
Though 3D printing and metal additive manufacturing (AM) are remaking the manufacturing landscape, few equipment, material, or technology providers can claim full knowledge of the process. Sintavia, a Davie, Florida-based 3D metal printing company, is pioneering applications for the technology, and company executives are committing significant time, effort, and capital to better understand its many process parameters.
“There are thousands of metal AM machines in place globally with just as many people if not more still figuring the process out,” says Sintavia Chairman and CEO Brian Neff. “We’re making it a mission to work with our customers to develop optimal parameters for their builds. If you don’t understand and control the process, you won’t build what you want to build.”
Though estimates vary, researchers agree that the market is growing:
- Consulting firm IDC – global spending on desktop and industrial 3D printers hit about $11 billion in 2015 and is forecast to reach $27 billion by 2019
- MarketsandMarkets – 3D printing will experience a 30% compound annual growth rate (CAGR) and reach $30 billion by 2022
- PwC – 52% of manufacturers in 2016 expected 3D printing to be used in high-volume production in the next three to five years, up from 38% in 2014
Amidst such growth numbers, Sintavia is doing much more than promoting its 3D printing capabilities – it is positioning itself as a full-service, design-through-production provider. In addition to six high-speed powder-bed metal printing machines, Sintavia’s full metallurgical powder lab includes a hot isostatic press, thermal processing, CNC machining, EDM equipment, and destructive and non-destructive testing capability.
“Working with our customers to develop optimal parameters for builds demands nothing less than total process knowledge and understanding,” Neff says. “Sintavia is able to optimize parameters, serially manufacture, and audit quality much faster than any of our competitors.”
One tool the company leans on to support its understanding is the Ishikawa diagram of process parameters controlling outcomes of metal AM. Also known as a fishbone or herringbone diagram, the Ishikawa diagram delineates all relevant parameters that control a specific build. Because each cause can be a source of variation, the Ishikawa diagram is populated with hundreds of process variances that can affect part quality. Sintavia’s effort has evolved to cover such areas as the user, CAD data, part geometry, and work material in addition to the varied process sources of change, including laser adjustments, gas supply, and layer thickness.
Inspect and validate
Sintavia technicians understand the importance of inspection and process verification in quality control. Manufacturing standards are the highest in aviation, Neff says, driving the need for a quality-control process that is robust and repeatable to clearly demonstrate and improve part quality. It is essential to know whether voids or inclusions are present, how large they are (both individually and in total), and where they occur – and also whether the dimensions of the part conform to those of the design.
In such cases, X-ray computed tomography (micro CT) is a powerful answer, and Sintavia is taking delivery of its XTH 450 micro-focus CT system from Nikon Metrology in Brighton, Michigan. By converting 2D pixels to 3D voxels, supplying a full 3D density map of the samples, micro CT gives all this information in an easy-to-read visual format.
One large weld inspection

Using conventional manufacturing techniques, one would always inspect a weld for voids and inclusions. In metal additive layer manufacturing, the whole sample is essentially one large weld. With partially melted powder flying around in the printer during 3D-printing powder-bed fusion, the position and nature of defects is often totally random.
With traditional manufacturing processes, a few radiographs at specific orientations can suffice. But with additive layer manufacturing (ALM), the whole part needs to be inspected, particularly for aerospace parts with stringent tolerances. Inspection must include:
- Powder residues blocking channels
- Defects (voids & inclusions) –porosity, contamination, cracking
- Departure from the CAD model – dimensional analysis, wall thickness measurements, warping
Micro CT can determine the cooling and flow channels built in by the ALM process to an accuracy of 50µm to 100µm (depending on acquisition parameters). Micro-CT can find defects within samples down to a resolution given by the number of pixels across the detector. Given a sample 100mm across, and a detector 2,000 pixels across, the limiting resolution would be 50µm. Resolution is also limited by the focal spot size of the X-ray source, which may range from 80µm for high energies down to less than 1µm for low energies.
The size of sample that can be scanned with CT depends on the material it is made of and the energy of the X-ray source, measured in kilovolts (kV). Larger lower density samples can be scanned, as can smaller higher density samples.

Typical largest samples are:
- 225kV – aluminum piston heads; diesel injectors
- 450kV – aluminum cylinder heads; aircraft turbine blades
Part size also tends to be limited by the size of the detector and the penetrating power of the X-rays. This decreases as material density and atomic number of the material increases. More plastic can be penetrated than steel, and more steel than lead.
Benefits
Micro CT is now much faster and more suitable for production-line use and CT scanning of similar parts can be automated for loading and unloading. Scan times down to a few tens of seconds per part are possible. Users gain:
- Better insight into the inside of ALM parts
- Faster optimization of ALM prototyping, production processes
- Quality control, higher confidence in incoming, outgoing parts
- Reduced costs by avoiding destructive testing
Striving for total understanding in anything is the process of the scholar, the visionary, and the insightful. With the rewriting of the manufacturing rules book that 3D printing brings, X-ray CT is a powerful partner for non-destructively assuring geometrical and tolerance quality control.
Nikon Metrology
Sintavia LLC
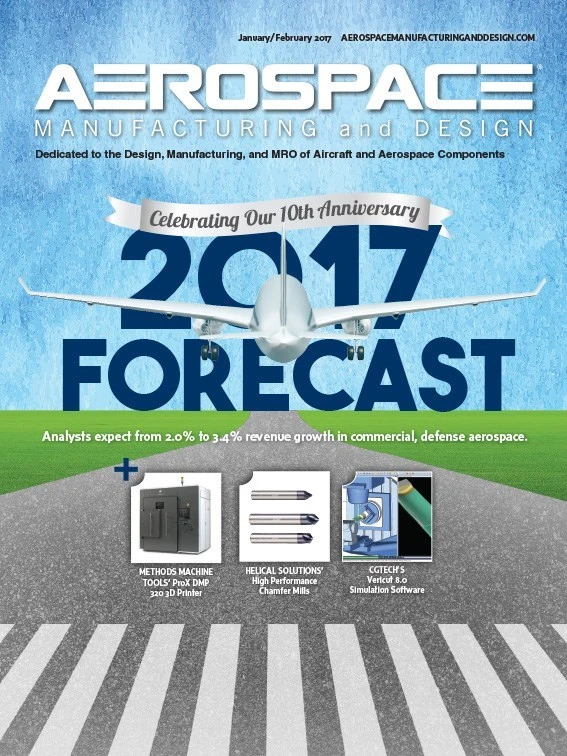
Explore the January February 2017 Issue
Check out more from this issue and find your next story to read.
Latest from Aerospace Manufacturing and Design
- 2024 Favorites: #10 Article – How 3D-printed aviation parts can accelerate return to air
- 2024 Favorites: #10 News – Boom Supersonic completes Overture Superfactory
- OMIC R&D hosts Supporting Women in Manufacturing Day 2024
- 4D Technology's AccuFiz SWIR interferometer
- Seventh Lockheed Martin-built GPS III satellite launches
- KYOCERA AVX's CR Series high-power chip resistor
- UT researchers receive Air Force grant for wind tunnel
- Monticont's linear voice coil servo motor