
Robot workers perform maintenance on an F-35 aircraft, using the Mold in Place (MIP) process.
The Ukrainian conflict and the pandemic caught many by surprise. The last time the world experienced similar concurrent developments was more than 100 years ago, when World War I coincided with the Spanish Flu pandemic. Such moments can be inflection points for major technological breakthroughs and changes to established production and manufacturing patterns. What if the people needed for manufacturing are too sick to work?
The answer: robots.
Robots don’t need sick days
The loss of hours and production have been major obstacles for companies and organizations since the pandemic began. Many American companies lost thousands of hours during the past two years due to employee exposure to COVID-19 and required quarantine or sick leave.
Those worker shortages have been a factor in slowing the supply chain, which is still not back to pre-2020 levels. Supply chain inefficiencies have affected nearly every American company, and we’ve felt the effects at our robotics solutions company in shipping delays for parts, in some cases lasting up to 3x longer than average.
Robots can help, as they won’t get sick. If they fail in their tasks, they can be serviced and put back into operation. In manufacturing, robots have advantages compared to human workers, but during a pandemic, robots’ durability is significantly heightened.
Robots don’t need security clearances
Many employees working for aerospace and defense (A&D) companies in the U.S. need to be background vetted and given security clearances. Even with these checks, their employers and the federal government will always have concerns about potential sabotage or espionage. Robots don’t need security clearances or background checks.
Additionally, once programmed, robots can run disconnected from networks, free from risk of compromise via targeted cyberattacks, one of the biggest threats to U.S. national security and corporate America. Robots can help reduce that threat.
Robots can work 24/7
Although they need some regular maintenance and supervision, robots work at a pace humans can’t sustain. Robots aren’t legally required to be allowed breaks or owed vacation time. Robots can work long periods in dull, dirty, and dangerous conditions (extreme temperatures, dust, chemicals, toxins), allowing people to work in safer environments.
Robots deliver products in less time
Due to their ability to be programmed to perform repeatable tasks, robots can complete work tasks efficiently, without mistakes. Quality is enhanced in production, with the added benefit of better process control.

Operations beyond the capabilities of humans, such as repeatedly lifting several hundred-pound objects, are easy for robots to perform, resulting in jobs being completed safer, faster, and better.
Many American companies chose to move production facilities offshore. In a stable global environment, this saves costs for these companies, but can leave companies vulnerable during times of instability. In a global environment that’s become more unstable, onshoring manufacturing to the United States is more attractive.
Robots and artificial intelligence (AI) could help make U.S.-based production jobs more viable. Many jobs that moved abroad are repetitive and dangerous. The robotization of manufacturing can move those jobs back to the U.S. Ultimately, the quality of life improves for Americans as factory employees are now highly skilled and higher paid robot technicians, programmers, and machine operators. In 2018, the World Economic Forum reported “Machines will do more tasks than humans by 2025 but the Robot Revolution will still create 58 million in net new jobs in the next five years.”
American A&D manufacturing companies must move toward robotics and AI to remain profitable and viable in the future. Now’s the time to embrace the efficiency and dependability of robotics before another possible combination of war and disease forces manufacturers to play catch-up.
NEWS AND PRODUCTS

High-accuracy, CAN output proximity sensor The CAN Output Proximity Sensor, the first sensor within the Crane FLEXtech product portfolio, supports direct CAN data bus connectivity and provides absolute gap measurement. Proximity sensors and switches detect a near-far relationship between the sensor and the actuating mechanism. The sensor provides absolute position and can communicate that information via CAN bus. Access to this information is vital for traditional aircraft, as well as unmanned aerial vehicles (UAVs) or in urban air mobility (UAM) and the emerging electrification of these platforms. Obtaining precise positioning also provides proactive warnings and supports prognostics systems that enhance operators’ maintenance systems and optimize efficiencies.
Crossed-roller linear bearing
NB Studroller crossed-roller linear bearings have fast acceleration and deceleration at dimensions ranging from 30mm to 600mm lengths, 1mm to 12mm rollers, and for 150 million cycles. Now added to the line-up is the NV-type Studroller with anti-creep cage technology for zero slippage.
By placing studs in the center roller and machining a correspondingly dimpled path in the rail, the retainer never slips.
Load capacities are increased 1.4x to 2.3x compared to the standard SV type. Roller-to-rail contact area is extended 42% to 58% while the number of rollers is increased 20% to 55%. Studroller lowers component costs and allows more compact designs.
Available configurations:NV – Sliding plate bearings feature four rails, eight retainers, and two end pieces. A retainer (resin or stainless steel) and built-in Studroller system keep bearings in place while a track base provides smooth movement and creep-free operation.
SV – Similar design and functionality to NV but with R-type roller cages arranged in a cross formation, minimizing friction resistance and are available in resin/steel and all-stainless steel constructions.
SVW – Linear roller bearings use a W-type rail for a more compact design while still offering many of the benefits of SV and NV cross rollers. Both stainless steel/resin (SVW) and all-stainless steel (SVWS) configurations are available.
Nippon Bearing Corp.WANT MORE?
Enter your email to receive our newsletters.
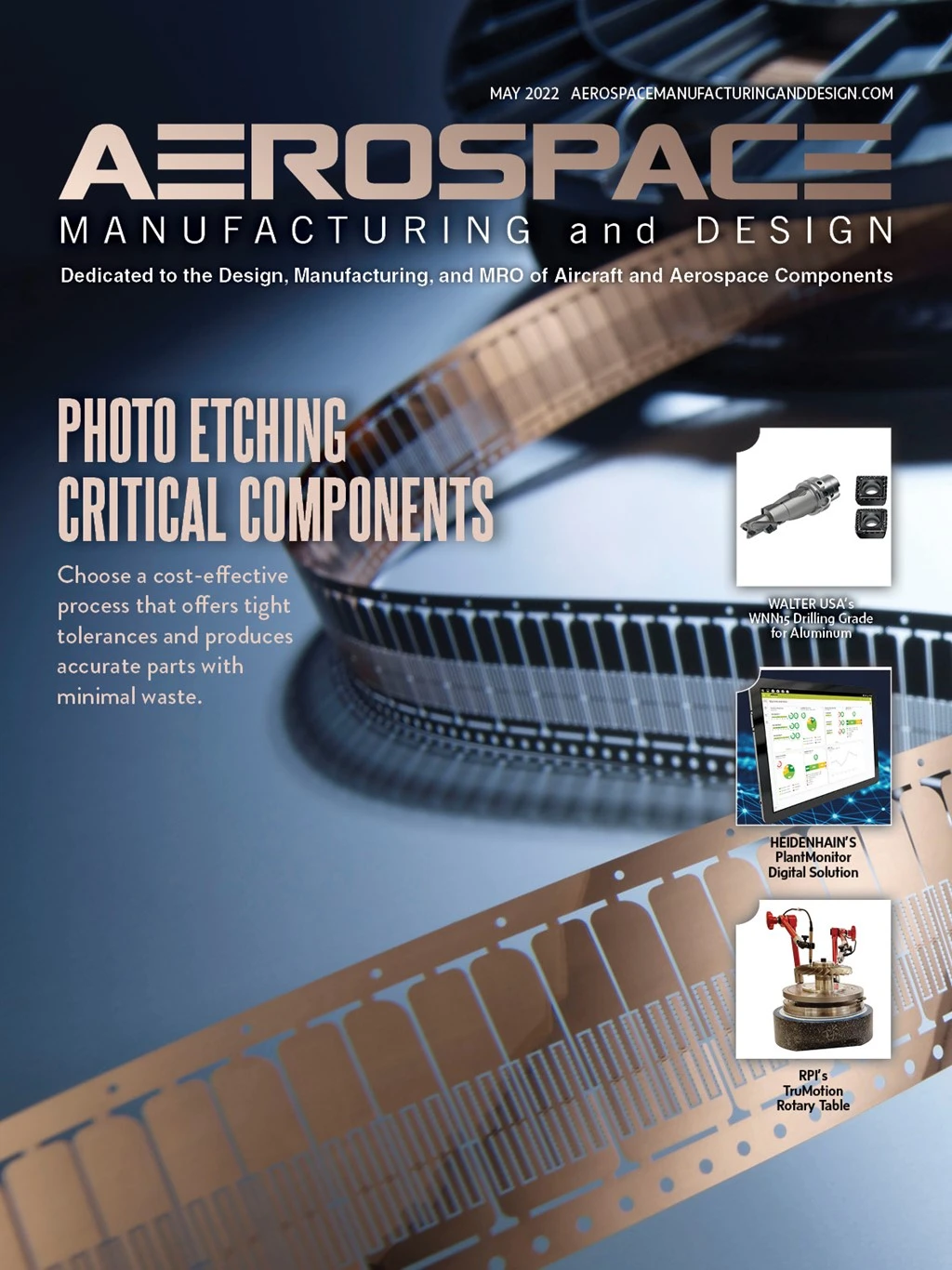
Explore the May 2022 Issue
Check out more from this issue and find your next story to read.
Latest from Aerospace Manufacturing and Design
- GE Aerospace awarded subcontract for FLRAA next phase
- KYOCERA Precision Tools publishes 2025-2026 Indexable Cutting Tools Catalog
- BOC Aviation orders 120 Airbus, Boeing jetliners
- Mazak’s INTEGREX j-Series NEO
- Embraer tests wing for new technologies demonstrator
- Mitutoyo America’s SJ-220 portable surface roughness tester
- #55 - Manufacturing Matters - A Primer on Defense Contract Manufacturing
- Registration is open for April’s Manufacturing Lunch + Learn!