
7. Fear factor
With blast cabinets, a person can walk up in regular clothes, stick their hands in the gloves, and start blasting – no safety equipment required. The scenario is quite different for a blast room, which requires operators enter this large, intimidating structure with full protective gear, including an air-fed helmet.
This becomes an even greater concern when safety departments get involved; the idea that the operator is physically in the room with this industrial blast equipment makes them worried – whether that worry is justified or not. The blast room takes on the appearance of an industrial haunted house.
8. Cost
While it’s difficult to determine an exact cost, blast rooms are almost always the more expensive purchase; expect to pay anywhere from $90,000 to $200,000, or much more, depending on size, type, and any customizations. Blast cabinets, as one would expect, are much less expensive than blast rooms, generally in the $35,000 to $55,000 range.
Sometimes, a company that doesn’t have the need (or the resources) for a full-blown blast room will buy a cabinet, then request modifications. This can be anything from a small bucket elevator reclaim system (rather than a vacuum system, to pick up heavier blast media) or turntables. Such changes can substantially drive up the cost of the blast cabinet – sometimes rivaling the cost of a blast room.
About the author: Brandon Acker is president of Titan Abrasive Systems, designers and manufacturers of blast rooms, blast cabinets, and abrasive blasting equipment. Follow Titan on LinkedIn at https://www.linkedin.com/company/titan-abrasive/.
Latest from Aerospace Manufacturing and Design
- Piasecki acquires Kaman's KARGO UAV program
- PI Americas’ long-travel XY piezo nanopositioners-scanners
- AAMI project call submission deadline extended to May 12
- Jergens launches cast iron tooling column additions
- Airbus to acquire assets relating to its aircraft production from Spirit AeroSystems
- FANUC America's Cobot and Go web tool
- Chicago Innovation Days 2025: Shaping the future of manufacturing
- High-density DC/DC converters for mission-critical applications