Vacuum technology achieves effective, reliable hold-down of materials for printing, cutting, machining, measuring, application of coatings and adhesives, and other types of processing without using clamps or chucks. Inherent advantages include: faster, more accurate setups; access to entire surface of the workpiece; and lower potential to damage material or machine
From large industrial facilities cutting and machining steel to cleanrooms recording precise measurements of aerospace grade composites, vacuum table systems provide logistical solutions and operational advantages.
Although the principles of operation are the same in all vacuum table systems, design and construction vary widely depending on the application. Small tabletop systems may have a vacuum surface area of 1 in² while modular systems for industrial use may be expanded to hundreds of square feet. Stainless steel and aluminum are the most common surface materials – and generally preferred for heavy-duty use – while common variants include anodized
The precision of computer-controlled industrial processes such as CNC mills, lathes, routers, plasma cutters, and EDMs has led to an increased use of vacuum table systems during the last two decades. At the same time, high-tech composites and synthetic materials have grown more popular, creating a demand for clamp-free
“I don’t even know all of the potential
GPI’s customers demonstrate the versatility and variety of vacuum
Peak performance under pressure
A vacuum table system typically consists of a penetrable flat, rigid work surface, usually perforated or grid-style depending on the application; a plenum or vacuum chamber; and a vacuum pump large enough to create a sufficient pressure differential between the chamber and the ambient or atmospheric pressure at the surface to hold a workpiece in place. It is not
In a properly configured and calibrated vacuum
If the process generates excessive heat it may require the application of coolant during processing; if it generates excessive scrap material it may require cleaning during processing with blasts of compressed air.
In such

Look out for leaks
Air leaks and airflow inefficiencies account for most of the problems encountered when calibrating vacuum
A vacuum table system draws air through the
Again, efficient hold-down of the workpiece comes from balancing suction and system airflow. It’s critical the part is flat against the vacuum table surface. It is also important that the plenum be deep enough, and fittings
An airtight case
With an appropriate system properly configured and installed, business owners and production managers can reap the rewards of vacuum
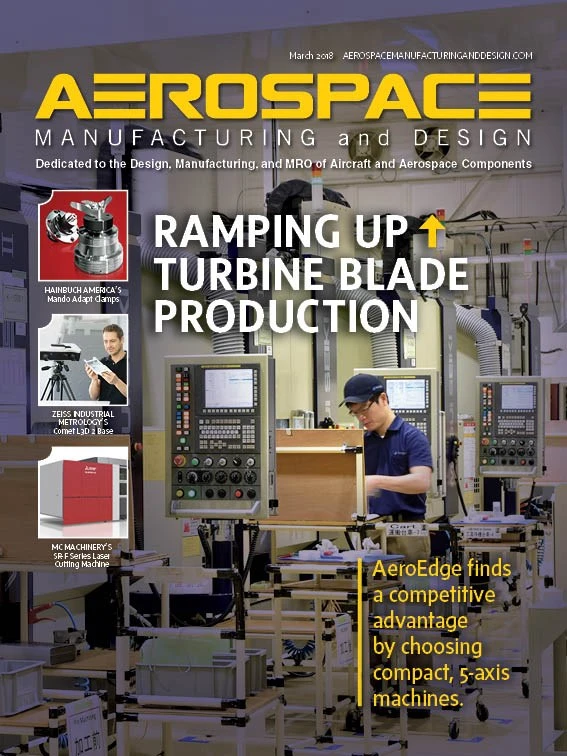
Explore the March 2018 Issue
Check out more from this issue and find your next story to read.
Latest from Aerospace Manufacturing and Design
- AIX shows aircraft interiors are a strategic priority for global airlines
- Machine Tool Builders Roundtable: Turn equipment into expertise
- No time to waste: How to machine MedTech parts more efficiently
- The 5 Best and Fastest Spindle Repair Services
- Mill smarter, not harder: How collaboration optimizes production
- Be proactive – stay ahead of tariffs and other economic and supply chain curveballs!
- Taiwan’s China Airlines orders Boeing 777X passenger, freighter jets
- Reamer re-tipping extends life of legacy tooling