
Manufacturers are under constant pressure to deliver prototype, production, and replacement parts at an ever-quickening pace, all while maintaining quality. Wire-based metal additive manufacturing (AM) technology can help manufacturers meet this challenge while:
- Reducing lead times from months to weeks
- Increasing design freedom, part consolidation
- Speeding prototype testing
- Light-weighting parts, lowering waste
Cleveland, Ohio-based Lincoln Electric, known for its arc-welding and cutting products and automated systems is at the forefront of AM, leveraging its in-house technology, materials, automation, and software to produce large, complex metal parts.
With a background in defense aerospace, Michael (Mike) S. Wangelin, business development and sales manager for Lincoln Electric Additive Solutions, who also represents Lincoln Electric subsidiary Baker Industries, Macomb, Michigan, spoke about innovations recently with Aerospace Manufacturing & Design (AM&D).
AM&D: What are the advances in wire-based AM?
Mike Wangelin (MW): Wire-based AM is basically taking an advanced gas metal arc welding (GMAW) power source, an industrial robot, and software that combines the robot’s motion with a multi-axis positioner to lay down successive weld beads to create a free-form 3D shape. It differs from metal powder-based AM in that the technology allows a larger build and is not limited to a build chamber. The only limitation is the movement of the robot or the cell used for the build. We’re currently working with a 4ft x 6ft x 6ft build volume and can expand that as needed. No special environment is needed, it’s just enclosed for fume collection with a localized shielding gas.
AM&D: What common industrial manufacturing challenges can AM solve?
MW: Prototyping in polymers or plastics can take a concept to a physical object in a short time, but it’s not representative of the actual part in strength or weight, so it’s limited to demonstration purposes, not functional testing. With our process, the strength would closely match or be the same as production. By initially prototyping with metal you can get to the point of what’s in production, whereas with polymers you’re limited to a conceptual object. Metal is a better match, closer to the end product.
AM&D: What replacement parts can you print on demand?
MW: Parts years out of production, often defined by paper 2D drawings, are difficult to reproduce in the current manufacturing environment. You can scan a part, capturing it digitally as an as-built object and recreate it quickly with 3D printing. Wire AM has greater surface variation than machined or cast surfaces – it’s near-net shape, so excess material may need to be removed from critical areas, but not necessarily entirely, saving time.
AM&D: What’s different about Lincoln Electric’s in-house technology?
MW: There are many 3D printing service providers in polymers and metal, many using off-the-shelf equipment and materials, so they’re limited to creating objects with what’s commercially available. What’s different about Lincoln Electric is that we’re in control of the entire process from start to finish, so we manufacture the power sources, welding equipment, and our own wire feedstock. Lincoln Electric has decades of experience in advanced automation and also owns and develops the software that takes the 3D model, creates the building routine, and controls the robot and positioner. Every piece, from startup design to completion of the product, is within Lincoln Electric’s control. Having the power of the large Lincoln corporation, we’re able to invest in each advanced technology segment along the way, driving the whole process.

AM&D: What software has been developed?
MW: One key piece of establishing the 3D-printing solutions group within Lincoln Electric was having the software that sliced the 3D model to prepare it for 3D printing, generate the deposition tool path, and control the system. So, the company has taken software initially developed for complex 5-axis NC machining and adapted it to AM, a product called SculptPrintTM. Having the software owned by Lincoln Electric offers us the advantage to constantly make changes to the software as we learn about the process and gain efficiencies with it, so there’s no delay between identifying issues and making changes, where with third-party software, you’re running behind in making those advancements.
AM&D: What materials are you using?
MW: We’re currently printing steel, high-strength low-alloy steel, stainless steel, Inconel, bronze, and recently with Invar, a nickel-based alloy that has become the material of choice for aerospace composite cure-tools because its coefficient of thermal expansion matches the parts being produced. In addition, Invar has durability and wear benefits.
AM&D: What are the largest parts you can produce?
MW: Basically, a 5ft cube, but it’s part- dependent. If narrower, we can print up to 9ft – limited only by the robot’s reach. We could use a larger robot or pedestal to raise the robot if the need arises to go beyond our current build volume. A couple of projects we’re working on are 14ft long. We’re printing 4ft to 5ft segments vertically and joining the segments, welded together post-printing. Printing shorter segments also shortens the cycle time.
AM&D: What are the benefits of producing tooling with metal AM?
MW: As parts become more complex, lead times and costs start to come down with AM. Tooling is the last item needed before a production run, so there’s always schedule pressure to produce the tooling as quickly as possible, and we see this as our advantage, as we can cut cycle and delivery times, especially for complex tools.
AM&D: What are some examples of complex tools?
MW: Anything with high curvature such as inlet ducts, exterior skins with intricate contour shapes, multiple angles, or bends. Traditionally, you can form tools from plate stock with bumping and forming blacksmithing skills or machine it from a billet. With our wire additive, we can rotate the part, and the robot motion lets you build a complex part without a support structure. It’s well-choreographed to control robot motion and torch angle while rotating and spinning the positioner holding the part. Multiple pieces of equipment are rotating, all programmed with SculptPrintTM software.

AM&D: How is Lincoln Electric offering AM services?
MW: Lincoln Electric is selling the metal AM 3D-printing service as a print bureau, using a dedicated 75,000ft2 facility in Cleveland, which currently has 18 production cells. We’re working with Baker Industries, which uses its 35 3- and 5-axis CNC centers for machining, prototyping, or tooling, or we provide a print for customers to machine from near-net.
AM&D: How does the service work?
MW: A customer comes with the solid model and prints of a finished part or a tool to produce, giving us the parameters. We can design to requirements or use a completed design or a variation between the two. Or bring us an existing design of a product you’re trying to produce. We’ll build to print or we can redesign it for AM, offering alternatives to reduce time or cost. Or bring us an existing part, where tooling or drawings no longer exist.
Baker Industries, A Lincoln Electric company
Get curated news on YOUR industry.
Enter your email to receive our newsletters.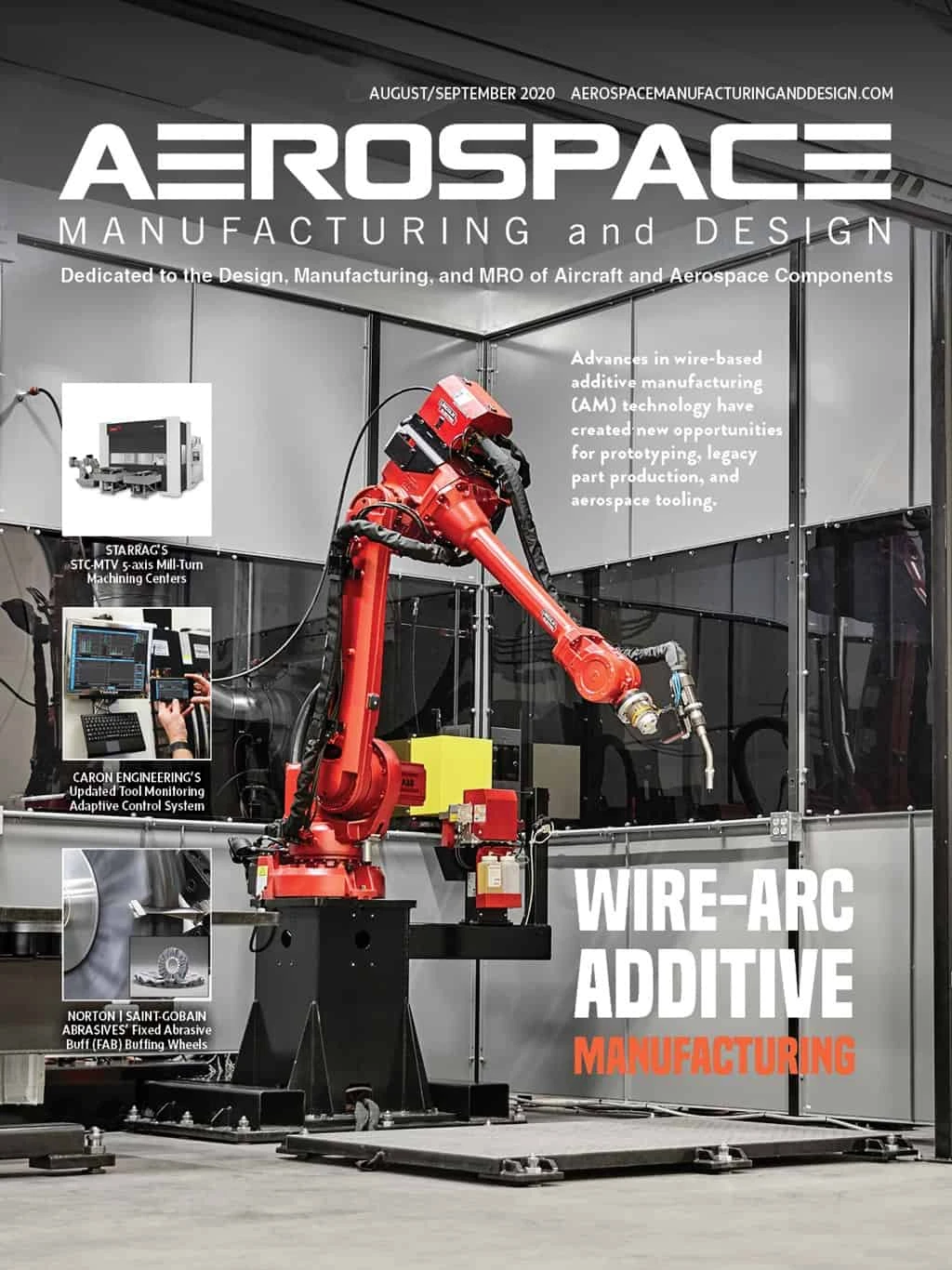
Explore the August September 2020 Issue
Check out more from this issue and find your next story to read.
Latest from Aerospace Manufacturing and Design
- Taiwan’s China Airlines orders Boeing 777X passenger, freighter jets
- Reamer re-tipping extends life of legacy tooling
- Revitalizing the Defense Maritime Industrial Base with Blue Forge Alliance
- Safran Defense & Space opens US defense HQ
- Two miniature absolute encoders join US Digital’s lineup
- Lockheed Martin completes Orion for Artemis II
- Cylinder CMMs for complex symmetrical workpieces
- University of Oklahoma research fuels UAS development