
As part of a NASA-funded study, University of Virginia (UVA) School of Engineering and Applied Science researchers showed airflow in supersonic combustion jet engines can be controlled by an optical sensor. The finding could lead to more efficient stabilization of hypersonic jet aircraft.
The researchers also achieved adaptive control of a scramjet engine – another first. Adaptive engine control systems keep the system’s overall performance optimal.
Professor Christopher Goyne, director of the UVA Aerospace Research Laboratory, where the research was done, and co-investigator Chloe Dedic, a UVA Engineering associate professor, believe optical sensors could be a big part of the control equation.
“If an aircraft operates at hypersonic speeds of Mach 5 and higher, it might be preferable to embed sensors working closer to the speed of light than the speed of sound,” Goyne says.
Supersonic combustion ramjets (scramjets) are built on proven ramjet technology using an aircraft’s forward motion to ram air into the engine to generate the temperatures and pressures needed to burn fuel – which happens about Mach 3 to Mach 6. As the ramjet’s inlet narrows, the internal air velocity slows to subsonic speeds. Scramjets have the same basic setup but must maintain super-fast airflow through the engine to reach hypersonic speeds.
“If something happens within the hypersonic engine, and subsonic conditions are suddenly created, it’s an unstart,” Goyne explains. “Thrust will suddenly decrease, and it may be difficult to restart the inlet.”
Scramjets need to get to a speed where they can take in enough oxygen to operate. The latest innovation is a dual-mode scramjet combustor, the engine type tested. The dual engine starts in ramjet mode at lower Mach numbers, then shifts into receiving full supersonic airflow in the combustion chamber at speeds exceeding Mach 5.
Goyne and his collaborators wondered if a pending unstart could be predicted by observing properties of the engine’s flame instead of sensing at the speed of sound – where engine processes exceed the speed of sound.
Optical sensors can identify subtle changes inside the engine. The tool analyzes the light emitted by the reacting gasses within the scramjet combustor – for spectral content and the flame’s location in the flow path. The different colors of light offer information about the engine’s state not captured by pressure sensors.
The team’s wind tunnel demonstration showed engine control can be smoothly transitioned between scramjet and ramjet functioning.
“We were very excited to demonstrate the role optical sensors may play in the control of future hypersonic vehicles,” doctoral student and first author Max Chern says. “We’re continuing to test sensor configurations as we work toward a prototype that optimizes package volume and weight for flight environments.”
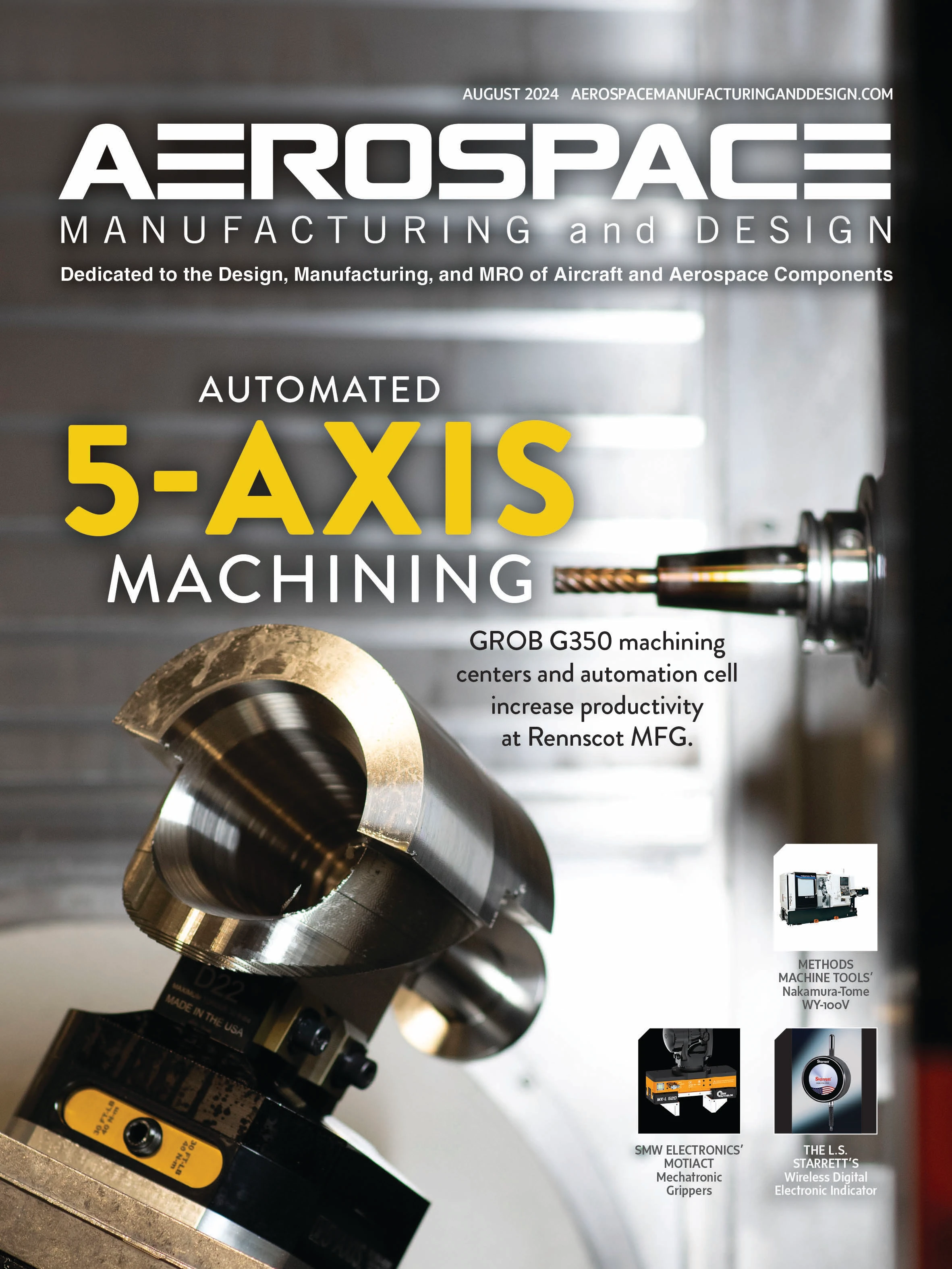
Explore the August 2024 Issue
Check out more from this issue and find your next story to read.
Latest from Aerospace Manufacturing and Design
- Revitalizing the Defense Maritime Industrial Base with Blue Forge Alliance
- Safran Defense & Space opens US defense HQ
- Two miniature absolute encoders join US Digital’s lineup
- Lockheed Martin completes Orion for Artemis II
- Cylinder CMMs for complex symmetrical workpieces
- University of Oklahoma research fuels UAS development
- Motorized vision measuring system
- Everyone's talking tariffs