
High concentrations of ice particles at high altitudes can threaten flight safety. Ice can accumulate very quickly in an aircraft engine during certain temperatures, flows, geometries, and ice crystal concentrations. Build-up can choke an engine within minutes, reducing it to idle. Ice shedding can damage engine components or cause a flame-out. Currently, no reliable sensor system exists that can provide pilots with early indications of ice crystal accretion, but the National Research Council of Canada (NRC) has developed an ultrasound ice accretion sensor to technology readiness level (TRL) 6.
The ultrasound ice accretion sensor is a small, thin, lightweight, non-intrusive device that has low power requirements. Using ultrasound, it acts as both a microphone and a speaker, sending out an acoustic wave that is reflected back, and providing data about conditions on the other side of the skin. The reflected acoustic signal is analyzed using methods developed at NRC.
Contrary to most sensors, the ultrasound sensor does not have to be placed within the environment being measured. It is applied to the non-exposed surface of an engine or aircraft component, eliminating the risk of it going through the engine or becoming damaged by ice and debris.
“Knowing where icing is likely to occur in an engine can be narrowed down – NRC’s Reducing Aviation Icing Risk research program has done years of work on that,” explains Dan Fuleki, icing group project manager at NRC. “So when we positioned this sensor in the right locations on the other side of the wall from the flow, we were able to determine that ice accretion was happening.”
During three years, the sensor was put through rigorous testing at NRC’s facilities for ice crystal icing investigation. Modifications to enhance the technology included improving performance and durability through changes to materials, cabling, and fabrication, and the development and testing of installation procedures. Finally, the sensor was ready to move to a definitive high-altitude ice-crystal-icing engine test.
The sensor was tested in November 2015 at NASA Glenn Research Center’s Propulsion Systems Laboratory. In partnership with Honeywell Engines and the Ice Crystal Consortium, which provided a test engine known to roll back to idle in certain icing conditions, the sensor was tested at 30,000ft in a real icing environment.

“The test gave us a valuable opportunity to evaluate the technology and the initial results are very positive,” Fuleki says. “We have been able to detect ice accretion in an actual engine icing environment, and have also seen that this sensor has sufficient sensitivity to distinguish between severe and light accretions, and in effect, to measure the accretion intensity.”
Incorporating the sensor into aircraft, along with other probes and radar technology, could help pilots avoid situations where they would have to contend with engine ice crystal icing, improving flight safety.
National Research Council Canada
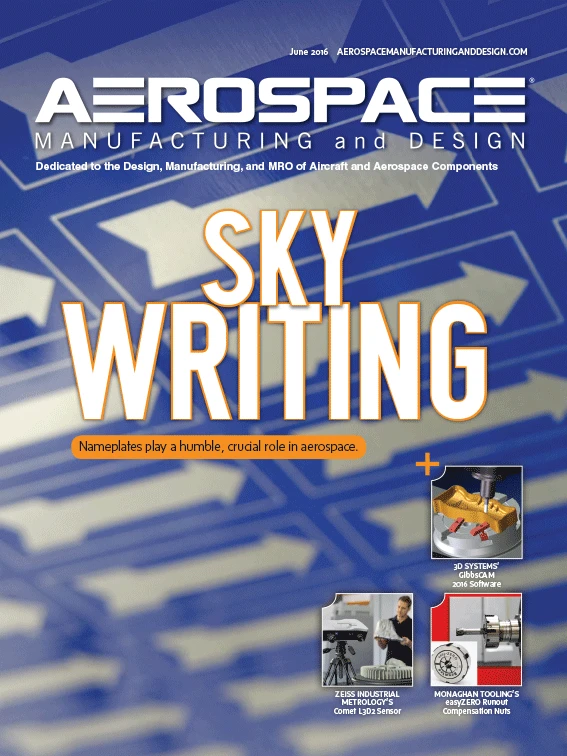
Explore the June 2016 Issue
Check out more from this issue and find your next story to read.
Latest from Aerospace Manufacturing and Design
- 2024 Favorites: #10 Article – How 3D-printed aviation parts can accelerate return to air
- 2024 Favorites: #10 News – Boom Supersonic completes Overture Superfactory
- OMIC R&D hosts Supporting Women in Manufacturing Day 2024
- 4D Technology's AccuFiz SWIR interferometer
- Seventh Lockheed Martin-built GPS III satellite launches
- KYOCERA AVX's CR Series high-power chip resistor
- UT researchers receive Air Force grant for wind tunnel
- Monticont's linear voice coil servo motor