
Haas Multigrind users manufacture a variety of workpieces ranging from intermediate pressure (IP) compressor blades, to high pressure (HP) turbine blades, HP vanes, or HP shroud segments for aircraft engine components in aircraft turbines, which are exposed to extreme thermal and physical stresses. The company deals with very demanding materials which are hard to machine and where only grinding can be used.
For the aerospace industry, Tim Kern, demonstrations manager at Haas Schleifmaschinen says engineers and technicians know what they want.
“In comparison to medical equipment, the technical specifications are much tighter in this sector,” Kern explains. “We have the technical ability to meet the high requirements which prevail in this sector – with our grinding software, our CNC grinders.”
Technical challenges
Wolfram Hermle, manager of software development at Haas Schleifmaschinen, with U.S. subsidiary Multigrind LLC located in Warsaw, Indiana, says the company’s customers want absolutely reliable, robust processes with which they can achieve reproducible quality.
“One component should be just the same as the next,” he says.
Kern adds, “These challenges from aero engine makers are just what we like to hear. Where possible, we only clamp a component once, then measure it and machine it in a single operation to produce the finished item. Having to re-clamp several times costs time.”
Hermle explains that the lost time costs the companies money and, above all, precision.
“Fewer clamping operations also means that the workpiece spends less time waiting around, thus shortening the cycle times,” Hermle says. “You have fewer half-finished, expensive components lying about, require less effort for quality assurance and measurements, and need less staff. They don’t have to operate five machines – just a single grinding machine.”
Quality assurance
“At Haas, we work with a variety of measurement technologies, including three-two-one measurements to exactly locate the workpiece in space,” Hermle says. In this type of measurement, three points define the plane, while two other points define the axis, and a third point is on the workpiece itself.
“This is nothing completely new, but so far it has not been common practice to use the integrated three-two-one measurement when grinding,” Hermle says. “Especially not in the way that we further process the result of the three-two-one measurement with our Multigrind Horizon grinding software. This automatically adapts the grinding program to the workpiece’s position in the working space.”
Application
With the Multigrind Horizon 3D-CAD package and the 3D-CAM package, Hermle says aerospace users can cover about 90% of grinding tasks in turbines.
“If users also want to machine teeth for drive functions, where sliding fits are important, then they will also need the package for rotationally symmetrical workpieces,” Hermle says. “All of the measurement functions and the dressing technology to dress the tools in the process are included in the basic package.”

Kern says casting high-pressure compressor blades is expensive and time consuming, in terms of the dimensional accuracy.
“The caster is responsible for the position of the part in this bismuth holder. That means that the process decides whether I get a good part or an expensive reject,” Kern says.
Hermle adds, “With the three-two-one measurement and Haas sandwich clamping, we have the technical ability to compensate for casting tolerances. When measuring a compressor blade, if deviations such as a visually imperceptible warp are revealed, then measurements will be introduced into our grinding program. We correct casting faults in the grinding process to permit optimum efficiency to be achieved for the engine.”

When dealing with turbine components, Haas uses alloys, titanium, titanium aluminum alloys, aluminum alloys, and ceramic coatings materials, that can withstand extreme stress.
“Important characteristics here include low weight, high operating temperature, and tensile strength,” Kern says.
Crucial grinding software
“Our grinding software is becoming more important and powerful, especially in the high-precision area where 0.001mm is important,” Kern says. “Our Multigrind Horizon can generate a lot more than grinding paths. It is a genuine CAM system, a grinding programming system, a tool management system, a robot-handling program, an interface to a measurement system and, operating software which is really easy to use.”
Haas’ grinding software has facets for the designer and the machine operator.
“Working with varying rights or user levels has the advantage that a validated grinding process, as required by the FAA, cannot be changed by an unauthorized person. This means that the Multigrind Horizon ensures traceability at all times of who changed what and when in the grinding process. This documentation of absolutely everything is mandatory in the aerospace industry,” Hermle says.
Hass finds that its aerospace users want a grinding process that has been properly tested to produce faultlessly from the very first day. For the company, this means developing robust processes and then automating it to work just as well in the United Kingdom as in France, China, or the United States.
Haas Multigrind LLC
IMTS 2016 Booth #N-7514
Get curated news on YOUR industry.
Enter your email to receive our newsletters.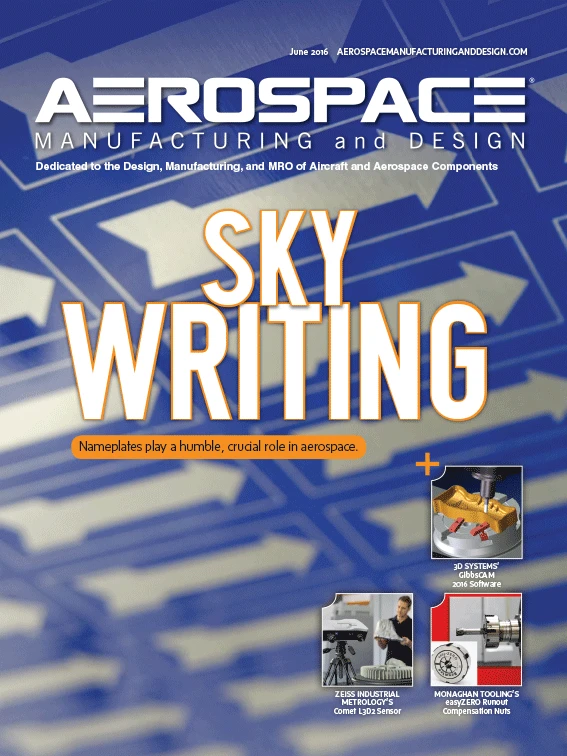
Explore the June 2016 Issue
Check out more from this issue and find your next story to read.
Latest from Aerospace Manufacturing and Design
- Ralliant to establish global headquarters in North Carolina
- Philatron MIL-DTL-3432 military cables
- Beyond Aero refines its hydrogen-electric light jet
- Americase's advanced protective solutions
- Social media - what are your thoughts
- GE Aerospace secures Air Force engine contract
- Thomson Industries' online sizing and selection tool
- #53 - Manufacturing Matters - 2024 Leaders in Manufacturing Roundtable