
The AgieCharmilles CUT F 350/600 series is designed for ease of use and flexibility. The series features the Uniqua control, ISPS and iWire functions, and RFID Smart Wire system along with design enhancements for thermal stabilization and fine laser correction for better precision.
The CUT F 350/600’s Uniqua human machine interface (HMI) delivers optimal functionality and ergonomics with a 19" vertical touchscreen, full keyboard, and mouse. For compatibility, Uniqua supports legacy file types from various EDM manufacturers, and with off-line and at-the-machine programming, ISO-based functionality, and object-oriented programming, Uniqua provides a powerful graphic tool with integrated CAM, ensuring compatibility with major CAD/CAM programs.
The iWire function automatically identifies and adapts wire speed to changing erosion height conditions during the wire-cutting EDM process. This eliminates wire breakage while reducing overall wire consumption per job, in some instances by as much as 29%. The iWire function works in tandem with the company’s Intelligent Spark Protection System (ISPS).
SparkTrack can recognize exactly where the sparks of wire-cutting EDM are happening during the process. Additionally, it can measure and identify the position of each spark along the length of an EDM’s wire. Knowing the exact location of the spark allows the system to optimize the cutting height, which automatically adapts the wire feed speed accordingly. Such capability reduces the chances of wire breakage during unattended operations when machining parts with steps and other features that vary the erosion height – the length of the actual surface areas where the wire is eroding/cutting.
Also available with the CUT F series machines is the SMART wire technology. This system reads wire characteristics through the radio frequency identification (RFID) chip on the spool as well as other traceability-related data.
For increased machine pitch accuracy, precision, reliability, and overall process stability, CUT F machines feature several enhanced design elements, one of which is thermal stabilization of axis optical encoders. The other design change is the incorporation of higher-grade ball screws for improved positioning accuracy and lifetime.
Radial pole magnetic chuck

The Radial Pole permanent electromagnetic system is used for vertical turning and grinding of thin-wall parts such as bearings, rings, gears, and flanges. The chuck can clamp workpieces with non-distortional clamping from the base surface when using three solid pole extensions and the remainder with spring-loaded pole extensions. There are no obstacles to the tool path for three sides of the part and no deformation occurs. Parts can be machined with extremely high accuracies of 10μm to 20μm, which can in many cases eliminate grinding.
Since users are holding the part for the base, setups are dramatically reduced. Pole extensions allow users to raise the piece from the magnet surface making the top, inner, and outer diameters fully machinable, reducing part distortion and allowing for more accurate part processing.
Mag AutoblokCeramic end mills

Cera-Cut end mills feature a high-hardness cutting ceramic head brazed to a carbide shank for optimal vibration dampening and longer tool life compared to one-piece ceramic tools. Featuring a high-feed duplex cutting-edge geometry, Cera-Cut produces high metal removal rates in challenging nickel-based alloys, resulting in machining parts 200% to 400% faster than conventional carbide end mills. Tool life of Cera-Cut is up to 5x higher than regular carbide end mills.
Cera-Cut end mills are designed for consistent cutting of high-temperature resistant materials such as Inconel, Hastelloy, and Nimonic as well as machining of hardened tool steels. Cera-Cut is also suitable for making interrupted cuts and offers a tight cutting diameter tolerance ranging from -0.0008" to -0.0016" (-20μm to -40μm), depending on the tool diameter.
Cera-Cut end mills can be used for roughing or pre-finishing, can produce 2D or 3D contours, and are suitable for face milling, slot milling, helical milling, contour milling, and pocket milling. Cera-Cut end mills are offered in diameters from 0.24" to 0.79" (6mm to 20mm). Corner radius, modular, and special designs are also available.
EMUGE-FRANKEN USA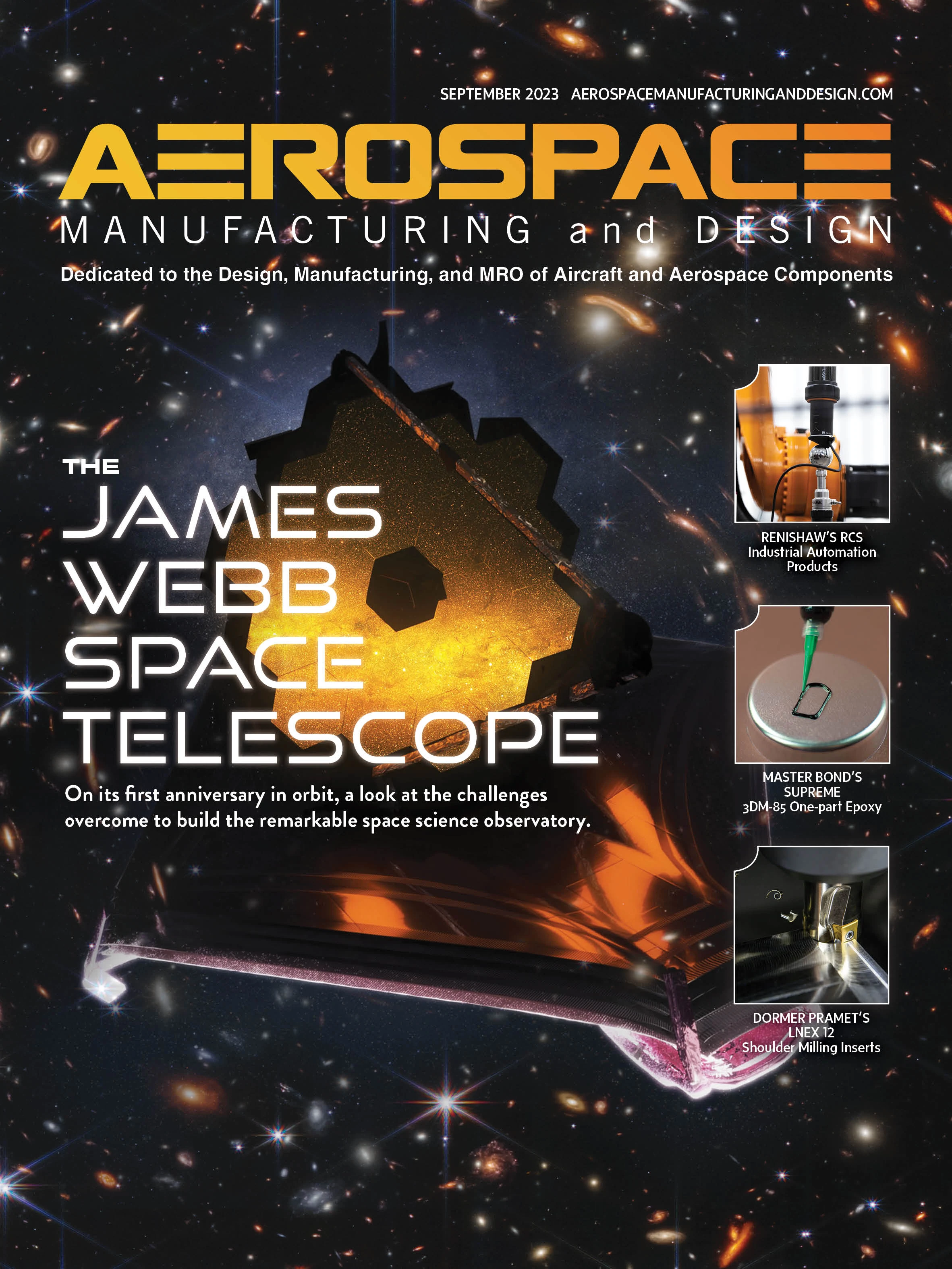
Explore the September 2023 Issue
Check out more from this issue and find your next story to read.
Latest from Aerospace Manufacturing and Design
- AAMI project call submission deadline extended to May 12
- Jergens launches cast iron tooling column additions
- Airbus to acquire assets relating to its aircraft production from Spirit AeroSystems
- FANUC America's Cobot and Go web tool
- Chicago Innovation Days 2025: Shaping the future of manufacturing
- High-density DC/DC converters for mission-critical applications
- #59 - Manufacturing Matters: Additive manufacturing trends, innovations
- ACE at 150: A legacy of innovation and industry leadership