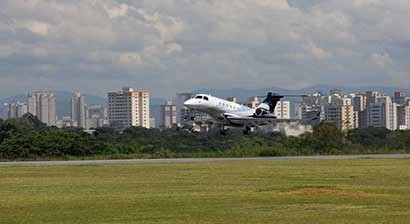
“With the first two prototypes already well into the flight test program, the first flight of the third Legacy 500 is a major milestone for the program,” says Ernest Edwards, President, Embraer Executive Jets. “The four-aircraft test program is designed to ensure all systems and features on the Legacy 500 reach maturity before entering service. The first and second prototypes already have logged 122 hours on 66 flights with testing proceeding as anticipated.”
Testing the interior to ensure a smooth EIS is key to the success of the program because it allows the company to test for failures and address problems before service entry, confirming the Company’s dedication to delivering an unmatched customer experience.
To that end, Embraer Executive Jets took the unusual step of producing an interior rig using an actual metallic fuselage equipped with the complete interior. The goal is to gain maturity in terms of assembly and to take managers and engineers on virtual flights between two and six hours to test comfort, reliability and durability. The interiors rig underwent rigorous testing of the seats, the galley as well as the lavatory. The company also had test results validated by outside labs.
The maturity campaign included more than 13,000 hours on the Legacy 500 Iron Bird since it entered service in 2010. The Iron Bird is used to test and re-test the aircraft at each development phase and integrates all systems including air management, avionics, power plant, electrical systems, flight controls, specific fly-by-wire control law tests, synoptics and CAS messages tests as well as failure mode case analysis tests.
In addition, during the maturity campaign each of the prototypes will have all maintenance reports uploaded into the Aircraft Health Analysis and Diagnosis (AHEAD) system which collects maintenance data for more efficient, thorough and easier maintenance planning. The computational, web-based maintenance platform is designed to ensure maximum readiness by limiting down time. Once in service with customers, AHEAD accelerates fault identification, allowing maintenance technicians to plan troubleshooting responses while the aircraft is still in flight.
Latest from Aerospace Manufacturing and Design
- US Dept. of Labor recognizes United Grinding as Apprenticeship Ambassador
- Optimal Engineering Systems' goniometers
- Breaking Free of the Additive Manufacturing Echo Chamber
- Don’t miss this month’s Manufacturing Lunch + Learn!
- marcus evans Aerospace & Defense Manufacturing and R&D Summit 2024
- How robots and cobots can work for you
- Why expertise in process fluid solutions is key to aerospace manufacturing performance
- Electra.aero to lead sustainable commercial airliner development