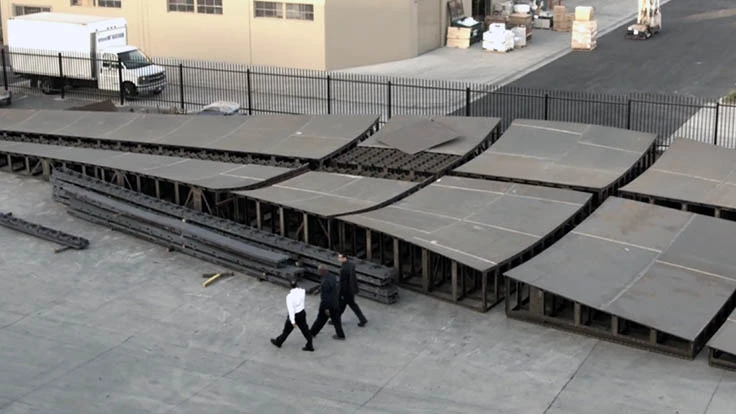
Santa Ana, California – Coast Composites LLC, an Ascent Aerospace company, has been contracted to produce a sixth set of wing skin molds for the Airbus A350 XWB. Following Coast Composites' delivery of the first set for the A350-1000 in May, Airbus announced the completion of the first production wings in August.
Ascent Tooling Group, comprised of Coast Composites and sister companies Odyssey Industries and Global Tooling Systems, also produced tooling for segments of the fuselage and nacelles – in total, more than 70% of the A350 XWB's outer surface – as well as the center wingbox and 100% of the stringers and frame.
Wing skin tool segments for the A350 XWB are manufactured of Invar, a specialty steel alloy selected to match the thermal expansion properties of the composite material used for the wing skin, and shipped to Airbus facilities in Spain and Germany, then assembled onsite. Ascent's traveling laser-welding robot minimizes the heat-affected zone and does not introduce high thermal loads into the structure. This eliminates distortion, shrinkage and, most importantly, the requirement for post-heat treating. The 32m (105ft) finished tool can be joined in a vacuum tight weld in a matter of hours.
Coast Composites also was awarded a contract by The Boeing Company to manufacture the largest-ever wing skin molds. Ascent will produce a set of lay-up tooling, consisting of four individual molds, to be used at Boeing’s new facility in Everett, Washington, to manufacture the 777X’s composite wing skins.
Coast Composites will manufacture the molds with its modular tool building system, based on the company’s patented laser welding technology and proven on previous wing skin mold builds. Tooling segments manufactured of Invar, small enough to transport on conventional roads, will be shipped to Everett then assembled onsite. After welding in Everett, the final wing skin tools will measure more than 110ft long and up to 21ft wide and weigh approximately 80,000 lb each.
According to Klaus Koester, vice president and general manager of Coast Composites, "Ascent's modular tool building system makes it possible to efficiently deliver the largest, highest quality tools in the industry to anywhere in the world." Coast Composites has developed a unique system for building extra-large Invar tools, based on the company's patented "deep penetration" laser welding technology.
According to Paul Walsh, president and COO of Ascent Tooling Group. “As aircraft evolve, our capabilities, designs and processes have advanced to meet new challenges. We developed our innovative modular tool building system to accommodate the ever-increasing size of aircraft tooling.”
Coast Composites has previously built 26 wing skin molds. The company’s core competencies center on metallic and composite lay-up molds and cure tools to produce airframe structures.
Ascent Aerospace is an AIP Aerospace company.
Source: AIP Aerospace
Latest from Aerospace Manufacturing and Design
- Ohio creates Youngstown Innovation Hub for Aerospace and Defense
- Tormach’s Chip Conveyor Kit for the 1500MX CNC Mill
- How to Reduce First Article Inspection Creation Time by 70% to 90% with DISCUS Software
- Jackson Square Aviation orders 50 Airbus A320neo aircraft
- Beckhoff's motion control automation solutions
- #40 - Lunch & Learn with Fagor Automation
- Air Methods to purchase up to 28 Bell helicopters
- AMADA's laser marking capabilities