
The aerospace industry is one of the most complex industries integrating information technology, robotics, measurement and control technology, and other areas. Materials, components, and systems within the manufacturing processes must withstand extreme conditions.
SCHUNK is your reliable partner in the aerospace industry, supporting aircraft design projects as well as research and development activities for the aerospace industry.
In the extreme conditions of the aerospace industry, structural components must meet the highest standards. These components form the backbone of aircraft and spacecraft and not only contribute to stability, but must also combine low weight and high strength. Continuous innovation in materials science enables the development of lightweight yet extremely durable structural components. These evolutionary advances are crucial for the efficiency, performance, and safety of aircraft and spacecraft.

Structural components make high demands on set-up, requiring costly and time-consuming adjustments. With controlled flexibility, the VERO-S Aviation drastically reduces the need of set-ups by enabling effective unclamping of the components.
Driving mechanism parts play a key role in the aerospace industry by influencing the performance and efficiency of aircraft. From turbine blades to high-temperature alloys, these components have to withstand the highest of loads. Advances in materials technology and precision manufacturing enable the development of engine parts that are not only lighter, but can also withstand extreme temperatures and pressures. Continuous innovation in this area is crucial to improving fuel efficiency, reducing emissions, and increasing the overall performance of aerospace engines.
For clamping sensitive components such as housing and turbine parts, we rely on deformation-low setup. This is how integrity during the machining process is ensured and the highest precision requirements are met, even for rotationally symmetrical components.

Landing gear components are of central importance in the aerospace industry, as they are essential for the safe landing and take-off of airplanes. These highly specialized components have to withstand extreme loads, from landing shock absorbers to brake systems. Thanks to continuous innovation in materials science and engineering, chassis parts are becoming lighter, more durable, and more efficient. Precision in design and production is crucial in order to meet the requirements for safety, weight reduction, and performance and make a significant contribution to the development of modern aerospace technologies.
When clamping the aircraft rims, we attach great importance to minimizing the risk of deformation. Deformation-free clamping using a 6-jaw chuck ensures precise machining and compliance with quality standards.

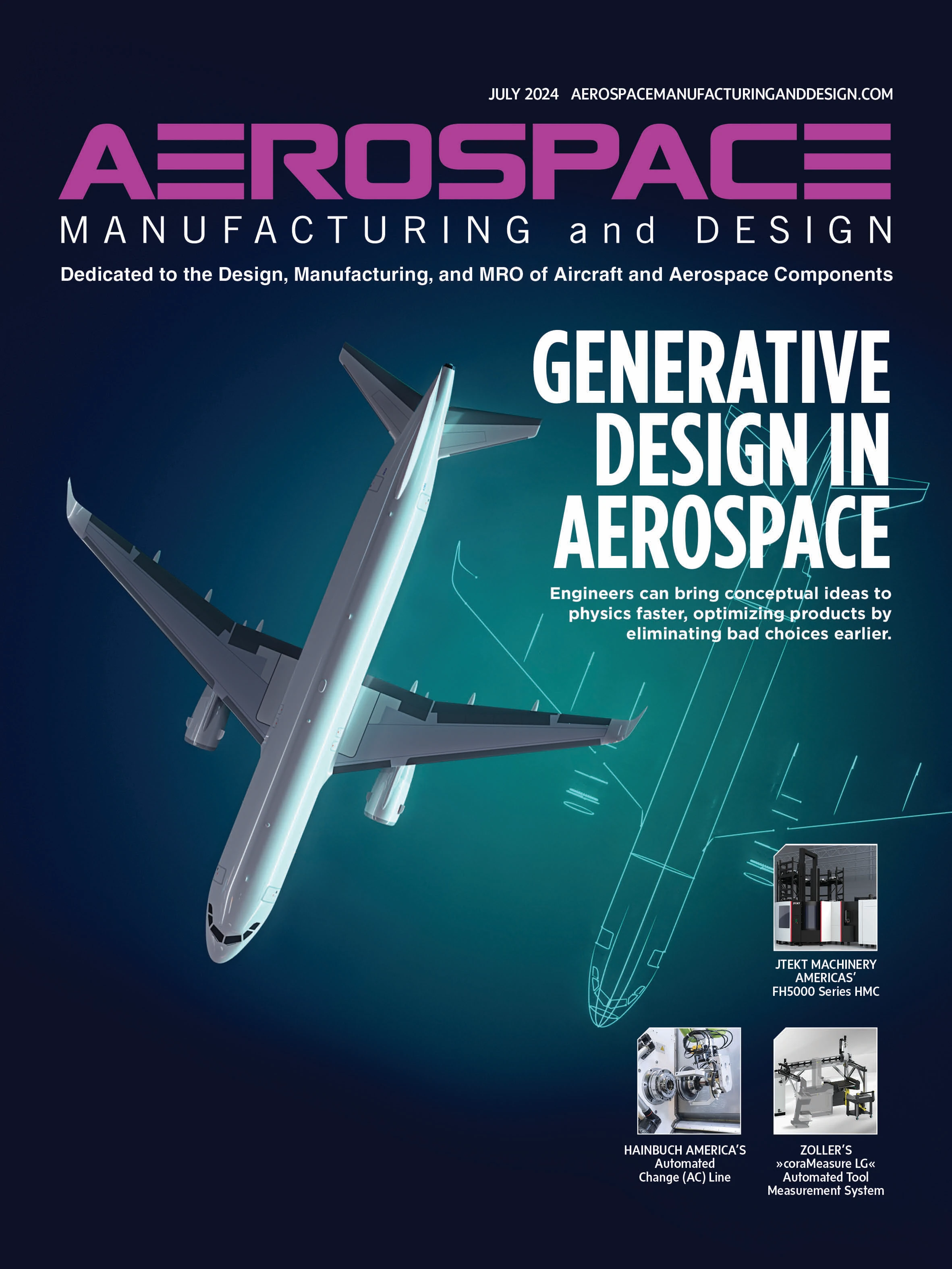
Explore the July 2024 Issue
Check out more from this issue and find your next story to read.
Latest from Aerospace Manufacturing and Design
- Talking machine tools with the professionals who build them
- Tools and strategies for improving your machining processes
- America Makes announces QTIME project call
- Innovation meets precision for 40% faster machining
- Upcoming webinar: Pro tips from a supply chain strategist
- Heart Aerospace relocates to Los Angeles
- Fixtureworks introduces Stablelock Clamps
- Piasecki acquires Kaman's KARGO UAV program