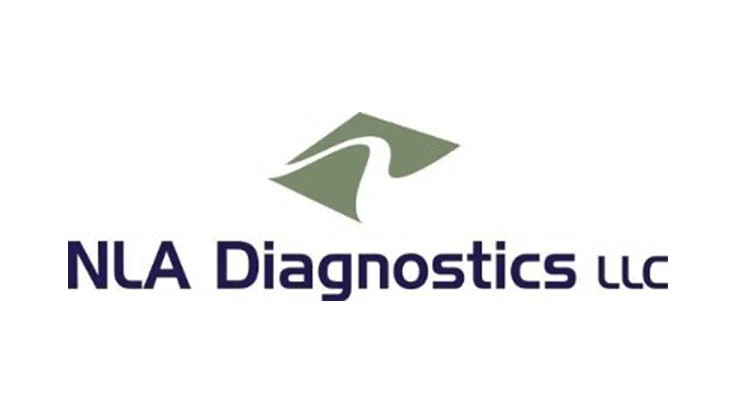
Charlotte, North Carolina – Aldo Bellotti, director of engineering at NLA Diagnostics LLC, will take the stage to discuss Impact Resonance Testing of Damaged Aerospace CFRP Materials and Structures at the upcoming CAMX 2015 (The Composites and Advanced Materials Expo). Decision-makers from aerospace and other industries will gather for the presentation on Thursday, Oct. 29 from 9:30 - 9:55 a.m. in room D171 at the Dallas Convention Center.
Bellotti's talk will focus on comparing impact resonance testing and results for two typical types of honeycomb composites: Nomex, the CFRP (carbon-fiber reinforced polymer) preferred for rotor blades on UH60 utility helicopters, and aluminum honeycomb composites used for commercial aircraft inner fixed structure (IFS) applications. Impact resonance testing is a non-destructive test method that makes gentle impacts on the material to detect damage. Bellotti will explain how testing from one side of the structure can also detect damage on the opposite side. Automatic analysis of the signal response and power spectra effectively differentiates between undamaged and damaged composite material.
NLA Diagnostics makes a unique, handheld instrument called the NLAD Cheetah designed for performing impact resonance technique on various forms of aerospace materials and structures at a rate of 10 taps per second. Testing can be performed at a fraction of the time needed for subjective, manual tap testing. Such technological efficiency means those responsible for keeping aircraft airborne can accurately and easily test for damage right in the field, minimizing downtime incurred in transporting plane and helicopter components for lab testing.
Bellotti's presentation is tailored for anyone whose job depends on understanding how aircraft control surfaces, wings, rotary blades, nacelles, radomes, turbine fan blades, and fuselages can be compromised by impact damage from bird strikes and other projectiles, fatigue, and thermal damage during service. Even though defects created by faulty manufacturing are often not identifiable by visual inspection, they can also be located and monitored with impact resonance testing to prevent failure.
NLA Diagnostics, a veteran-owned enterprise, was created to license and develop technology for the application of non-linear acoustic sound waves and resonance spectra analysis to identify stresses, defects and cracks in aircraft composite components and concrete. Its research and development unit, focused on accelerating the development of resonance technology and expanding its non-linear capabilities, was opened in 2010.
CAMX was created by ACMA (American Composites Manufacturers Organization) and SAMPE (Society for the Advancement of Material and Process Engineering) to connect communities devoted to advanced materials applications.
Source: NLA Diagnostics
Latest from Aerospace Manufacturing and Design
- Seventh Lockheed Martin-built GPS III satellite launches
- KYOCERA AVX's CR Series high-power chip resistor
- UT researchers receive Air Force grant for wind tunnel
- Monticont's linear voice coil servo motor
- FAA certifies Pratt & Whitney GTF engine to power the Airbus A321XLR
- Wevo's silicone gap filler
- Daher Learning Center inaugurated
- HEMCO Corporation's UniFlow CE AireStream fume hoods